The thickness of carbon coating for SEM typically ranges from 5 to 20 nanometers. This thin layer is applied to non-conductive samples to prevent charging and improve image quality by enhancing conductivity. The exact thickness depends on the sample's properties, the SEM's requirements, and the specific application. A thicker coating may be necessary for rough or porous samples, while a thinner coating is suitable for high-resolution imaging. The coating process is carefully controlled to ensure uniformity and avoid obscuring fine details of the sample.
Key Points Explained:
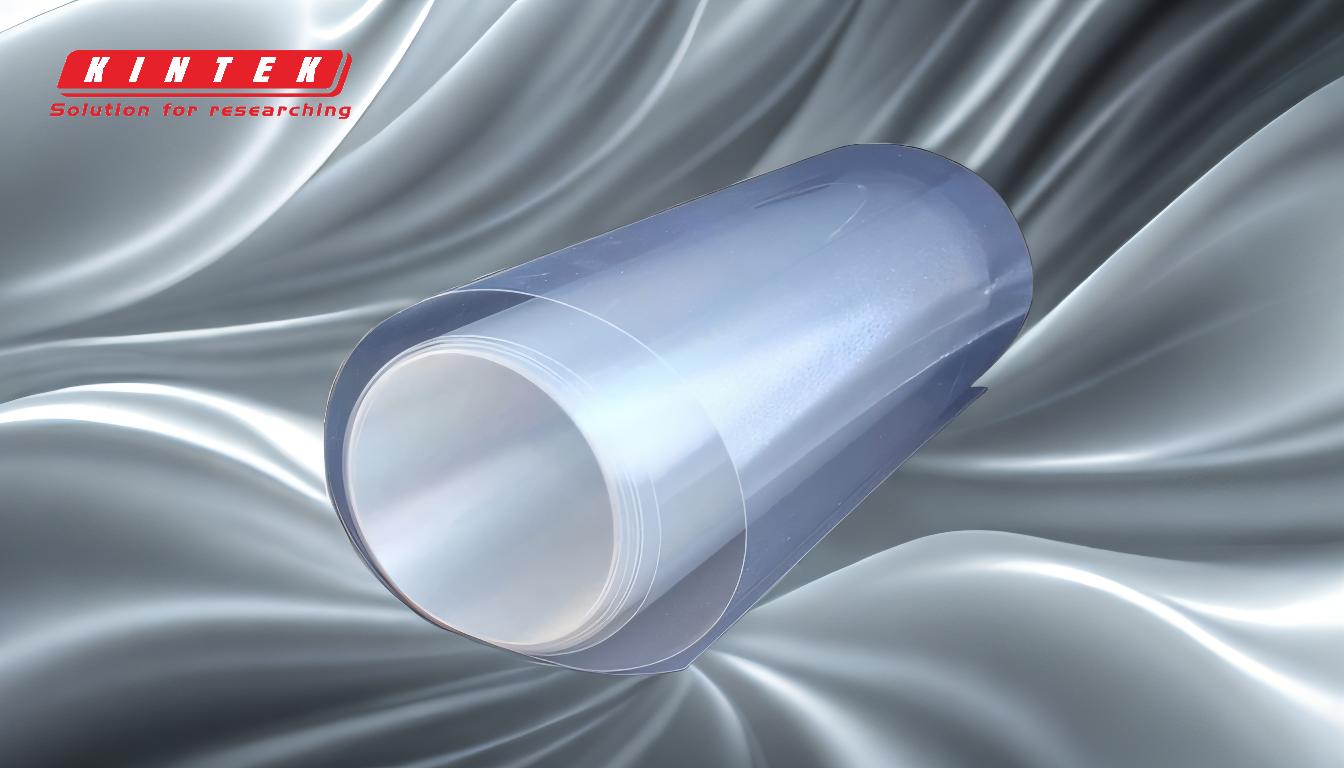
-
Purpose of Carbon Coating in SEM:
- Carbon coating is applied to non-conductive samples to prevent charging, which can distort SEM images.
- It enhances conductivity, ensuring better electron beam interaction and clearer imaging.
- The coating also protects delicate samples from beam damage during analysis.
-
Typical Thickness Range:
- The standard thickness for carbon coating in SEM applications is between 5 to 20 nanometers.
- This range balances conductivity enhancement with minimal interference with sample details.
-
Factors Influencing Coating Thickness:
- Sample Properties: Rough or porous samples may require a thicker coating to ensure full coverage.
- SEM Resolution Requirements: High-resolution imaging demands thinner coatings to avoid obscuring fine details.
- Application-Specific Needs: Some analyses, such as EDS (Energy Dispersive X-ray Spectroscopy), may require precise control over coating thickness to avoid interference with elemental analysis.
-
Coating Process and Uniformity:
- The coating is applied using techniques like sputter coating or evaporation, ensuring a uniform layer.
- Thickness is monitored using tools like quartz crystal microbalances or interferometers to maintain consistency.
-
Trade-offs in Coating Thickness:
- A thicker coating provides better conductivity but may obscure fine surface features.
- A thinner coating preserves sample details but may not fully eliminate charging in some cases.
-
Practical Considerations for Purchasers:
- When selecting coating equipment or services, consider the ability to control and measure coating thickness accurately.
- Ensure the coating process is compatible with the types of samples you frequently analyze.
- Evaluate the balance between cost, coating quality, and the specific needs of your SEM applications.
By understanding these key points, purchasers can make informed decisions about carbon coating thickness to optimize SEM performance and sample analysis.
Summary Table:
Aspect | Details |
---|---|
Purpose | Prevents charging, enhances conductivity, and protects samples. |
Typical Thickness | 5 to 20 nanometers. |
Factors Influencing Thickness | Sample properties, SEM resolution, and application-specific needs. |
Coating Process | Sputter coating or evaporation, ensuring uniformity and precise thickness. |
Trade-offs | Thicker coatings improve conductivity but may obscure fine details. |
Practical Considerations | Choose equipment/services that ensure accurate thickness control and compatibility with samples. |
Need help selecting the right carbon coating thickness for your SEM? Contact our experts today!