Vacuum casting is a manufacturing process used to create high-quality, detailed parts by pouring liquid material into a mold under vacuum conditions. This process is particularly useful for producing small batches of parts with intricate designs, as it minimizes air bubbles and ensures a high level of detail. The vacuum casting process typically involves several key steps, including mold preparation, material mixing, vacuum application, pouring, curing, and demolding. Each step must be carefully controlled to achieve the desired results. Below, we break down the process into detailed steps and explain the critical aspects of each stage.
Key Points Explained:
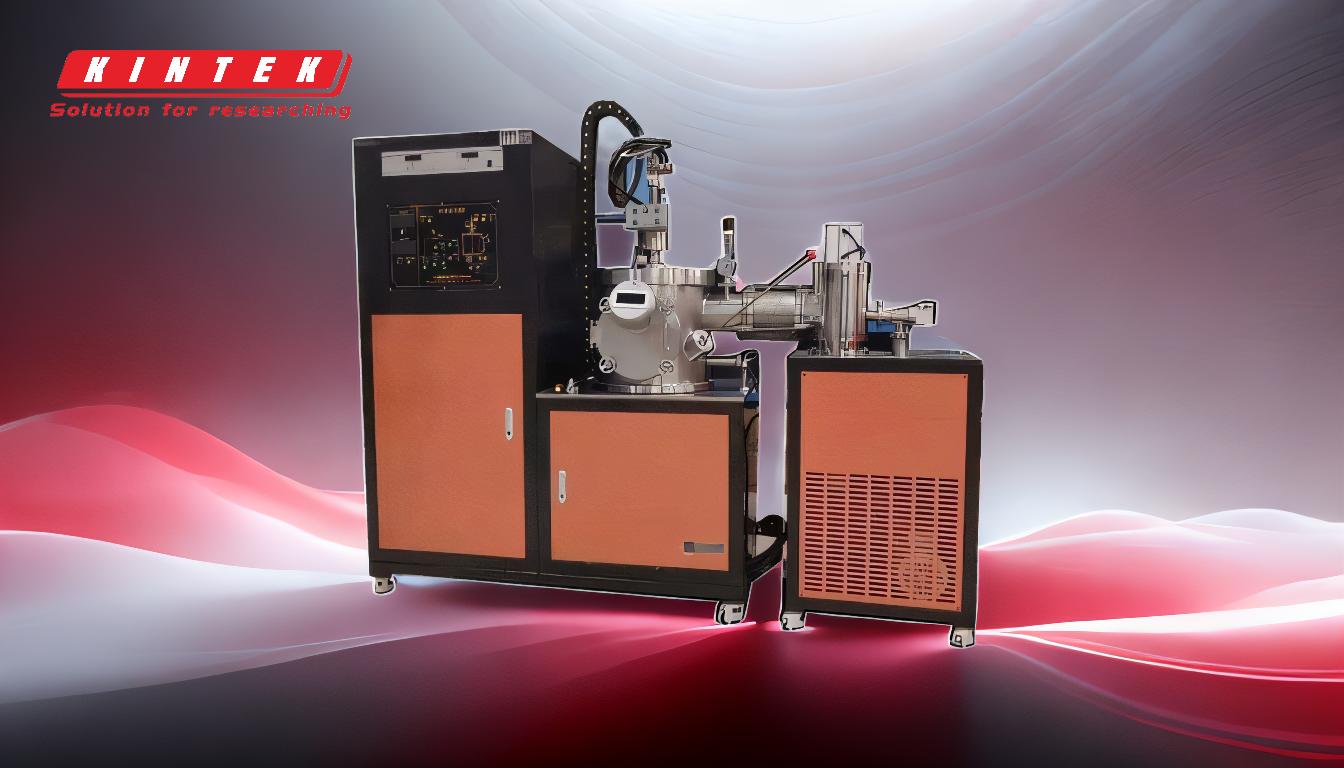
-
Mold Preparation:
- The first step in vacuum casting is preparing the mold. This involves creating a master model, typically using 3D printing or CNC machining, which is then used to make a silicone mold.
- The silicone mold is created by pouring liquid silicone around the master model and allowing it to cure. Once cured, the mold is cut open to remove the master model, leaving a cavity that matches the shape of the desired part.
- The mold must be cleaned and inspected for defects before use to ensure the final part's quality.
-
Material Mixing:
- The material used for vacuum casting is typically a two-part polyurethane resin. The resin and hardener are mixed in precise proportions to ensure proper curing and material properties.
- Mixing is done under vacuum to remove air bubbles from the resin, which could otherwise lead to defects in the final part.
- The mixed resin is then degassed further in the vacuum chamber to ensure it is free of trapped air.
-
Vacuum Application:
- The mold is placed inside a vacuum chamber, and the chamber is sealed. A vacuum pump is used to remove air from the chamber, creating a low-pressure environment.
- The vacuum helps to draw the liquid resin into the mold's cavities, ensuring that even intricate details are filled completely.
- The vacuum also helps to eliminate any remaining air bubbles in the resin, resulting in a smooth, defect-free surface.
-
Pouring and Curing:
- Once the vacuum is applied, the degassed resin is poured into the mold. The vacuum ensures that the resin flows evenly and fills all parts of the mold.
- After pouring, the mold is left to cure. Curing times vary depending on the resin used and the size of the part. Some resins require heat to cure, while others cure at room temperature.
- During curing, the resin solidifies and takes on the shape of the mold. It is important to monitor the curing process to ensure the part achieves the desired mechanical properties.
-
Demolding and Finishing:
- After the resin has fully cured, the mold is opened, and the part is carefully removed. Demolding must be done gently to avoid damaging the part or the mold.
- The part may require post-processing, such as trimming excess material, sanding, or painting, to achieve the final desired appearance and functionality.
- The silicone mold can often be reused multiple times, making vacuum casting a cost-effective method for small-batch production.
-
Equipment and Safety Considerations:
- Vacuum casting requires specialized equipment, including a vacuum chamber, vacuum pump, and mixing tools. Proper maintenance of this equipment is essential to ensure consistent results.
- Safety precautions must be taken when working with resins and vacuum equipment. This includes wearing protective gear, ensuring proper ventilation, and following manufacturer guidelines for material handling.
-
Advantages of Vacuum Casting:
- High level of detail and surface finish.
- Ability to produce small batches of parts cost-effectively.
- Versatility in material choice, with a wide range of resins available to mimic different properties (e.g., ABS-like, rubber-like, or transparent materials).
- Reusable molds reduce overall production costs for small runs.
-
Limitations of Vacuum Casting:
- Not suitable for large-scale production due to the time-intensive nature of the process.
- Limited by the durability of silicone molds, which may degrade after multiple uses.
- Material properties of cast parts may not match those of injection-molded parts, depending on the resin used.
By following these steps and considerations, vacuum casting can be a highly effective method for producing detailed, high-quality parts. The process requires careful attention to detail and proper equipment, but the results are often well worth the effort, especially for prototyping or small-batch manufacturing.
Summary Table:
Step | Key Details |
---|---|
Mold Preparation | Create a master model (3D printing/CNC), make a silicone mold, clean and inspect. |
Material Mixing | Mix two-part polyurethane resin under vacuum to remove air bubbles. |
Vacuum Application | Place mold in a vacuum chamber to ensure resin fills intricate details. |
Pouring and Curing | Pour resin into mold, cure under controlled conditions for optimal results. |
Demolding/Finishing | Remove part gently, perform post-processing (trimming, sanding, painting). |
Advantages | High detail, cost-effective small batches, versatile materials, reusable molds. |
Limitations | Not for large-scale production, mold durability, material property limitations. |
Ready to produce high-quality parts with vacuum casting? Contact our experts today to get started!