Using a press mold in ceramics is a technique that involves shaping clay or ceramic materials into a specific form by pressing them into or against a mold. This method is commonly used for creating consistent shapes and intricate designs. The process typically involves preparing the mold, lining it with clay, pressing the clay evenly, and allowing it to firm up before removing it. The mold can be made from bisque clay or plaster, and the pressing can be done manually or with the help of hydraulic presses for more uniform results. This technique ensures precision and repeatability, making it ideal for both artistic and industrial ceramic production.
Key Points Explained:
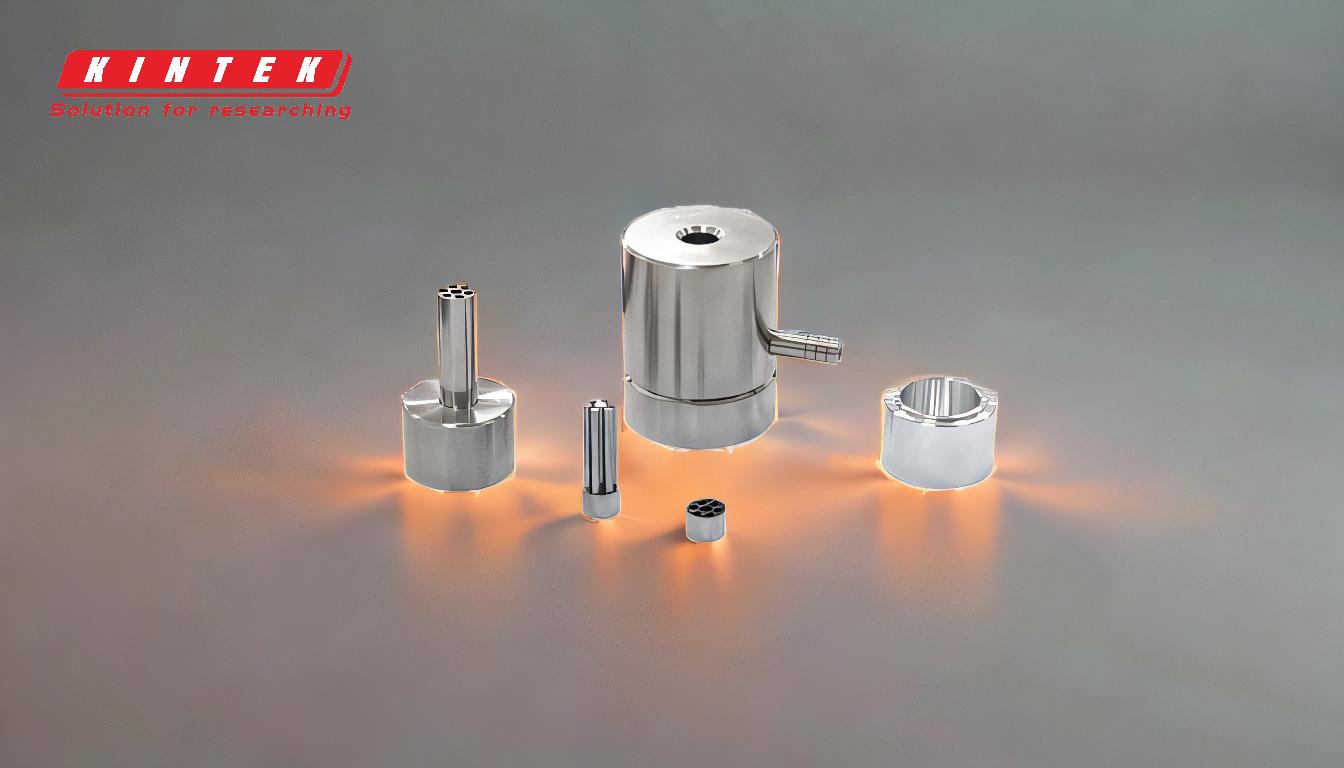
-
Understanding Press Molds in Ceramics
- Press molds are tools used to shape clay or ceramic materials into specific forms. They can be made from bisque clay (fired at 960-1000℃) or plaster. These molds are essential for creating consistent and intricate designs in ceramic work.
- The choice of material for the mold depends on the desired outcome and the type of clay being used. Plaster molds are porous and help in absorbing moisture from the clay, making it easier to release the formed piece.
-
Preparing the Mold
- Before using the press mold, ensure it is clean and free from any debris or old clay residues. This helps in achieving a smooth surface on the final product.
- If using a plaster mold, it should be slightly damp to prevent the clay from sticking too much. For bisque molds, ensure they are dry and free from cracks.
-
Lining the Mold with Clay
- Roll out a slab of fresh clay to an even thickness. The thickness should be consistent to ensure uniform pressing and drying.
- Carefully place the clay slab onto the mold, ensuring it covers the entire surface without any gaps or air pockets. Gently press the clay into the mold, starting from the center and moving outwards.
-
Pressing the Clay
- Use your hands or a soft tool to press the clay gently and evenly into the mold. Ensure that the clay is pressed into all the details and contours of the mold.
- For more uniform results, especially in industrial settings, hydraulic presses can be used. These presses apply isostatic or axial pressure to ensure even distribution of force, leading to better mechanical performance and dimensional accuracy.
-
Allowing the Clay to Firm Up
- After pressing, allow the clay to firm up slightly before attempting to remove it from the mold. This helps in maintaining the shape and prevents deformation.
- The drying time can vary depending on the type of clay and the thickness of the slab. It’s important to monitor the clay to ensure it doesn’t dry out too much, making it difficult to remove.
-
Detaching the Clay from the Mold
- Once the clay has firmed up, carefully detach it from the mold. Start by gently lifting the edges and then slowly peeling the clay away from the mold.
- If the clay sticks, you can use a thin tool to help release it, but be careful not to damage the surface.
-
Finishing Touches
- After removing the clay from the mold, inspect it for any imperfections or air bubbles. Smooth out any rough edges or surfaces using a sponge or a soft tool.
- Allow the formed piece to dry completely before proceeding to the next steps, such as bisque firing or glazing.
-
Advantages of Using Press Molds
- Consistency: Press molds allow for the creation of multiple identical pieces, which is particularly useful for production runs.
- Precision: The molds capture fine details, making it possible to create intricate designs with high accuracy.
- Efficiency: Using press molds can significantly speed up the production process, especially when combined with hydraulic presses.
-
Considerations for Industrial Applications
- In industrial settings, semi-isostatic pressing is often used to ensure uniformity and optimize mechanical performance. This technique involves applying pressure uniformly from all directions, resulting in a more consistent product.
- The use of hydraulic presses in these settings allows for precise control over the pressure applied, leading to better dimensional features and overall quality.
By following these steps and considerations, you can effectively use press molds in ceramics to create detailed, consistent, and high-quality pieces. Whether you're working on a small artistic project or a large industrial production, understanding the nuances of press molding will help you achieve the best results.
Summary Table:
Step | Key Actions |
---|---|
1. Understanding Molds | Use bisque clay or plaster molds for consistent and detailed ceramic designs. |
2. Preparing the Mold | Clean and dampen plaster molds or ensure bisque molds are dry and crack-free. |
3. Lining with Clay | Roll clay to even thickness and press into the mold, covering all surfaces. |
4. Pressing the Clay | Use hands, tools, or hydraulic presses for uniform pressure and fine details. |
5. Firming Up | Allow clay to firm up slightly before removal to maintain shape. |
6. Detaching the Clay | Gently peel clay from the mold, using tools if necessary to avoid damage. |
7. Finishing Touches | Smooth imperfections and let the piece dry completely before further processing. |
8. Advantages | Consistency, precision, and efficiency in ceramic production. |
9. Industrial Tips | Use semi-isostatic pressing and hydraulic presses for uniform, high-quality results. |
Ready to elevate your ceramic projects? Contact us today to learn more about press molds and techniques!