Annealing is indeed commonly performed in a furnace, and the type of furnace used depends on the specific requirements of the annealing process. Furnaces provide a controlled environment necessary for achieving the desired material properties, such as stress relief, improved ductility, and refined microstructure. Bright annealing, vacuum annealing, and solution annealing are examples of processes that utilize specialized furnaces to ensure optimal results. The furnace atmosphere, temperature, and cooling rate are critical factors that influence the outcome of the annealing process.
Key Points Explained:
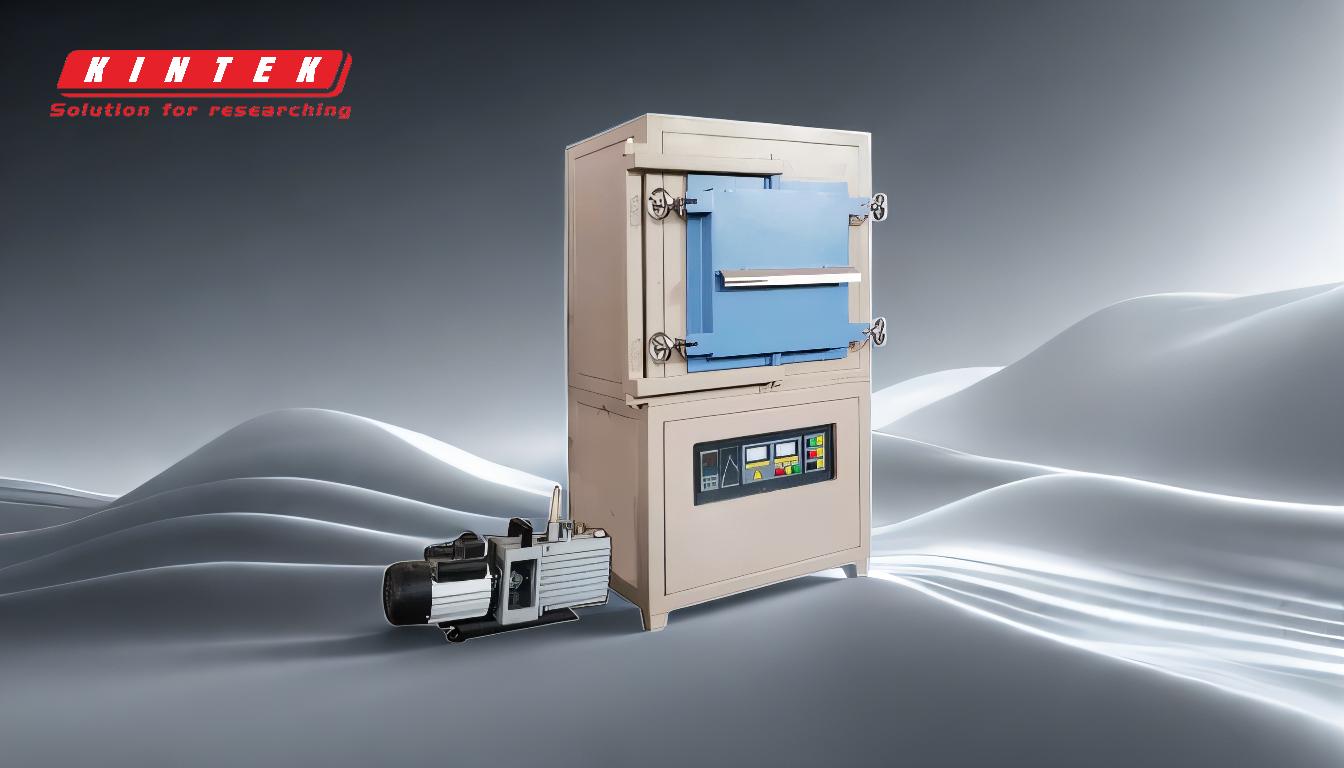
-
Types of Annealing Furnaces:
- Bright Annealing Furnace: This furnace is specifically designed for heat treatment under a protective atmosphere, preventing oxidation and maintaining the metal's surface brightness. It is commonly used for stainless steel products.
- Vacuum Annealing Furnace: Suitable for solution treatment and aging of large and medium-sized parts, this furnace operates in a vacuum to eliminate oxidation and contamination.
- Controlled Atmosphere Furnace: Used for annealing processes where oxidation and decarburization must be avoided, particularly for stainless steels and non-ferrous metals.
-
Purpose of Annealing:
- Annealing is primarily used to relieve internal stresses induced during manufacturing processes, such as casting or cold working. This improves the material's ductility and reduces brittleness.
- It also refines the material's microstructure, enhancing its mechanical properties and making it more suitable for further processing or end-use applications.
-
Solution Annealing:
- Solution annealing is a specific type of annealing used for austenitic stainless steels. It involves heating the material to temperatures between 900 °C and 1100 °C to dissolve precipitation phases like carbides into the matrix.
- Rapid cooling after heating prevents the re-separation of carbides and reduces cold hardening, resulting in a more uniform and less strained structure.
-
Importance of Furnace Atmosphere:
- A controlled atmosphere is essential in annealing to prevent surface oxidation and decarburization, which can compromise the material's properties and appearance.
- Protective atmospheres, such as inert gases or vacuum environments, are used to ensure consistent and reproducible results, especially for stainless steels and non-ferrous metals.
-
Temperature and Cooling Control:
- The annealing process requires precise temperature control to achieve the desired material properties. For example, solution annealing typically involves heating to high temperatures (900–1100 °C) followed by rapid cooling.
- The cooling rate is critical in determining the final microstructure and mechanical properties of the material.
In summary, furnaces are indispensable for annealing processes due to their ability to provide controlled environments, precise temperature regulation, and protective atmospheres. The choice of furnace depends on the specific annealing requirements, such as bright annealing for surface quality or vacuum annealing for oxidation-free treatment.
Summary Table:
Aspect | Details |
---|---|
Types of Furnaces | Bright Annealing, Vacuum Annealing, Controlled Atmosphere Furnace |
Purpose of Annealing | Relieves internal stresses, improves ductility, refines microstructure |
Solution Annealing | Dissolves carbides in austenitic stainless steels, followed by rapid cooling |
Furnace Atmosphere | Prevents oxidation and decarburization using inert gases or vacuum |
Temperature Control | Precise heating (900–1100 °C) and rapid cooling for desired properties |
Need the right furnace for your annealing process? Contact our experts today to find the perfect solution!