Brazing is indeed a joining process, and it stands out due to its unique advantages over other methods like welding or soldering. It involves joining materials by heating them to a specific temperature and using a filler metal that melts at a lower temperature than the base materials. This process allows for strong, durable joints without melting the base metals, making it ideal for applications requiring precision, complex geometries, or joining dissimilar materials. Below, we’ll explore the key aspects of brazing as a joining process and why it is widely used in various industries.
Key Points Explained:
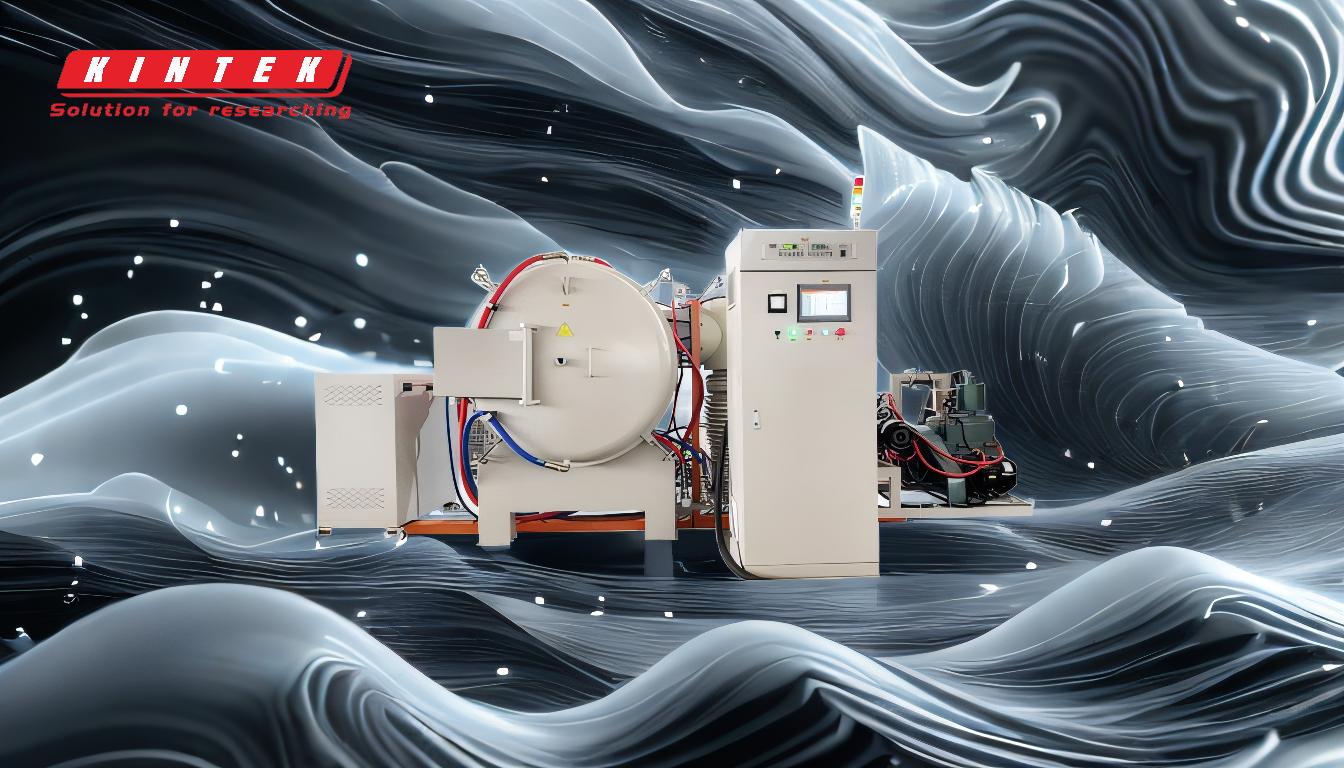
-
Brazing as a Joining Process
- Brazing is a metal-joining process where a filler metal is heated above its melting point and distributed between two or more close-fitting parts by capillary action. The filler metal bonds with the base materials, creating a strong, permanent joint.
- Unlike welding, the base metals are not melted during brazing, which preserves their structural integrity and allows for precise, high-tolerance joints.
-
Advantages of Brazing Over Other Joining Methods
- No Melting of Base Metals: Since the base metals are not melted, brazing maintains their original properties and dimensions, making it ideal for applications requiring close tolerances.
- Versatility in Joining Dissimilar Materials: Brazing can join a wide range of materials, including metals, ceramics, and composites, even when they have different melting points or thermal expansion rates.
- Reduced Thermal Distortion: The lower temperatures used in brazing compared to welding minimize thermal distortion, which is critical for maintaining the shape and alignment of components.
- Cost-Effectiveness for Complex Parts: Brazing is well-suited for joining intricate or complex parts, as the filler metal flows into tight spaces, creating uniform and reliable joints.
- High-Volume Production: The process is scalable and efficient, making it suitable for mass production in industries like automotive, aerospace, and electronics.
-
Applications of Brazing
- Brazing is widely used in industries where strong, leak-proof, and precise joints are required. Examples include:
- Automotive: Joining heat exchangers, radiators, and air conditioning components.
- Aerospace: Assembling turbine blades, fuel systems, and structural components.
- Electronics: Creating connections in circuit boards and semiconductor devices.
- HVAC Systems: Fabricating copper tubing and refrigeration systems.
- Brazing is widely used in industries where strong, leak-proof, and precise joints are required. Examples include:
-
Types of Brazing Techniques
- Torch Brazing: Uses a gas flame to heat the filler metal and base materials.
- Furnace Brazing: Involves heating parts in a controlled atmosphere furnace, ideal for high-volume production.
- Induction Brazing: Uses electromagnetic induction to heat the joint, offering precise and localized heating.
- Dip Brazing: Submerges the assembly in a molten salt or metal bath to achieve uniform heating.
-
Considerations for Equipment and Consumables
- Filler Metals: Commonly used filler metals include silver, copper, nickel, and aluminum alloys, chosen based on the base materials and application requirements.
- Fluxes: Fluxes are used to clean the surfaces and prevent oxidation during the brazing process.
- Equipment: Depending on the technique, equipment such as torches, furnaces, induction coils, or dip baths are required.
In summary, brazing is a highly effective joining process that offers numerous advantages, including precision, versatility, and cost-effectiveness. Its ability to join dissimilar materials and reduce thermal distortion makes it a preferred choice in many industries. By understanding the principles and techniques of brazing, equipment and consumable purchasers can make informed decisions to meet their specific joining needs.
Summary Table:
Aspect | Details |
---|---|
Process | Joins materials using a filler metal without melting base metals. |
Advantages | No melting of base metals, joins dissimilar materials, reduces distortion. |
Applications | Automotive, aerospace, electronics, HVAC systems. |
Techniques | Torch, furnace, induction, and dip brazing. |
Equipment & Consumables | Filler metals, fluxes, torches, furnaces, induction coils, dip baths. |
Ready to explore how brazing can enhance your projects? Contact us today for expert advice!