Pyrolysis is not the same as burning, although both processes involve the application of heat to organic materials. Burning, or combustion, requires oxygen and results in the release of heat, light, and combustion byproducts like ash and carbon dioxide. Pyrolysis, on the other hand, occurs in the absence of oxygen and involves the thermal decomposition of materials into gases, liquids, and solid char. This process is used to convert biomass, plastics, and other carbonaceous materials into renewable products like biochar and syngas, making it more environmentally friendly compared to combustion or incineration.
Key Points Explained:
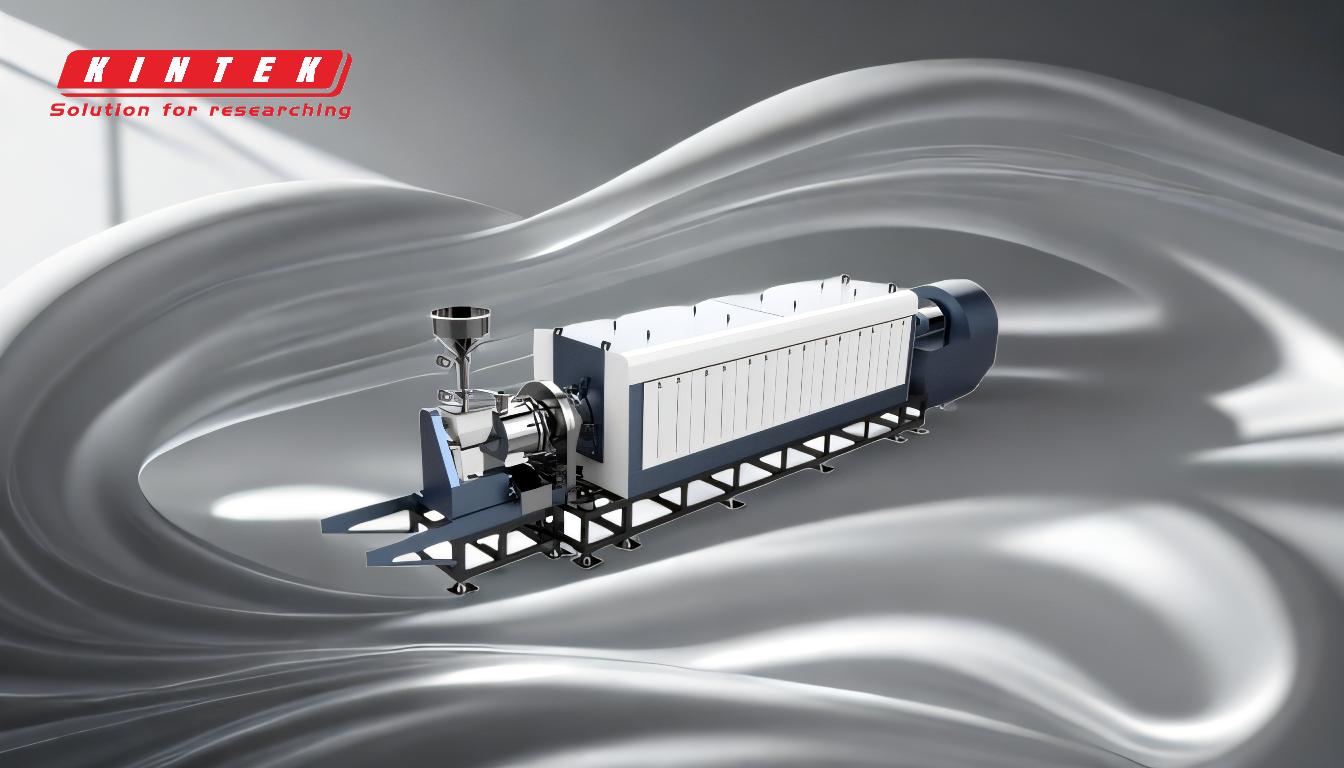
-
Definition of Pyrolysis vs. Combustion:
- Pyrolysis: A thermal decomposition process that occurs in the absence of oxygen, breaking down materials into gases, liquids, and solid char. It is used to convert biomass, plastics, and tires into renewable products like biochar and syngas.
- Combustion: A chemical process that involves burning materials in the presence of oxygen, releasing heat, light, and byproducts like ash and carbon dioxide.
-
Environmental Impact:
- Pyrolysis: More environmentally friendly as it does not produce harmful emissions like combustion. It converts waste materials into useful products, reducing landfill use and promoting recycling.
- Combustion: Releases carbon dioxide and other pollutants into the atmosphere, contributing to air pollution and climate change.
-
Temperature and Duration:
- Pyrolysis: Operates at lower temperatures (350-550 degrees Celsius) over several hours, allowing for controlled decomposition of materials.
- Incineration: Occurs at higher temperatures (800-1000 degrees Celsius) over a few minutes, leading to rapid oxidation and destruction of materials.
-
Products of Pyrolysis:
- Gases: Syngas, which can be used as a fuel.
- Liquids: Bio-oil, which can be refined into biofuels.
- Solids: Biochar, which can be used as a soil amendment or in carbon sequestration.
-
Applications of Pyrolysis:
- Biomass Conversion: Converts agricultural waste, wood, and other biomass into renewable energy sources.
- Plastic and Tire Recycling: Breaks down non-biodegradable materials into reusable products, reducing environmental pollution.
-
Comparison with Cracking:
- Cracking: A chemical process used in the oil and gas industry to break down large hydrocarbon molecules into smaller ones using heat and pressure.
- Pyrolysis: A thermal process used for biomass and waste conversion, breaking down materials in the absence of oxygen.
-
Technological Variations:
- Input Materials: Pyrolysis can handle a wide range of materials, including biomass, plastics, and tires.
- Size and Scale: Pyrolysis technologies vary widely, from small-scale units for local use to large industrial facilities.
- Products and Pricing: The end products and cost of pyrolysis depend on the technology used and the input materials.
In summary, pyrolysis is a distinct process from burning, offering a more sustainable and environmentally friendly method for converting waste materials into valuable resources. Its applications in biomass conversion, plastic recycling, and tire recycling make it a key technology in the transition to a circular economy.
Summary Table:
Aspect | Pyrolysis | Combustion |
---|---|---|
Definition | Thermal decomposition in the absence of oxygen. | Burning materials in the presence of oxygen. |
Environmental Impact | Produces no harmful emissions; converts waste into useful products. | Releases CO2 and pollutants, contributing to air pollution and climate change. |
Temperature | 350-550°C over several hours. | 800-1000°C over a few minutes. |
Products | Gases (syngas), liquids (bio-oil), and solids (biochar). | Heat, light, ash, and carbon dioxide. |
Applications | Biomass conversion, plastic and tire recycling, renewable energy production. | Energy generation, waste disposal. |
Ready to explore how pyrolysis can transform your waste management? Contact us today for expert guidance!