Sintering and melting are fundamentally different processes, primarily distinguished by whether the material undergoes liquefaction. Melting involves heating a material to its melting point, transforming it from a solid to a liquid state. In contrast, sintering uses heat and pressure to fuse particles without reaching the energy threshold required for liquefaction. This allows sintering to occur at lower temperatures, preserving the material's structure and shape while enhancing properties like strength and hardness. Sintering is particularly useful for materials with high melting points, offering greater control and consistency in manufacturing.
Key Points Explained:
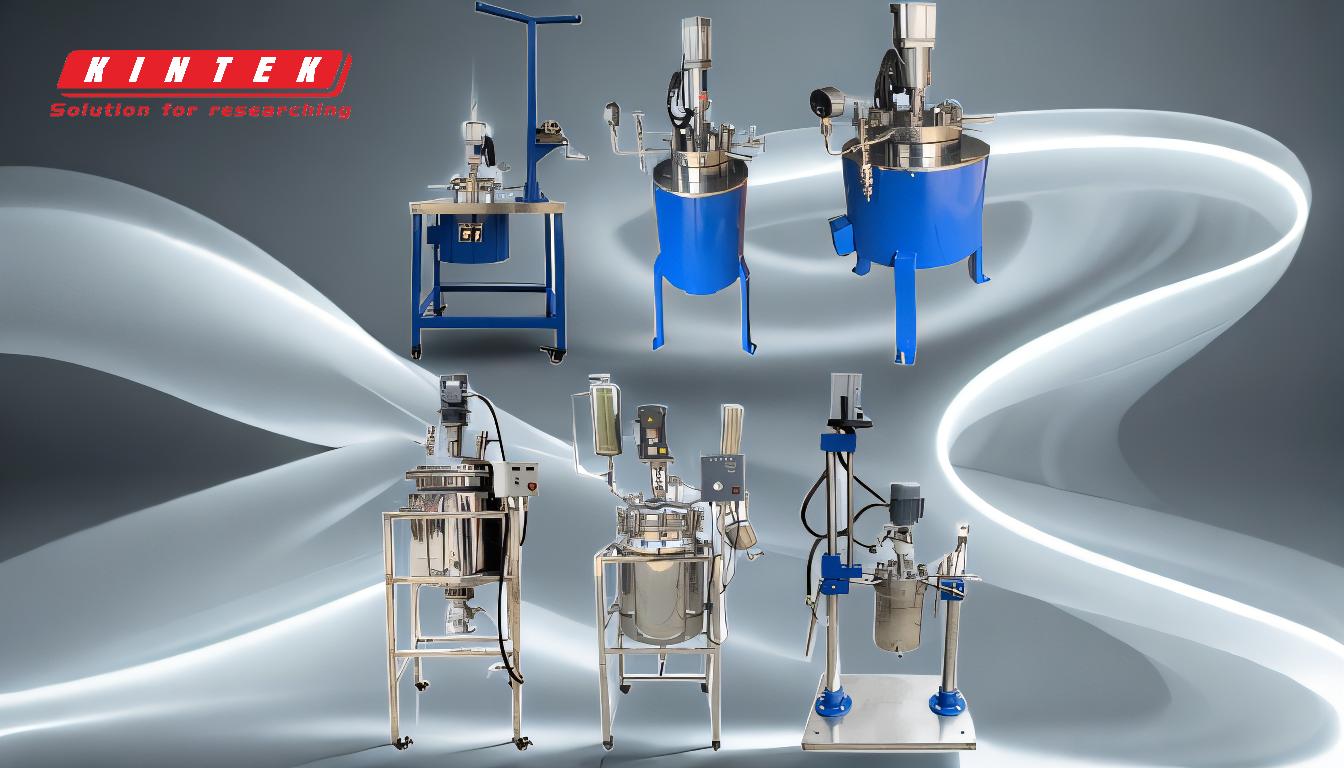
-
Definition and Purpose:
- Melting: The process of heating a material until it transitions from a solid to a liquid state. This requires sufficient thermal energy to break the bonds holding the solid together.
- Sintering: A process that uses heat and pressure to fuse particles without liquefying the material. It occurs at temperatures below the material's melting point, preserving its structural integrity.
-
Energy Requirements:
- Melting: Requires high temperatures to achieve the energy threshold necessary for liquefaction. This makes it energy-intensive.
- Sintering: Operates at lower temperatures, making it more energy-efficient compared to melting. This is particularly advantageous for materials with high melting points.
-
Material State:
- Melting: Results in a complete phase change from solid to liquid. This can alter the material's properties and structure.
- Sintering: Maintains the material in a solid state, allowing for the creation of complex shapes and structures without the risk of deformation.
-
Applications:
- Melting: Commonly used in processes like casting, where the liquid material is poured into molds to form desired shapes.
- Sintering: Widely used in powder metallurgy and ceramic manufacturing. It is ideal for creating parts from metals and ceramics with high melting points, enhancing properties like strength and hardness.
-
Control and Consistency:
- Melting: Can be less predictable due to the complete phase change, which may lead to inconsistencies in the final product.
- Sintering: Offers greater control over the final product's properties and consistency, as the material does not undergo a phase change.
-
Microscopic Gaps:
- Melting: Typically results in a fully dense material with minimal microscopic gaps due to the complete liquefaction.
- Sintering: May leave microscopic gaps between particles, which can affect the material's density and mechanical properties. However, these gaps can be minimized with proper sintering techniques.
-
Equipment:
- Melting: Requires furnaces capable of reaching high temperatures, such as induction furnaces or arc furnaces.
- Sintering: Utilizes specialized sintering furnaces designed to maintain precise temperature and pressure conditions.
Understanding these key differences helps in selecting the appropriate process based on the material properties and the desired outcome. Sintering is particularly beneficial for manufacturing parts from high-melting-point materials, offering a balance between energy efficiency and material integrity.
Summary Table:
Aspect | Melting | Sintering |
---|---|---|
Definition | Heating material to its melting point, transforming it into a liquid state. | Fusing particles using heat and pressure without liquefying the material. |
Energy Requirements | High temperatures required; energy-intensive. | Lower temperatures; more energy-efficient. |
Material State | Complete phase change from solid to liquid. | Maintains solid state; no phase change. |
Applications | Used in casting and molding. | Ideal for powder metallurgy and ceramics. |
Control & Consistency | Less predictable due to phase change. | Greater control and consistency. |
Microscopic Gaps | Fully dense material with minimal gaps. | May leave microscopic gaps; can be minimized. |
Equipment | Requires high-temperature furnaces. | Uses specialized sintering furnaces. |
Need help choosing the right process for your materials? Contact our experts today!