Spark Plasma Sintering (SPS) is not considered additive manufacturing (AM) in the traditional sense. While both SPS and AM involve the creation of parts or components, they differ fundamentally in their processes and principles. SPS is a powder metallurgy technique that uses electrical current and pressure to sinter powdered materials into dense components, whereas AM builds parts layer by layer from a digital model. SPS is more aligned with traditional sintering methods, albeit with enhanced efficiency and precision, and does not involve the layer-by-layer deposition characteristic of AM.
Key Points Explained:
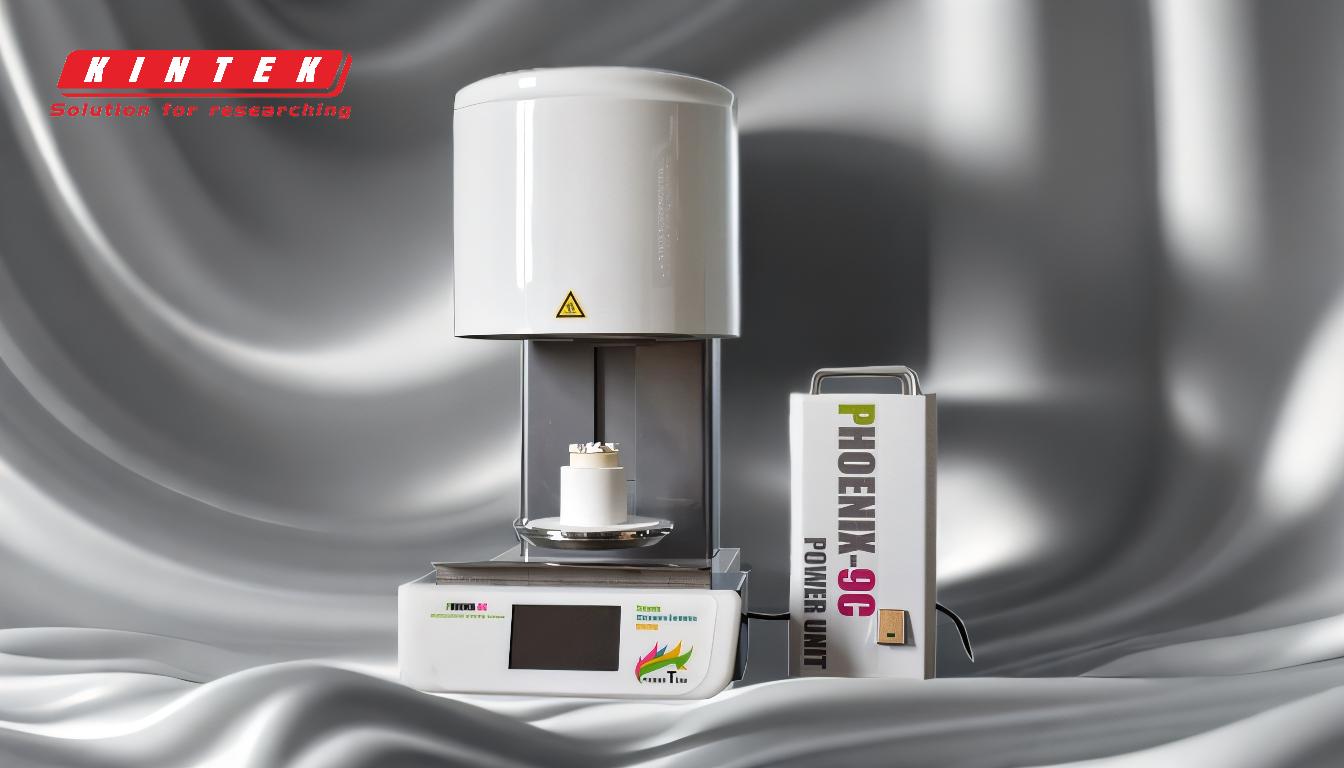
-
Definition of Additive Manufacturing (AM):
- AM refers to processes that create objects by adding material layer by layer, based on a digital 3D model. Examples include 3D printing techniques like Fused Deposition Modeling (FDM), Selective Laser Sintering (SLS), and Stereolithography (SLA).
- AM is characterized by its ability to produce complex geometries with minimal waste, as material is only added where needed.
-
Definition of Spark Plasma Sintering (SPS):
- SPS is a sintering technique that uses a pulsed direct current (DC) and uniaxial pressure to densify powdered materials into solid components.
- The process involves placing powder in a die and applying both heat (generated by the electrical current) and pressure to achieve densification.
- SPS is known for its rapid heating rates, which can lead to the formation of unique microstructures and enhanced material properties.
-
Key Differences Between SPS and AM:
- Process Mechanism: AM builds parts layer by layer, whereas SPS consolidates powder into a solid part in a single step.
- Material Addition: In AM, material is added incrementally to form the final part. In SPS, the material (powder) is pre-placed in a die and consolidated under pressure and heat.
- Complexity of Parts: AM excels in creating complex, intricate geometries that would be difficult or impossible to achieve with traditional methods. SPS, while capable of producing high-density parts, is generally used for simpler shapes.
- Material Waste: AM minimizes waste by adding material only where needed. SPS, being a powder-based process, may involve some material loss during handling and processing.
-
Applications of SPS:
- SPS is widely used in the production of advanced ceramics, composites, and metallic materials.
- It is particularly useful for materials that are difficult to sinter using conventional methods, such as refractory metals and ceramics.
- SPS is also employed in the fabrication of functionally graded materials (FGMs) and nanostructured materials.
-
Applications of AM:
- AM is used across various industries, including aerospace, automotive, healthcare, and consumer goods, for prototyping, custom parts, and complex components.
- It is particularly valuable for producing lightweight structures, customized medical implants, and intricate designs that are not feasible with traditional manufacturing methods.
-
Conclusion:
- While SPS and AM both involve the transformation of powdered materials into solid parts, they are fundamentally different in their approaches and applications.
- SPS is not considered additive manufacturing because it does not involve the layer-by-layer addition of material. Instead, it is a sintering process that consolidates powder into a dense component under heat and pressure.
- Understanding the distinctions between these technologies is crucial for selecting the appropriate method for specific manufacturing needs.
In summary, SPS is a powerful sintering technique with unique advantages, but it does not fall under the umbrella of additive manufacturing. Its role in materials processing is complementary to AM, offering solutions for specific challenges in material densification and property enhancement.
Summary Table:
Aspect | Spark Plasma Sintering (SPS) | Additive Manufacturing (AM) |
---|---|---|
Process Mechanism | Consolidates powder in a single step | Builds parts layer by layer |
Material Addition | Pre-placed powder in a die | Material added incrementally |
Complexity of Parts | Simpler shapes | Complex, intricate geometries |
Material Waste | Some material loss during handling | Minimal waste (material added as needed) |
Applications | Advanced ceramics, composites, metals | Aerospace, automotive, healthcare, etc. |
Want to learn more about SPS and AM? Contact our experts today for tailored solutions!