Sputtering is indeed performed in a vacuum, and this is a critical aspect of the process. The vacuum environment ensures that the ejected atoms from the target material can travel freely towards the substrate without significant resistance or contamination. This is essential for achieving high-quality thin films with precise properties. The vacuum level must be carefully controlled to balance the need for a plasma to form and sustain, while also minimizing collisions that could degrade the deposition process. The specific vacuum level required can vary depending on the material being sputtered and the desired characteristics of the film.
Key Points Explained:
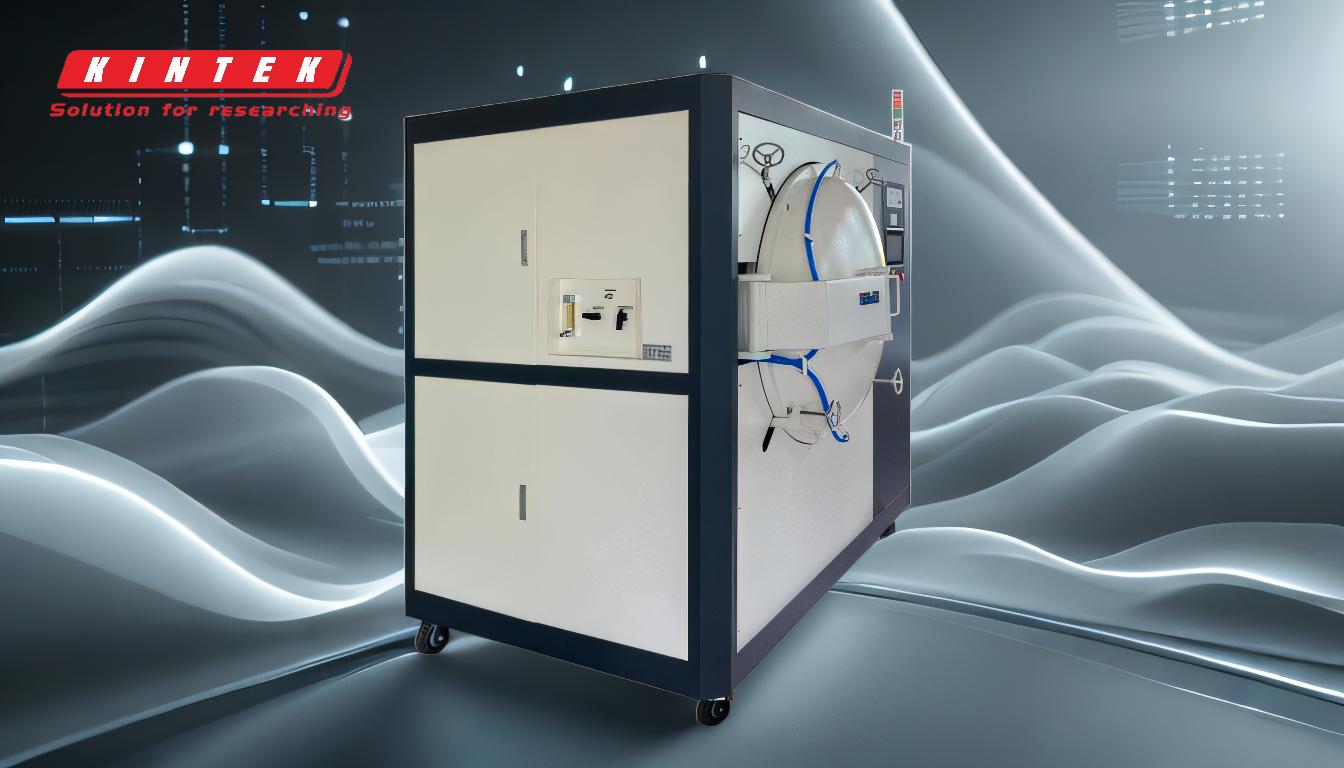
-
Vacuum Environment is Essential:
- A vacuum is necessary for sputtering to ensure that the ejected atoms from the target material can move freely towards the substrate. This minimizes resistance and prevents contamination from air or other gases, which could degrade the quality of the deposited film.
-
Balancing Vacuum Pressure:
- The vacuum level must be carefully controlled. If the pressure is too low, there won't be enough collisions to sustain a plasma, which is necessary for the sputtering process. Conversely, if the pressure is too high, excessive collisions can prevent electrons from gaining enough energy to ionize atoms, which is also crucial for sustaining the plasma.
-
Preventing Contamination:
- Maintaining the correct vacuum level is vital to prevent contamination of the thin film by air or other gases. This ensures that the deposited film has the desired properties and quality. The vacuum level must be sufficient to remove almost all vapors other than the source material before the process begins.
-
Impact on Deposition Efficiency:
- In a high vacuum, evaporated particles can travel directly to the deposition target without colliding with background gas. This results in a more controlled and efficient deposition process, which is critical for achieving uniform and high-quality thin films.
-
Dependence on Sample and Detail Level:
- The required vacuum level can vary depending on the specific sample and the level of detail needed in the deposited film. Different materials and applications may require different vacuum conditions to achieve optimal results.
In summary, sputtering is performed in a vacuum to ensure that the process is efficient, controlled, and free from contamination. The vacuum level must be carefully managed to sustain the plasma and achieve the desired film properties.
Summary Table:
Key Aspect | Explanation |
---|---|
Vacuum Environment | Ensures free movement of ejected atoms, minimizing resistance and contamination. |
Balancing Vacuum Pressure | Must sustain plasma formation while avoiding excessive collisions. |
Preventing Contamination | Removes air and gases to maintain film quality and desired properties. |
Deposition Efficiency | High vacuum allows direct particle travel, ensuring uniform and high-quality films. |
Sample-Specific Needs | Vacuum levels vary based on material and application requirements. |
Need expert advice on sputtering or vacuum systems? Contact us today for tailored solutions!