A continuous furnace is an industrial heat treatment system designed for high-volume production, where workpieces move through the heating chamber in a continuous flow. These furnaces utilize conveyor belts, roller systems, or other automated mechanisms to transport materials, ensuring an uninterrupted and efficient heat treatment process. They are ideal for applications requiring rapid thermal processing, such as drying, curing, or reheating semi-finished products for subsequent manufacturing steps. Continuous furnaces are widely used in industries where consistent, high-throughput processing of identical parts is essential.
Key Points Explained:
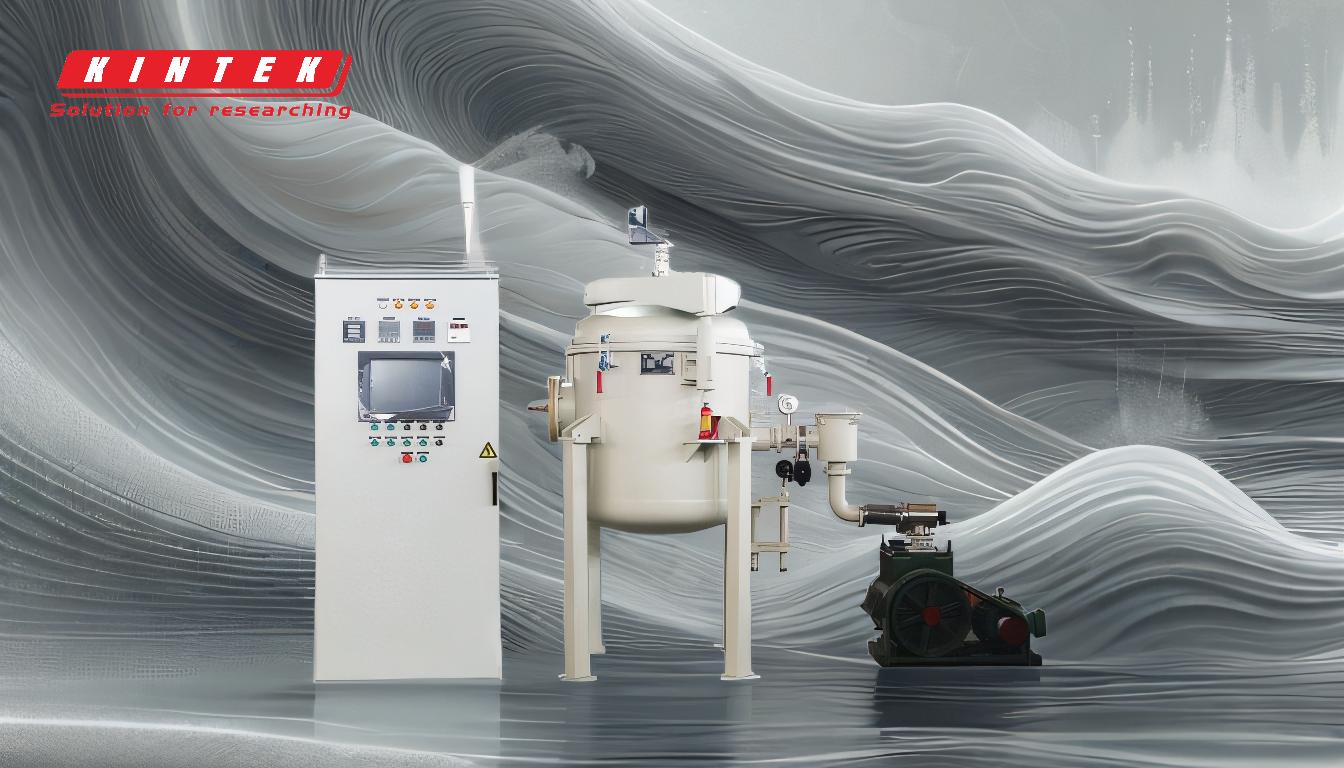
-
Definition and Purpose of Continuous Furnaces
- Continuous furnaces are industrial heat treatment systems designed to process a continuous flow of workpieces.
- They are optimized for high-volume production environments, ensuring consistent and uninterrupted heat treatment.
- These furnaces are ideal for applications requiring rapid thermal processing, such as drying, curing, or reheating semi-finished products.
-
Mechanism of Operation
- Workpieces are transported through the furnace using automated systems like conveyor belts, roller systems, "walking beams," or rotary screws.
- The movement of materials is either continuous or step-by-step, depending on the furnace design and application.
- This mechanism ensures that the heat treatment process is completed as the workpieces pass through the furnace, minimizing downtime and maximizing efficiency.
-
Applications of Continuous Furnaces
- Heat Treatment: Used for processes like annealing, hardening, or tempering of metal components.
- Drying and Curing: Suitable for fast drying and curing of coatings, adhesives, or other materials.
- Reheating Semi-Finished Products: Often used to reheat materials for subsequent hot forming or further manufacturing steps.
- High-Volume Production: Ideal for industries requiring the processing of thousands of identical parts in a consistent manner.
-
Advantages of Continuous Furnaces
- High Throughput: Enables the processing of large quantities of materials in a short time.
- Consistency: Provides uniform heat treatment for all workpieces, ensuring consistent quality.
- Automation: Reduces manual labor and human error, improving operational efficiency.
- Energy Efficiency: Optimized heating processes reduce energy consumption compared to batch furnaces.
-
Types of Continuous Furnaces
- Conveyor Belt Furnaces: Use a moving belt to transport materials through the heating chamber.
- Roller Hearth Furnaces: Utilize rollers to move heavy or large workpieces.
- Walking Beam Furnaces: Employ a mechanical system to lift and move materials in a step-by-step manner.
- Rotary Hearth Furnaces: Use a rotating platform to move materials through the furnace.
-
Design Considerations for Continuous Furnaces
- Temperature Control: Precise temperature regulation is critical to ensure consistent heat treatment.
- Material Handling: The system must accommodate the size, shape, and weight of the workpieces.
- Heating Chamber Design: The chamber must provide uniform heating and accommodate the movement of materials.
- Automation Integration: The furnace should integrate seamlessly with other manufacturing processes for optimal efficiency.
-
Industries Using Continuous Furnaces
- Automotive: For heat treatment of engine components, gears, and other parts.
- Aerospace: For processing high-strength alloys and composites.
- Electronics: For curing coatings on circuit boards or drying components.
- Metals and Mining: For reheating billets, slabs, or other semi-finished products.
-
Comparison with Batch Furnaces
- Continuous Furnaces: Suited for high-volume, consistent processing with minimal downtime.
- Batch Furnaces: Better for smaller batches or custom heat treatment processes.
- The choice between the two depends on production volume, material type, and specific heat treatment requirements.
By understanding these key points, purchasers of equipment and consumables can make informed decisions about whether a continuous furnace is the right solution for their manufacturing needs. Continuous furnaces offer significant advantages in terms of efficiency, consistency, and throughput, making them a valuable asset in high-volume production environments.
Summary Table:
Key Aspect | Details |
---|---|
Definition | Industrial heat treatment system for high-volume, continuous processing. |
Mechanism | Uses conveyor belts, rollers, or walking beams for material transport. |
Applications | Heat treatment, drying, curing, reheating semi-finished products. |
Advantages | High throughput, consistency, automation, and energy efficiency. |
Types | Conveyor belt, roller hearth, walking beam, rotary hearth furnaces. |
Industries | Automotive, aerospace, electronics, metals, and mining. |
Comparison | Better for high-volume vs. batch furnaces for smaller, custom processes. |
Ready to optimize your production with a continuous furnace? Contact us today for expert advice!