Hydrogen furnaces are specialized equipment used in various high-temperature processes across multiple industries. They utilize a hydrogen-rich atmosphere to facilitate specific chemical reactions or material property changes. These furnaces are primarily employed for sintering, annealing, brazing, metallization, and purification processes. They are particularly valuable in industries such as aerospace, automotive, electronics, and material science, where precise control over material properties is crucial. Hydrogen furnaces are also used for processing semiconductor materials, nano materials, and various metal powders, making them indispensable in advanced manufacturing and research applications.
Key Points Explained:
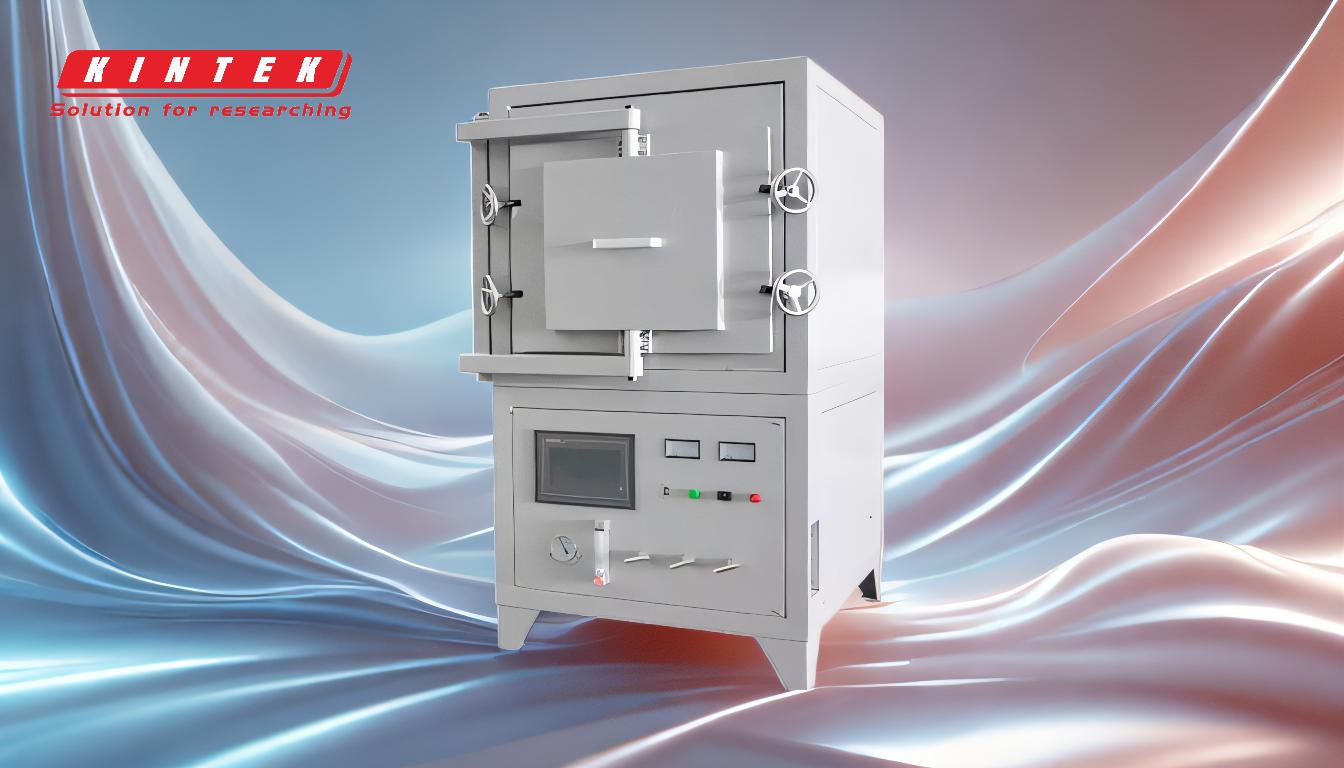
-
Ceramic Sintering and Metallization:
- Hydrogen furnaces are used to sinter ceramics, a process that involves heating ceramic powders to bond them into a solid structure without melting. This is crucial for creating strong, durable ceramic components.
- Metallization, which involves coating ceramics with a thin layer of metal, is also performed in hydrogen furnaces. This process is essential for creating components used in electronics and other industries where electrical conductivity is required.
-
Brazing:
- Brazing is a metal-joining process where a filler metal is melted and flowed into the joint between two or more metal pieces. Hydrogen furnaces provide the ideal environment for brazing, as the hydrogen atmosphere prevents oxidation and ensures a clean, strong joint.
-
Annealing and Purification:
- Annealing is a heat treatment process used to soften materials, improve ductility, and relieve internal stresses. Hydrogen furnaces are particularly effective for annealing glass parts used in sealing metal components, as the hydrogen atmosphere helps to purify the materials by removing impurities.
- Purification processes in hydrogen furnaces are essential for producing high-purity materials required in industries like semiconductor manufacturing and aerospace.
-
Sintering Powder Metallurgy:
- Powder metallurgy involves compacting metal powders into a desired shape and then sintering them to form a solid piece. Hydrogen furnaces are used to sinter these powders, ensuring the final product has the desired mechanical properties and density.
-
Semiconductor Alloy Processing:
- Hydrogen furnaces play a critical role in the processing of semiconductor alloys. The controlled hydrogen atmosphere allows for precise doping and alloying processes, which are essential for creating semiconductor materials with specific electrical properties.
-
High-Temperature Material Processing:
- Hydrogen furnaces are used for sintering, annealing, and welding of special high-temperature materials. These materials are often used in extreme environments, such as aerospace applications, where high strength and resistance to heat are required.
-
Hydrogen Reduction Processes:
- Hydrogen reduction furnaces are used to process materials like semiconductor wafers, nano materials, and various metal powders (e.g., copper, cobalt, nickel, tungsten, and molybdenum). The hydrogen atmosphere facilitates reduction reactions, which are essential for producing high-purity materials and alloys.
-
Applications in Advanced Industries:
- Hydrogen furnaces are widely used in advanced industries such as aerospace, automobile manufacturing, and electronics. In aerospace, they are used for creating high-strength, lightweight components. In the automotive industry, they are used for producing durable engine parts. In electronics, they are essential for creating semiconductor devices and other high-purity materials.
-
Controlled Atmosphere and Temperature:
- Hydrogen furnaces provide a controlled atmosphere and precise temperature control, which is crucial for achieving the desired material properties. The hydrogen atmosphere prevents oxidation and other unwanted chemical reactions, ensuring high-quality results.
-
Versatility in Material Processing:
- Hydrogen furnaces are versatile and can be used for a wide range of materials, including metals, ceramics, and semiconductors. This versatility makes them valuable tools in both industrial manufacturing and research laboratories.
In summary, hydrogen furnaces are essential for a wide range of high-temperature processes, particularly in industries where material purity, strength, and precise control over material properties are critical. Their ability to provide a controlled hydrogen atmosphere makes them indispensable for sintering, annealing, brazing, and other processes that require high precision and quality.
Summary Table:
Process | Description | Applications |
---|---|---|
Ceramic Sintering | Bonds ceramic powders into solid structures without melting. | Electronics, durable components |
Metallization | Coats ceramics with metal for electrical conductivity. | Electronics, industrial components |
Brazing | Joins metals using a filler metal in a hydrogen-rich atmosphere. | Aerospace, automotive, electronics |
Annealing | Softens materials, improves ductility, and relieves internal stresses. | Glass sealing, semiconductor manufacturing |
Purification | Removes impurities to produce high-purity materials. | Aerospace, semiconductor production |
Powder Metallurgy | Sinters metal powders to form solid pieces with desired properties. | Industrial manufacturing, research |
Semiconductor Alloying | Enables precise doping and alloying for specific electrical properties. | Semiconductor industry |
Hydrogen Reduction | Processes materials like semiconductor wafers and metal powders for purity. | Advanced manufacturing, research |
Ready to enhance your high-temperature processes with a hydrogen furnace? Contact our experts today to learn more!