Sintered products are widely used across various industries due to their unique properties and cost-effective manufacturing process. Sintering is a versatile technique that involves compacting and heating powdered materials to form solid objects without melting them entirely. This process is particularly useful for materials with high melting points, such as refractory metals, and for creating complex shapes with improved mechanical properties. Sintered products are commonly found in industries like aerospace, automotive, dental equipment, battery manufacturing, and research laboratories. The applications of sintering continue to grow, especially with advancements in 3D printing and additive manufacturing technologies.
Key Points Explained:
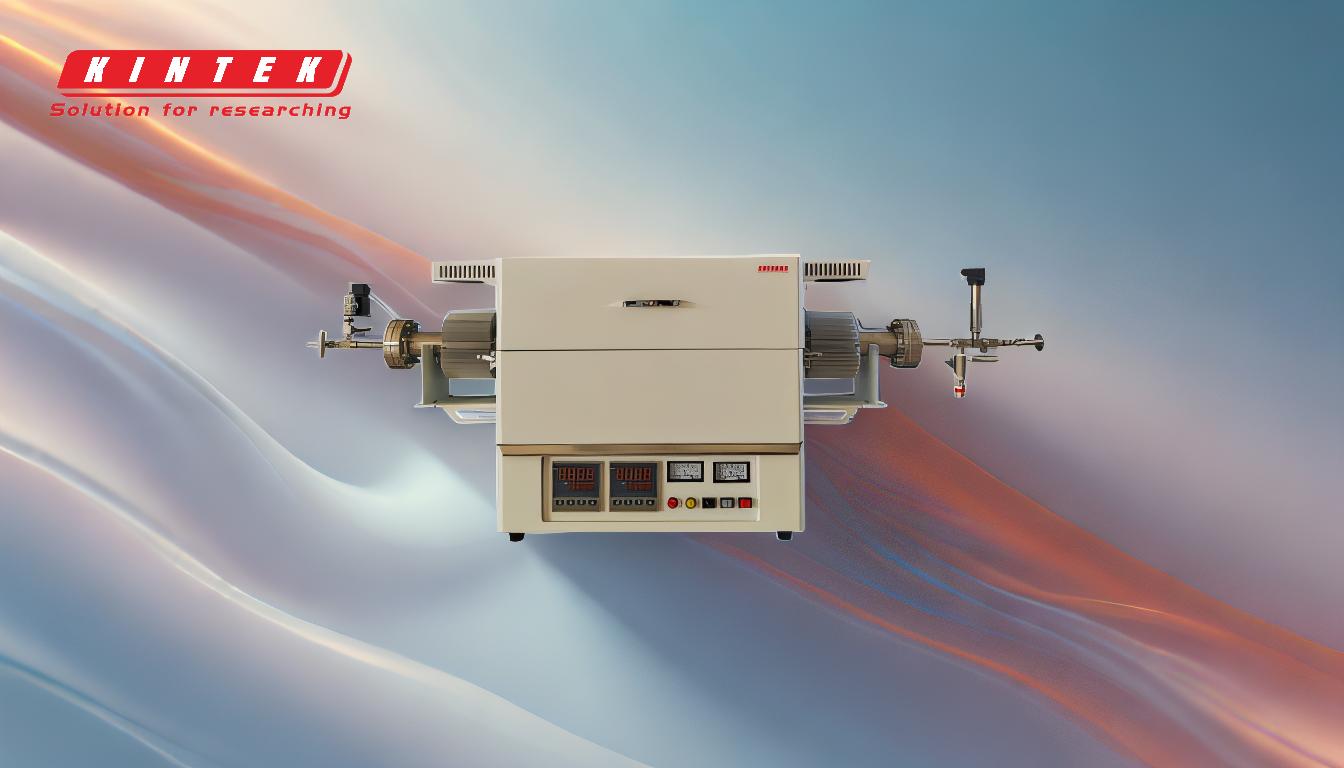
-
Powder Metallurgy:
- Sintering is a cornerstone of the powder metallurgy industry, where metal powders are compacted and heated to form durable, high-strength components.
- Common applications include gears, bearings, and structural parts used in automotive and aerospace industries.
- The process allows for the creation of complex shapes with minimal material waste, making it cost-effective and efficient.
-
Ceramic Industry:
- Sintering is extensively used in the special ceramic industry to produce components like insulators, cutting tools, and wear-resistant parts.
- Ceramic sintering enhances the material's density and mechanical properties, making it suitable for high-temperature and high-stress environments.
- Examples include ceramic filters, crucibles, and substrates for electronic components.
-
Additive Manufacturing and 3D Printing:
- Sintering plays a crucial role in additive manufacturing, particularly in 3D metal printing.
- It enables the layer-by-layer formation of custom metal shapes, offering design flexibility and energy savings compared to traditional melting processes.
- This technology is widely used in prototyping, medical implants, and aerospace components.
-
Refractory Metals:
- Sintering is essential for processing refractory metals like tungsten and molybdenum, which have extremely high melting points.
- These metals are used in applications requiring high thermal and electrical conductivity, such as filaments, electrodes, and furnace components.
-
Surface Porosity Reduction:
- Sintering can reduce the porosity of a material's surface, improving its mechanical properties, such as strength and wear resistance.
- This is particularly useful in creating filters, membranes, and other components where surface integrity is critical.
-
Diverse Industrial Applications:
- Sintered products are used in a wide range of industries, including:
- Aerospace: Lightweight and high-strength components.
- Dental Equipment: Durable and biocompatible materials for implants and tools.
- Battery Manufacturing: Electrodes and conductive components.
- Automotive: Engine parts, transmission components, and sensors.
- Research Laboratories: Custom components for experimental setups.
- Sintered products are used in a wide range of industries, including:
-
Energy Efficiency:
- Sintering is an energy-efficient process compared to melting, as it operates at lower temperatures.
- This makes it an environmentally friendly option for manufacturing, especially for materials with high melting points.
-
Emerging Technologies:
- Advances in sintering technologies, such as spark plasma sintering and microwave sintering, are expanding its applications.
- These innovations enable faster processing, improved material properties, and the ability to work with new materials.
In summary, sintered products are integral to modern manufacturing, offering solutions for creating durable, high-performance components across a wide range of industries. The versatility and efficiency of sintering make it a key process in both traditional and cutting-edge applications.
Summary Table:
Key Aspect | Description |
---|---|
Powder Metallurgy | Creates durable, high-strength components like gears and bearings. |
Ceramic Industry | Produces insulators, cutting tools, and wear-resistant parts. |
Additive Manufacturing | Enables 3D metal printing for prototyping and medical implants. |
Refractory Metals | Processes tungsten and molybdenum for high thermal/electrical conductivity. |
Surface Porosity Reduction | Improves strength and wear resistance in filters and membranes. |
Industrial Applications | Aerospace, automotive, dental equipment, battery manufacturing, and more. |
Energy Efficiency | Operates at lower temperatures, making it environmentally friendly. |
Emerging Technologies | Spark plasma and microwave sintering expand applications and material options. |
Learn how sintered products can revolutionize your manufacturing process—contact our experts today!