Heat treatment is a critical process in metallurgy and materials science, used to alter the physical and sometimes chemical properties of materials, primarily metals. The five main types of heat treatment are annealing, hardening, tempering, quenching, and stress relieving. Each method serves a specific purpose, such as improving hardness, ductility, or reducing internal stresses, and involves precise control of temperature and cooling rates to achieve the desired material properties.
Key Points Explained:
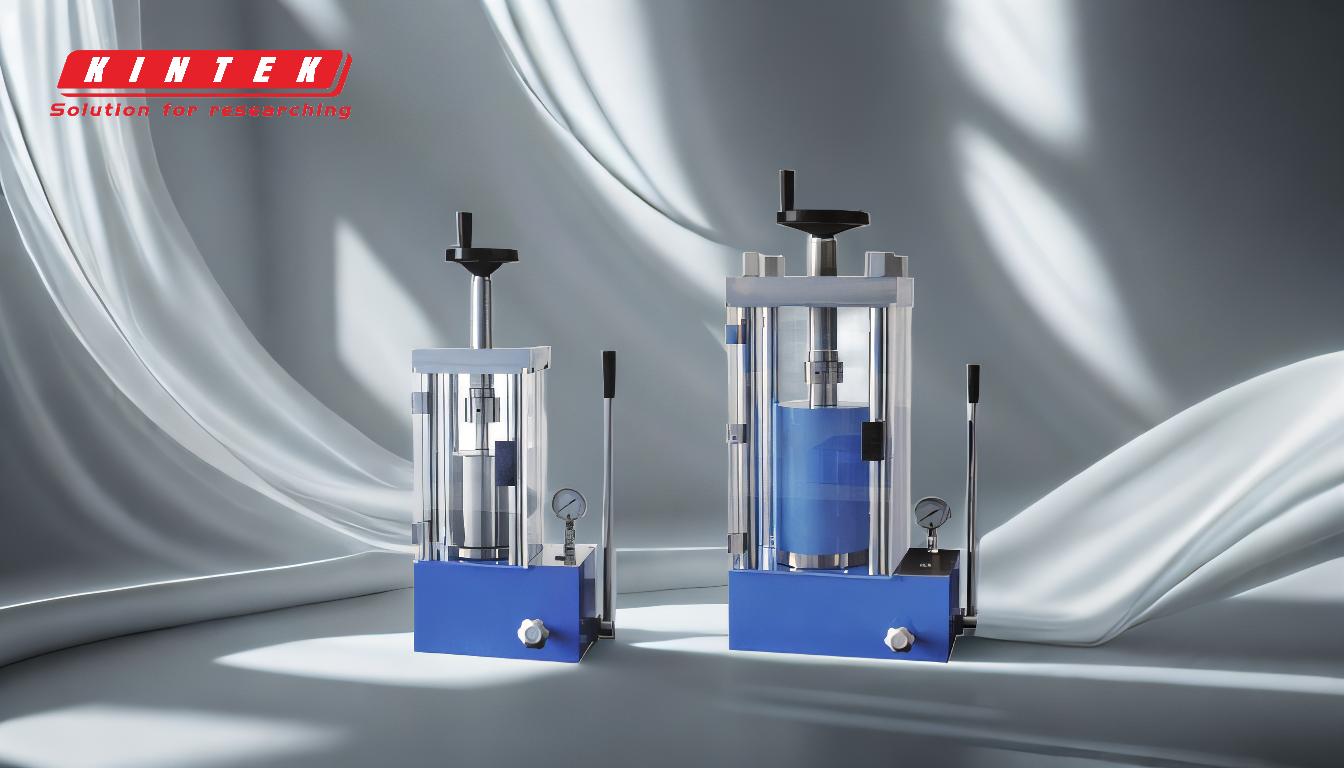
-
Annealing:
- Purpose: Annealing is used to soften materials, improve machinability, and enhance ductility. It also helps in reducing internal stresses and refining the grain structure.
- Process: The material is heated to a specific temperature (below its melting point) and then cooled slowly, usually in the furnace itself. This slow cooling allows the material to reach a more stable and softer state.
- Applications: Commonly used in steel, copper, and aluminum to prepare them for further processing like machining or cold working.
-
Hardening:
- Purpose: Hardening increases the hardness and strength of the material, making it more resistant to wear and deformation.
- Process: The material is heated to a high temperature (above its critical point) and then rapidly cooled, often by quenching in water, oil, or air. This rapid cooling traps carbon atoms in the crystal structure, creating a harder material.
- Applications: Used in tools, gears, and other components that require high strength and wear resistance.
-
Tempering:
- Purpose: Tempering is performed after hardening to reduce brittleness and improve toughness. It balances the hardness and ductility of the material.
- Process: The material is reheated to a temperature below its critical point and then cooled at a controlled rate. The temperature and duration of tempering determine the final properties of the material.
- Applications: Commonly applied to hardened steel to make it less brittle while retaining adequate hardness.
-
Quenching:
- Purpose: Quenching is a rapid cooling process used to lock the material's structure in a hardened state, preventing the formation of softer phases.
- Process: After heating the material to a high temperature, it is quickly immersed in a quenching medium like water, oil, or polymer. The rapid cooling rate is crucial for achieving the desired hardness.
- Applications: Essential in the production of high-strength components such as springs, blades, and automotive parts.
-
Stress Relieving:
- Purpose: Stress relieving is used to reduce internal stresses that can occur during manufacturing processes like welding, machining, or casting. It helps in preventing distortion and improving dimensional stability.
- Process: The material is heated to a temperature below its critical point and then cooled slowly. This process does not significantly alter the material's hardness or strength but helps in stabilizing its structure.
- Applications: Often used in welded structures, castings, and machined parts to ensure they maintain their shape and performance over time.
Each of these heat treatment methods plays a crucial role in tailoring the properties of materials to meet specific engineering requirements. By understanding and applying these processes correctly, manufacturers can produce components with optimized performance characteristics for various applications.
Summary Table:
Heat Treatment | Purpose | Process | Applications |
---|---|---|---|
Annealing | Soften materials, improve machinability, reduce stress | Heated below melting point, cooled slowly | Steel, copper, aluminum for machining or cold work |
Hardening | Increase hardness and strength | Heated above critical point, rapidly cooled (quenching) | Tools, gears, wear-resistant components |
Tempering | Reduce brittleness, improve toughness | Reheated below critical point, cooled at controlled rate | Hardened steel for balanced hardness and ductility |
Quenching | Lock material in hardened state | Heated to high temperature, rapidly cooled in water, oil, or polymer | Springs, blades, automotive parts |
Stress Relieving | Reduce internal stresses, prevent distortion | Heated below critical point, cooled slowly | Welded structures, castings, machined parts |
Optimize your material properties with the right heat treatment—contact our experts today for tailored solutions!