Muffle furnaces are essential equipment in high-temperature applications, particularly in metal processing and material testing. Acceptance criteria for a muffle furnace ensure it meets operational, safety, and performance standards. These criteria include environmental conditions, design specifications, and functional requirements. The furnace must operate in a safe environment, free from flammable, explosive, or corrosive substances, and maintain specific temperature and humidity conditions. Key design considerations include chamber size, heating elements, power supply, and energy efficiency. Proper placement and installation are also critical to ensure longevity and optimal performance.
Key Points Explained:
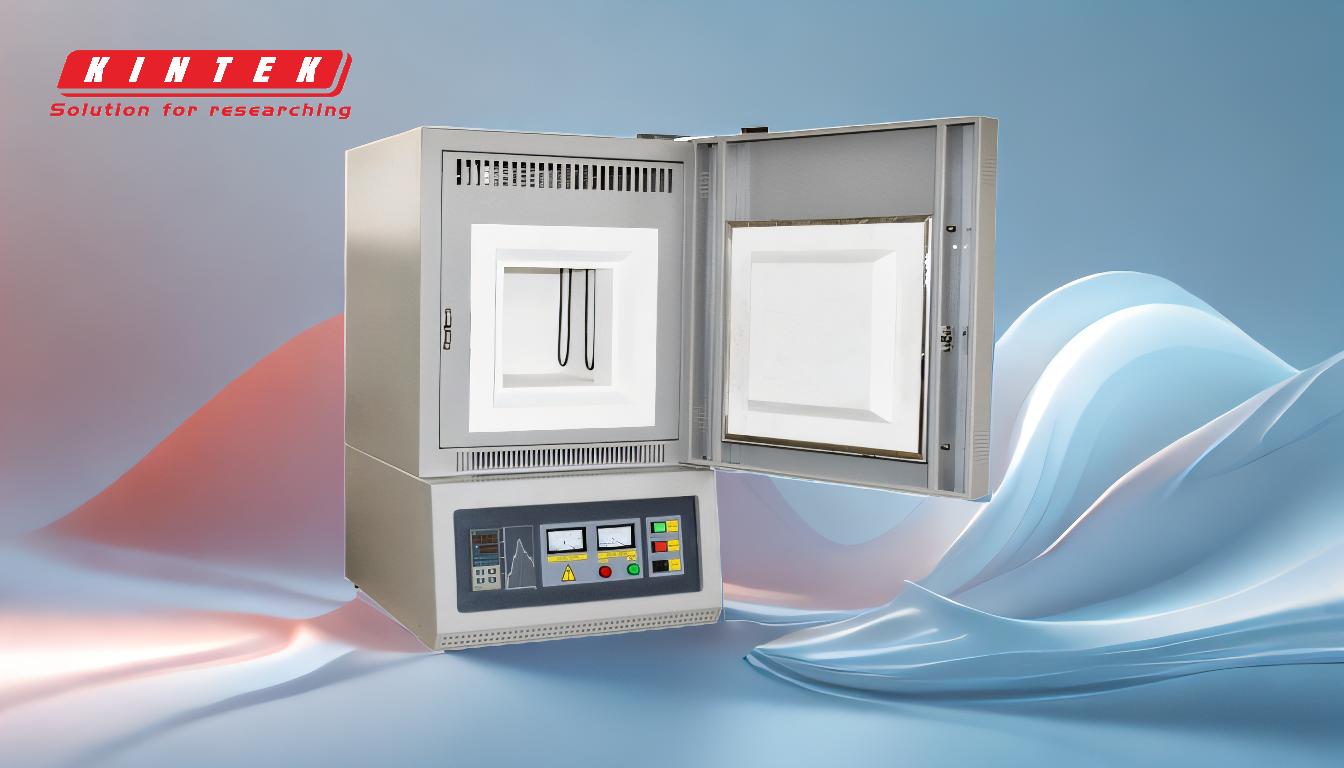
-
Environmental Conditions:
- Humidity: The relative humidity of the operating environment should not exceed 85%. High humidity can damage the furnace's internal components, particularly the heating elements, and reduce its efficiency.
- Temperature: The ambient temperature should be between 1°C and 40°C. Operating outside this range can affect the furnace's performance and lifespan.
- Safety: The environment must be free of flammable, explosive, or corrosive materials. This ensures safe operation and prevents damage to the furnace and surrounding equipment.
-
Design Specifications:
- Chamber Size: The size of the interior chamber should accommodate the materials being processed. Larger chambers are suitable for bulk processing, while smaller chambers are ideal for precise, small-scale applications.
- Heating Elements: The type and quality of heating elements are critical for achieving and maintaining the desired temperatures. High-quality elements ensure uniform heating and longevity.
- Power Supply: The furnace must be compatible with the available power supply. This includes voltage and current requirements to ensure efficient operation.
- Energy Efficiency: Selecting an energy-efficient furnace helps reduce operational costs and environmental impact. Look for models with advanced insulation and temperature control features.
-
Functional Requirements:
- Maximum Temperature: The furnace should be capable of reaching the required maximum temperature for the intended application. This is particularly important for processes involving high-temperature materials like stainless steel and copper.
- Temperature Control: Precise temperature control is essential for consistent results. Advanced software and control systems can enhance accuracy and repeatability.
- Door Opening Options: The design of the door and its opening mechanism should facilitate easy loading and unloading of materials. This is especially important for frequent use or large-scale operations.
-
Installation and Placement:
- Location: The furnace should be placed on a solid, stable surface such as a concrete table or shelf. This prevents vibrations and ensures stability during operation.
- Proximity to Controller: The controller should be placed away from the furnace to avoid overheating. Proper placement also helps in maintaining accurate temperature readings and control.
- Ventilation: Adequate ventilation around the furnace is necessary to dissipate heat and prevent overheating of internal components.
By adhering to these acceptance criteria, you can ensure that the muffle furnace operates safely, efficiently, and effectively, meeting the demands of your specific application.
Summary Table:
Criteria | Details |
---|---|
Environmental Conditions | - Humidity: ≤ 85% - Ambient Temperature: 1°C to 40°C - Safe from flammable/explosive materials |
Design Specifications | - Chamber Size: Fits materials - Heating Elements: High-quality - Power Supply: Compatible - Energy Efficiency: Advanced insulation |
Functional Requirements | - Max Temperature: Application-specific - Temperature Control: Precise - Door Opening: Easy loading/unloading |
Installation & Placement | - Location: Stable surface - Controller Placement: Away from furnace - Ventilation: Adequate heat dissipation |
Ensure your muffle furnace meets the highest standards—contact our experts today for personalized guidance!