Annealing is a heat treatment process that involves heating metals to a specific temperature, holding them at that temperature, and then cooling them slowly. This process offers several advantages, such as improving ductility, reducing hardness, relieving internal stresses, and enhancing machinability and electrical properties. However, it also has disadvantages, including low productivity, long cooling times, uneven heating, and sensitivity to temperature variations, which can affect material quality and equipment performance. The process requires careful handling post-treatment, as materials become highly sensitive to shock and stress.
Key Points Explained:
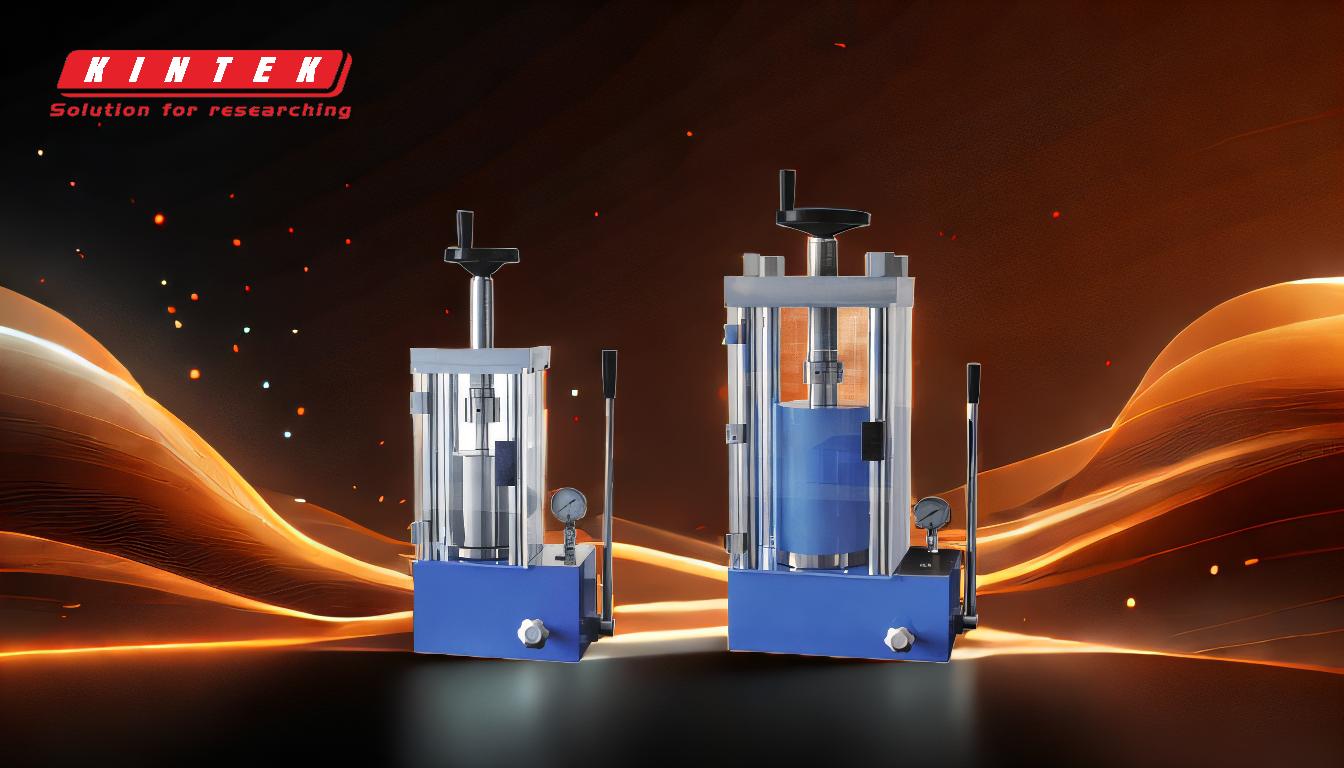
-
Advantages of Annealing:
- Improved Ductility and Workability: Annealing makes metals more ductile, allowing them to be shaped without cracking. This is particularly useful in manufacturing processes where metals need to be bent, stretched, or formed into complex shapes.
- Reduction in Hardness: By reducing hardness, annealing makes metals easier to machine, cut, or drill, which is beneficial in industries requiring precise metalworking.
- Stress Relief: Internal stresses caused by previous manufacturing processes, such as welding or cold working, are relieved during annealing. This prevents material deformation or failure during use.
- Enhanced Electrical Properties: Annealing refines the crystal structure of metals, improving their electrical conductivity. This is crucial for materials used in electrical applications, such as wiring or transformers.
- Improved Mechanical Properties: The process enhances mechanical properties like toughness and strength, making materials more durable and resistant to wear and tear.
-
Disadvantages of Annealing:
- Low Productivity: Traditional annealing methods, such as vacuum annealing, often have low productivity due to long heating and cooling cycles.
- Uneven Heating: Materials, especially large or complex shapes, may experience uneven heating, leading to inconsistent material properties and quality issues.
- Temperature Sensitivity: Variations in temperature during the annealing process (ranging from 5 to 25°C) can affect the stability and consistency of the final product.
- Equipment Degradation: Frequent cycling between vacuum and normal pressure environments can cause wear and tear on equipment, reducing its lifespan.
- Post-Treatment Sensitivity: Annealed materials are highly sensitive to shock, vibration, and stress, requiring careful handling to avoid damage.
-
Applications and Considerations:
- Material-Specific Effects: For example, in X80 pipeline steel, annealing at 200°C for 12 hours increases yield strength by 10% but reduces elongation by 20%. This is due to the formation of a Cottrell atmosphere, which pins dislocations and reduces movable dislocation density.
- Use of Inert Atmospheres: Nitrogen gas mixtures are often used during annealing to prevent oxidation and unwanted chemical reactions, ensuring the material retains its desired properties.
- Cooling Process: Slow cooling is essential to achieve the desired crystalline structure and avoid reintroducing stresses or defects.
-
Challenges in Industrial Implementation:
- Inconsistent Quality: Traditional methods may result in poor inherent quality consistency, making it difficult to produce uniform batches of materials.
- Thermal Stress and Layer Issues: Problems like thermal stress, layer channeling, and loose layers can arise, particularly in materials like aluminum foil rolls, affecting their usability and performance.
In summary, annealing is a valuable process for improving material properties, but it comes with challenges that require careful management of temperature, equipment, and post-treatment handling to achieve consistent and high-quality results.
Summary Table:
Aspect | Advantages | Disadvantages |
---|---|---|
Ductility | Improves ductility, making metals easier to shape without cracking. | N/A |
Hardness | Reduces hardness, enhancing machinability and cutting precision. | N/A |
Stress Relief | Relieves internal stresses, preventing deformation or failure. | N/A |
Electrical Properties | Enhances electrical conductivity, ideal for wiring and transformers. | N/A |
Mechanical Properties | Improves toughness, strength, and wear resistance. | N/A |
Productivity | N/A | Low productivity due to long heating and cooling cycles. |
Heating Uniformity | N/A | Uneven heating can lead to inconsistent material properties. |
Temperature Sensitivity | N/A | Sensitive to temperature variations (5-25°C), affecting stability. |
Equipment Lifespan | N/A | Frequent cycling causes wear and tear, reducing equipment lifespan. |
Post-Treatment Handling | N/A | Materials become highly sensitive to shock and stress, requiring careful handling. |
Need expert advice on annealing processes? Contact us today to optimize your metal heat treatment!