Thermal cracking is a process used in the petroleum industry to break down large hydrocarbon molecules into smaller, more useful ones. It involves heating heavy oil fractions to high temperatures, causing the chemical bonds to break. This process has several advantages, such as increasing the yield of valuable products like gasoline and diesel, and enabling the use of heavier crude oils. However, it also has disadvantages, including high energy consumption, the production of undesirable by-products, and the potential for equipment corrosion and coking. Understanding these pros and cons is essential for optimizing the process and making informed decisions in refinery operations.
Key Points Explained:
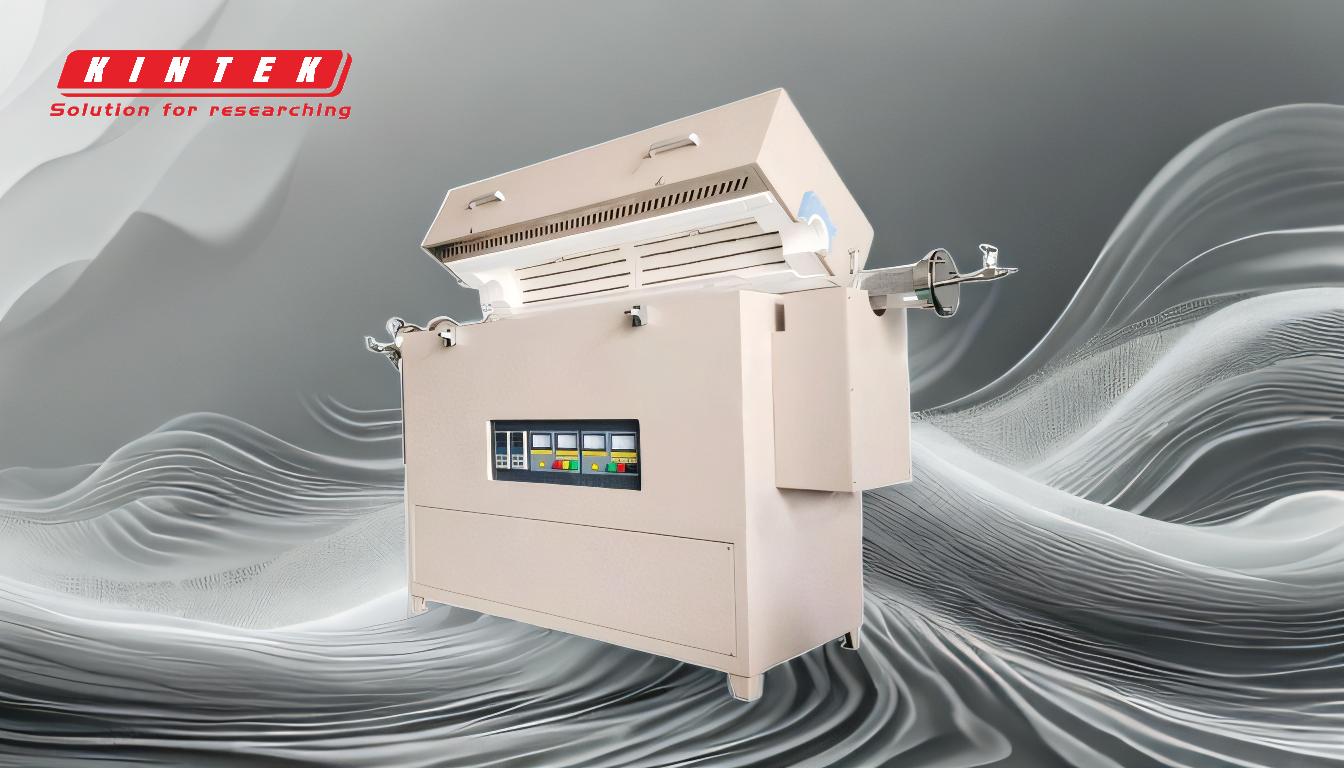
-
Advantages of Thermal Cracking:
- Increased Yield of Valuable Products: Thermal cracking significantly increases the yield of lighter, more valuable products such as gasoline, diesel, and light olefins. This is particularly beneficial in meeting the high demand for these fuels.
- Utilization of Heavier Crude Oils: The process allows refineries to process heavier crude oils, which are often cheaper and more abundant than lighter crudes. This flexibility can lead to cost savings and improved resource utilization.
- Simplicity of the Process: Thermal cracking is relatively simple compared to other cracking methods like catalytic cracking. It does not require complex catalysts or extensive equipment, making it easier to implement and maintain.
- Production of Petrochemical Feedstocks: The process generates olefins and other petrochemical feedstocks, which are essential for producing plastics, synthetic rubber, and other chemicals.
-
Disadvantages of Thermal Cracking:
- High Energy Consumption: Thermal cracking requires significant amounts of energy to achieve the high temperatures needed for the reaction. This can lead to increased operational costs and a larger carbon footprint.
- Production of Undesirable By-products: The process can produce unwanted by-products such as coke, tar, and heavy residues. These by-products can be difficult to handle and may require additional processing or disposal.
- Equipment Corrosion and Coking: The high temperatures and reactive intermediates involved in thermal cracking can lead to equipment corrosion and the formation of coke deposits. This can reduce the efficiency of the process and increase maintenance costs.
- Limited Control Over Product Distribution: Unlike catalytic cracking, thermal cracking offers limited control over the distribution of products. This can result in a less optimal mix of products, reducing the overall efficiency of the refinery.
-
Comparison with Other Cracking Methods:
- Catalytic Cracking: Catalytic cracking generally offers better control over product distribution and produces fewer undesirable by-products. However, it requires more complex equipment and catalysts, making it more expensive to operate.
- Hydrocracking: Hydrocracking combines cracking with hydrogenation, producing higher-quality products with fewer impurities. However, it also requires significant hydrogen input and more complex infrastructure.
- Steam Cracking: Steam cracking is primarily used for producing olefins and is highly efficient for this purpose. However, it is less versatile than thermal cracking and is not suitable for producing a wide range of products.
-
Economic and Environmental Considerations:
- Economic Viability: The economic viability of thermal cracking depends on the price of crude oil and the demand for various petroleum products. When heavy crude oils are inexpensive, thermal cracking can be a cost-effective option.
- Environmental Impact: The high energy consumption and production of by-products make thermal cracking less environmentally friendly compared to other methods. Refineries must consider the environmental regulations and potential carbon taxes when choosing this process.
-
Future Prospects and Improvements:
- Technological Advancements: Ongoing research and development aim to improve the efficiency of thermal cracking and reduce its environmental impact. Innovations such as advanced heat recovery systems and better materials for equipment can help mitigate some of the disadvantages.
- Integration with Other Processes: Integrating thermal cracking with other refining processes, such as hydrocracking or catalytic cracking, can optimize the overall efficiency and product yield of the refinery.
In conclusion, thermal cracking offers several advantages, including increased yield of valuable products and the ability to process heavier crude oils. However, it also has significant disadvantages, such as high energy consumption, the production of undesirable by-products, and equipment issues. Understanding these pros and cons is crucial for making informed decisions in refinery operations and optimizing the process for better economic and environmental outcomes.
Summary Table:
Aspect | Advantages | Disadvantages |
---|---|---|
Yield of Products | Increases yield of gasoline, diesel, and light olefins. | Limited control over product distribution. |
Crude Oil Utilization | Allows processing of cheaper, heavier crude oils. | High energy consumption and carbon footprint. |
Process Simplicity | Simpler than catalytic cracking; no complex catalysts required. | Equipment corrosion and coking issues. |
By-products | Generates petrochemical feedstocks for plastics and synthetic rubber. | Produces undesirable by-products like coke and tar. |
Economic Viability | Cost-effective when heavy crude oils are inexpensive. | Environmental impact and potential carbon taxes. |
Optimize your refinery operations with thermal cracking—contact our experts today for tailored solutions!