Electrochemical deposition (ECD) offers several advantages, making it a widely used technique in various industries. It enables precise control over the thickness and uniformity of deposited layers, making it ideal for applications requiring high-quality coatings, such as in electronics and corrosion protection. ECD is cost-effective, scalable, and compatible with a wide range of materials, including metals, alloys, and composites. Additionally, it allows for the deposition of complex shapes and intricate designs, making it suitable for microfabrication and nanotechnology. The process is environmentally friendly compared to other deposition methods, as it often uses aqueous solutions and generates minimal waste. Overall, ECD is a versatile, efficient, and sustainable method for material deposition.
Key Points Explained:
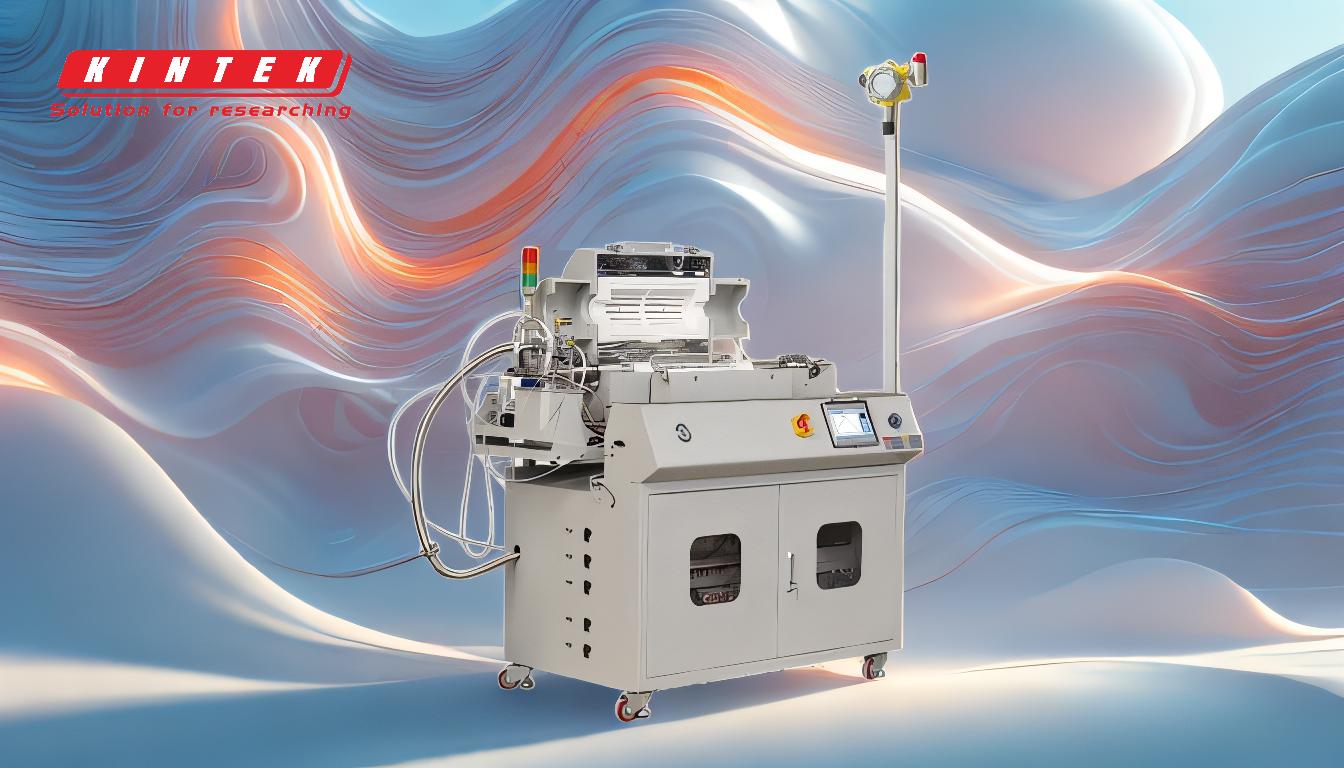
-
Precise Control Over Deposition
- Electrochemical deposition allows for precise control over the thickness and uniformity of the deposited layer. This is particularly important in industries like electronics, where thin, uniform coatings are essential for optimal performance.
- The process parameters, such as current density, voltage, and electrolyte composition, can be fine-tuned to achieve the desired deposition characteristics.
-
Cost-Effectiveness and Scalability
- ECD is a cost-effective method compared to other deposition techniques like physical vapor deposition (PVD) or chemical vapor deposition (CVD). It requires relatively simple equipment and can be easily scaled up for mass production.
- The ability to deposit materials at room temperature further reduces energy costs, making it an economical choice for large-scale manufacturing.
-
Compatibility with Diverse Materials
- ECD is compatible with a wide range of materials, including metals (e.g., copper, nickel, gold), alloys, and even composites. This versatility makes it suitable for various applications, from decorative coatings to functional layers in electronic devices.
- The process can also be adapted to deposit nanomaterials, enabling advancements in nanotechnology and microfabrication.
-
Ability to Deposit Complex Shapes
- One of the standout advantages of ECD is its ability to deposit materials onto complex shapes and intricate designs. This is particularly useful in microfabrication, where components often have intricate geometries.
- The process can uniformly coat surfaces with varying topographies, ensuring consistent quality across the entire substrate.
-
Environmental Friendliness
- ECD is considered more environmentally friendly than many other deposition methods. It typically uses aqueous solutions, which are less harmful than the solvents used in some chemical processes.
- The process generates minimal waste, and many of the byproducts can be recycled or safely disposed of, reducing the environmental impact.
-
Applications in Electronics and Corrosion Protection
- In the electronics industry, ECD is used to deposit conductive layers, such as copper interconnects in printed circuit boards (PCBs). The precision and uniformity of the deposition are critical for the performance of these components.
- ECD is also widely used for corrosion protection, where it deposits protective coatings (e.g., zinc or nickel) onto metal surfaces, extending their lifespan and reducing maintenance costs.
-
Advancements in Nanotechnology
- ECD has enabled significant advancements in nanotechnology, allowing for the deposition of nanoscale materials with controlled properties. This has opened up new possibilities in fields like sensors, energy storage, and biomedical devices.
- The ability to deposit materials at the nanoscale with high precision makes ECD a key technology in the development of next-generation devices.
-
Minimal Thermal Stress
- Unlike some deposition methods that require high temperatures, ECD is typically performed at or near room temperature. This minimizes thermal stress on the substrate, making it suitable for temperature-sensitive materials.
- The absence of high temperatures also reduces the risk of material degradation, ensuring the integrity of the deposited layer.
In summary, electrochemical deposition is a versatile, efficient, and sustainable method that offers numerous advantages, including precise control, cost-effectiveness, compatibility with diverse materials, and environmental friendliness. Its applications span a wide range of industries, from electronics to corrosion protection, and it continues to play a crucial role in advancing nanotechnology and microfabrication.
Summary Table:
Advantage | Key Details |
---|---|
Precise Control | Fine-tuned thickness and uniformity for high-quality coatings. |
Cost-Effectiveness | Scalable, low-energy process ideal for mass production. |
Material Compatibility | Works with metals, alloys, composites, and nanomaterials. |
Complex Shape Deposition | Uniform coating on intricate designs and varying topographies. |
Environmental Friendliness | Uses aqueous solutions, generates minimal waste, and supports recycling. |
Electronics & Corrosion | Essential for conductive layers and protective coatings. |
Nanotechnology Applications | Enables nanoscale material deposition for advanced devices. |
Minimal Thermal Stress | Performed at room temperature, preserving substrate integrity. |
Unlock the potential of electrochemical deposition for your projects—contact our experts today!