Inert gas condensation (IGC) is a widely used technique in materials science for producing ultrafine particles and nanomaterials. It involves evaporating a material in a vacuum or inert gas environment, followed by condensation of the vapor into nanoparticles. The advantages of IGC include high purity of the produced materials, control over particle size and morphology, scalability, and the ability to synthesize a wide range of materials, including metals, alloys, and ceramics. These benefits make IGC a versatile and efficient method for nanomaterial synthesis, particularly in applications requiring precise control over material properties.
Key Points Explained:
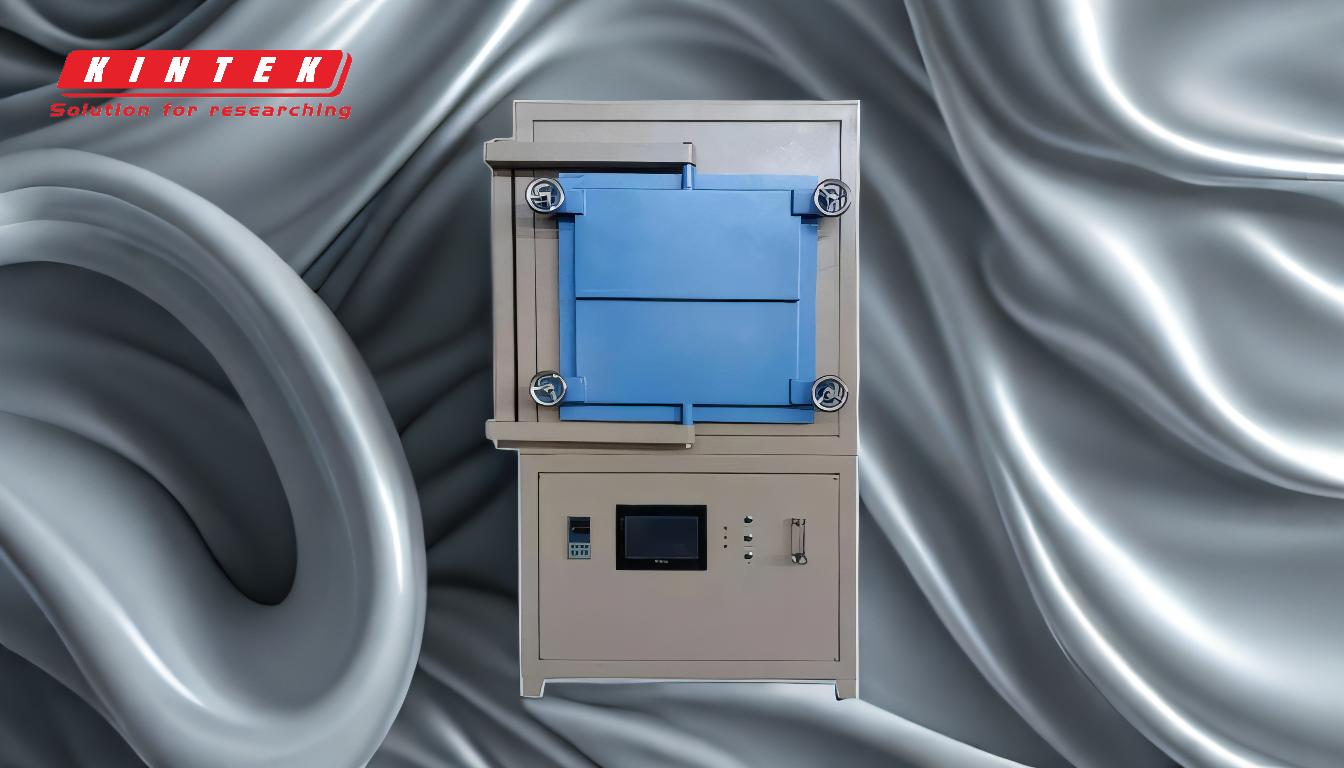
-
High Purity of Produced Materials:
- Inert gas condensation takes place in a controlled environment, typically under vacuum or in an inert gas like argon or helium. This prevents contamination from reactive gases such as oxygen or nitrogen, ensuring high purity of the synthesized nanoparticles.
- The absence of impurities is critical for applications in electronics, catalysis, and biomedical fields, where even trace contaminants can significantly affect performance.
-
Control Over Particle Size and Morphology:
- IGC allows precise control over the size and shape of nanoparticles by adjusting parameters such as evaporation rate, gas pressure, and temperature.
- Smaller particles can be produced by increasing the cooling rate or reducing the gas pressure, while larger particles can be obtained by decreasing the cooling rate or increasing the gas pressure.
- This level of control is essential for tailoring materials for specific applications, such as optimizing catalytic activity or tuning optical properties.
-
Scalability:
- The IGC process can be scaled up to produce large quantities of nanoparticles, making it suitable for industrial applications.
- Continuous flow systems and advanced reactor designs have further enhanced the scalability of IGC, enabling cost-effective production of nanomaterials on a commercial scale.
-
Versatility in Material Synthesis:
- IGC can be used to synthesize a wide range of materials, including pure metals, alloys, and ceramics.
- By co-evaporating multiple materials, complex nanostructures such as core-shell particles or nanocomposites can be produced.
- This versatility makes IGC a valuable tool for research and development in fields like energy storage, sensors, and advanced coatings.
-
Environmentally Friendly Process:
- IGC is a relatively clean process that does not involve harmful chemicals or solvents, reducing the environmental impact compared to other nanoparticle synthesis methods.
- The use of inert gases also minimizes waste generation, making IGC a more sustainable option for nanomaterial production.
-
Enhanced Material Properties:
- Nanoparticles produced by IGC often exhibit unique properties, such as high surface area, enhanced reactivity, and improved mechanical strength.
- These properties are advantageous for applications in catalysis, drug delivery, and advanced materials engineering.
-
Compatibility with Post-Processing Techniques:
- Nanoparticles synthesized via IGC can be easily integrated with other processing techniques, such as sintering, coating, or functionalization, to create advanced materials with tailored properties.
- This compatibility enhances the utility of IGC in developing next-generation materials for various industries.
In summary, inert gas condensation offers numerous advantages, including high material purity, precise control over particle characteristics, scalability, and versatility. These benefits make it a preferred method for producing high-quality nanomaterials for a wide range of scientific and industrial applications.
Summary Table:
Advantage | Description |
---|---|
High Purity | Produces contamination-free nanoparticles in a controlled inert gas environment. |
Particle Size & Morphology | Precise control over size and shape for tailored applications. |
Scalability | Suitable for industrial-scale production of nanomaterials. |
Versatility | Synthesizes metals, alloys, ceramics, and complex nanostructures. |
Environmentally Friendly | Clean process with minimal waste and no harmful chemicals. |
Enhanced Material Properties | High surface area, reactivity, and mechanical strength for advanced uses. |
Post-Processing Compatibility | Easily integrates with sintering, coating, and functionalization techniques. |
Learn how inert gas condensation can revolutionize your nanomaterial production—contact our experts today!