Press forging is a highly efficient metalworking process that offers numerous advantages, particularly in terms of material properties, cost-effectiveness, and production capabilities. By applying compressive forces to heated metal, press forging enables the creation of strong, durable components with superior mechanical properties. This method is widely used in industries requiring high-performance parts, such as automotive, aerospace, and heavy machinery. Below, we explore the key benefits of press forging in detail.
Key Points Explained:
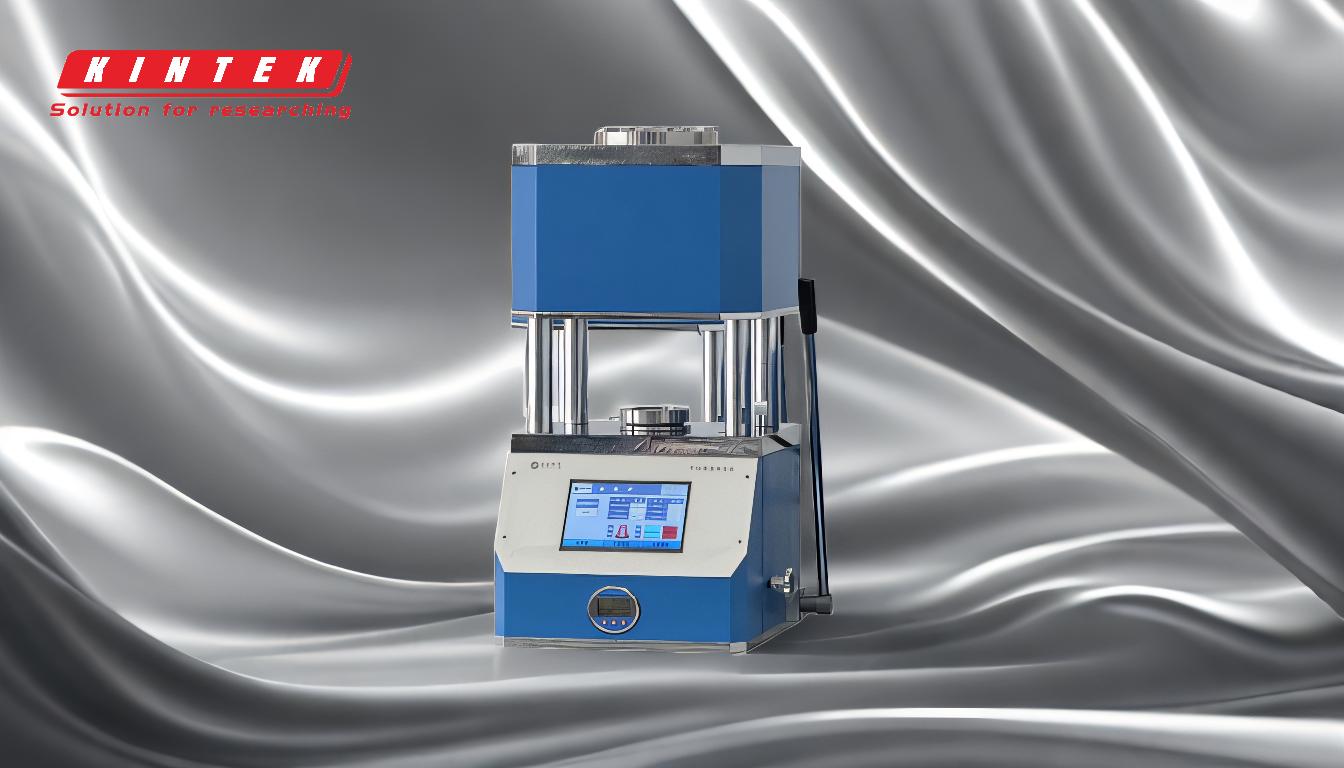
-
Enhanced Material Properties:
- Press forging significantly improves the mechanical properties of metals, including strength, toughness, and fatigue resistance. The process aligns the grain structure of the metal, resulting in a more uniform and dense material. This alignment enhances the overall durability and performance of the forged parts, making them ideal for high-stress applications.
-
Superior Dimensional Accuracy:
- Unlike other forging methods, press forging allows for precise control over the shape and dimensions of the final product. The slow and continuous application of pressure ensures that the metal fills the die cavity completely, resulting in parts with tight tolerances and minimal need for secondary machining.
-
Cost-Effectiveness:
- Press forging is a cost-effective manufacturing method, especially for large production runs. The ability to produce near-net-shape components reduces material waste and minimizes the need for additional machining, leading to lower overall production costs. Additionally, the use of forging alloys, which are readily available and affordable, further contributes to cost savings.
-
Versatility in Material Selection:
- Press forging is compatible with a wide range of materials, including carbon steels, alloy steels, and non-ferrous metals. This versatility allows manufacturers to select the most appropriate material for their specific application, ensuring optimal performance and longevity of the forged parts.
-
Improved Surface Finish:
- The controlled pressure and temperature conditions in press forging result in a smoother surface finish compared to other forging techniques. This reduces the need for extensive post-forging surface treatments, saving both time and money in the production process.
-
Ability to Produce Complex Geometries:
- Press forging excels in creating intricate and complex shapes that would be difficult or impossible to achieve with other methods. The combination of heat and pressure allows the metal to flow into detailed die cavities, enabling the production of components with sophisticated geometries.
-
Reduced Material Waste:
- The precision of press forging minimizes material waste, as the process efficiently utilizes the metal to form the desired shape. This not only lowers material costs but also contributes to more sustainable manufacturing practices.
-
Enhanced Structural Integrity:
- The uniform grain flow achieved through press forging results in parts with superior structural integrity. This makes the forged components highly resistant to cracking, fatigue, and other forms of mechanical failure, ensuring long-term reliability in demanding applications.
In summary, press forging offers a multitude of advantages, including improved material properties, cost savings, and the ability to produce complex and precise components. These benefits make it a preferred choice for industries requiring high-performance and durable metal parts.
Summary Table:
Advantage | Description |
---|---|
Enhanced Material Properties | Improves strength, toughness, and fatigue resistance through uniform grain flow. |
Superior Dimensional Accuracy | Ensures tight tolerances and minimal secondary machining. |
Cost-Effectiveness | Reduces material waste and lowers production costs for large runs. |
Versatility in Material Selection | Compatible with carbon steels, alloy steels, and non-ferrous metals. |
Improved Surface Finish | Produces smoother surfaces, reducing post-forging treatments. |
Complex Geometries | Enables intricate shapes with detailed die cavities. |
Reduced Material Waste | Minimizes waste, contributing to sustainable manufacturing. |
Enhanced Structural Integrity | Ensures long-term reliability in high-stress applications. |
Ready to enhance your production with press forging? Contact us today to learn more!