Sintered components offer numerous advantages, making them a preferred choice in various industries. These benefits include cost-effectiveness, material versatility, high production efficiency, and the ability to create complex shapes with excellent mechanical properties. Additionally, sintering enhances material properties such as strength, thermal and electrical conductivity, and reduces porosity, leading to durable and high-performance parts. The process is also environmentally friendly, as it minimizes material waste and energy consumption. Below, we explore these advantages in detail.
Key Points Explained:
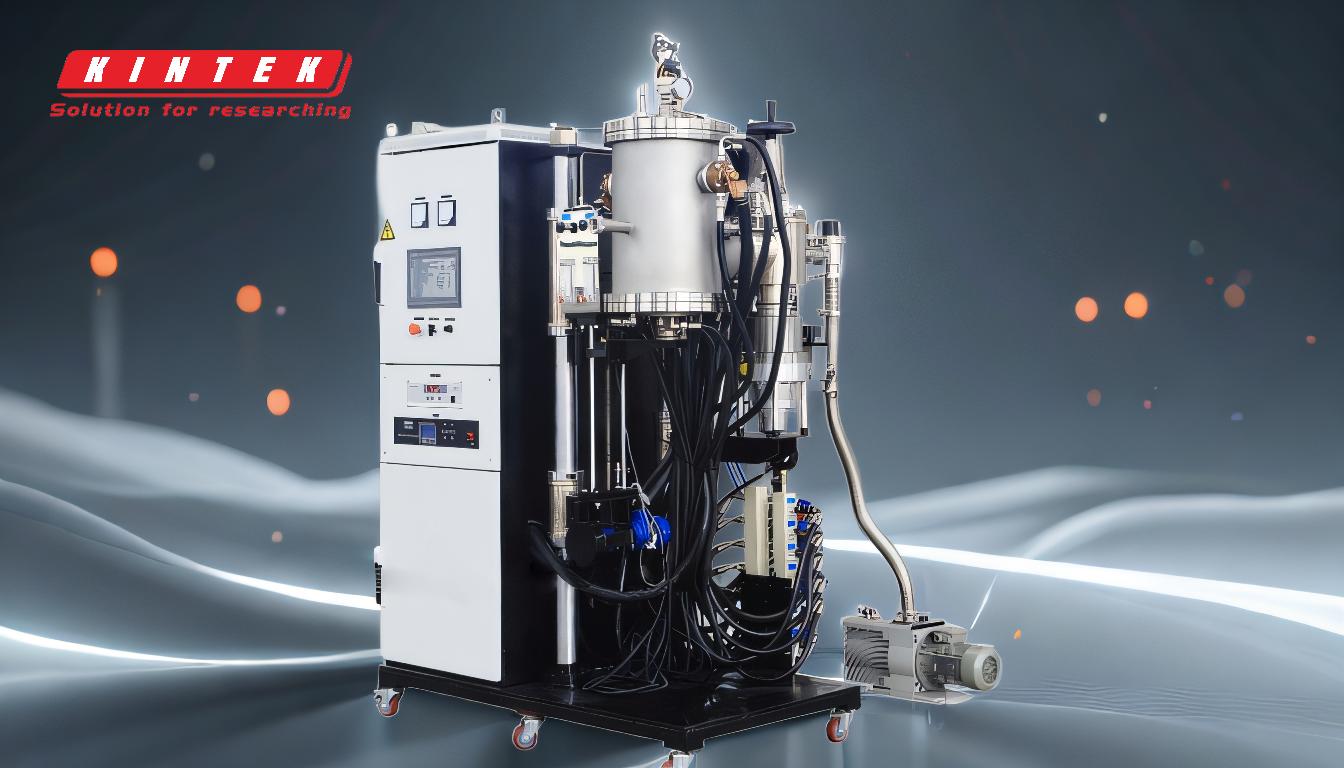
-
Cost-Effectiveness
- Sintering reduces material waste, as the process uses powder metallurgy to form parts directly from raw materials. This minimizes scrap and lowers production costs.
- The process is energy-efficient compared to traditional melting methods, as it does not require melting the metal, which is particularly beneficial for high-melting-point materials.
- It eliminates the need for additional machining or finishing in many cases, further reducing costs.
-
Material Versatility
- Sintering allows the use of a wide range of materials, including metals, ceramics, and composites. This flexibility enables the production of parts with tailored material compositions to meet specific application requirements.
- It can integrate high-melting-point materials that are difficult to process using conventional methods.
-
Complex Shapes and Intricate Designs
- Sintering excels in producing parts with complex geometries and intricate designs that would be challenging or impossible to achieve with traditional manufacturing techniques.
- The process allows for precise control over part dimensions and tolerances, ensuring consistency and accuracy.
-
Enhanced Mechanical Properties
- The sintering process improves material properties such as strength, durability, and structural integrity by reducing porosity and forming sintered necks between particles.
- It enhances properties like thermal and electrical conductivity, making sintered components suitable for high-performance applications.
-
Environmental Friendliness
- Sintering generates less waste compared to traditional manufacturing methods, as it uses near-net-shape production.
- The process is energy-efficient and reduces the carbon footprint associated with part production.
-
Excellent Surface Finish and Tolerance Control
- Sintered parts often require minimal post-processing, as the process inherently produces smooth surface finishes.
- Tight tolerance control ensures that parts meet precise specifications, reducing the need for additional machining.
-
Improved Performance Properties
- Sintering enhances properties such as translucency, thermal conductivity, and electrical conductivity, making it suitable for specialized applications like heat pipes, bearings, and electrical components.
- The process can also create specific material porosity, which is useful in applications like filters or self-lubricating bearings.
-
Consistency and Control in Production
- Sintering provides better control over the manufacturing process, leading to consistent results and fewer imperfections.
- The ability to diffuse elements like nickel, copper, and graphite during sintering further enhances the material's properties and performance.
In summary, sintered components are highly advantageous due to their cost-effectiveness, material versatility, ability to produce complex shapes, and enhanced mechanical and performance properties. These benefits make sintering a preferred manufacturing method across industries, from automotive to electronics and beyond.
Summary Table:
Advantage | Key Benefits |
---|---|
Cost-Effectiveness | Reduces material waste, energy-efficient, lowers production costs |
Material Versatility | Works with metals, ceramics, composites; integrates high-melting-point materials |
Complex Shapes | Produces intricate designs with precise tolerances |
Enhanced Mechanical Properties | Improves strength, durability, and conductivity |
Environmental Friendliness | Minimizes waste and energy consumption, reduces carbon footprint |
Surface Finish & Tolerance | Smooth finishes, tight tolerances, minimal post-processing |
Performance Properties | Enhances thermal/electrical conductivity, translucency, and porosity control |
Consistency in Production | Ensures uniform results, fewer imperfections, and better process control |
Unlock the potential of sintered components for your industry—contact our experts today!