Sintering in powder metallurgy is a highly advantageous manufacturing process that offers numerous benefits, including the ability to produce complex shapes with high precision, improved material properties, cost-effectiveness, and environmental sustainability. This process involves compacting metal powders into a desired shape and then heating them below their melting point to bond the particles together. The result is a strong, durable, and precise component that can be tailored to specific applications. Key advantages include the ability to work with high-melting-point metals, reduce porosity, enhance mechanical and thermal properties, and achieve high repeatability in manufacturing.
Key Points Explained:
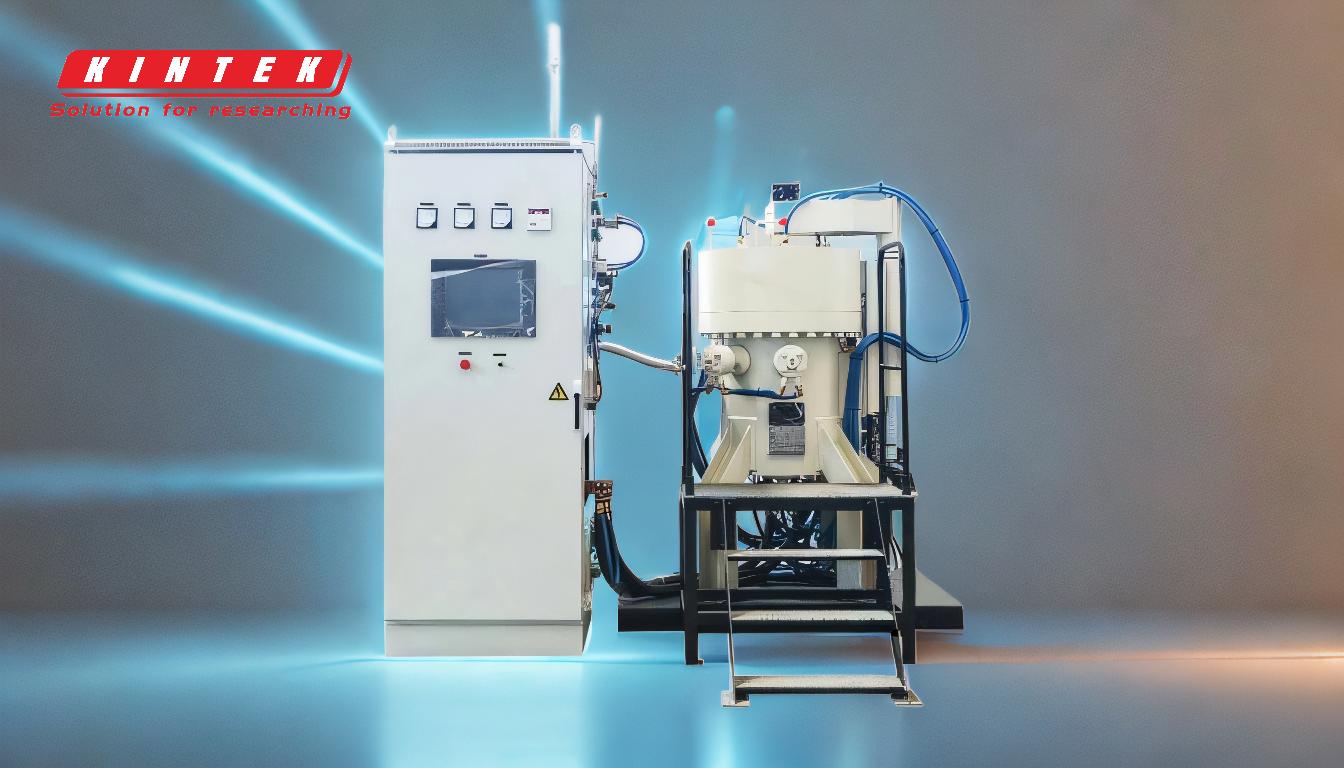
-
Production of Complex Shapes with High Precision
- Sintering allows for the creation of intricate external and internal geometries that would be difficult or impossible to achieve with traditional manufacturing methods.
- This is facilitated by the use of molds and dies made with wire EDM (Electrical Discharge Machining), which can achieve centesimal tolerances (0.01 mm).
- Examples include components with internal channels, undercuts, or complex surface textures, which are critical in industries like automotive, aerospace, and medical devices.
-
Improved Material Properties
- Sintering reduces porosity in the final product, enhancing properties such as strength, durability, electrical conductivity, and thermal conductivity.
- The process develops sintered necks between particles, which bond together to create a solid structure with minimal voids.
- This is particularly useful for applications requiring high mechanical performance, such as bearings, gears, and structural components.
-
Tailored Material Compositions
- Sintering enables the incorporation of alloying elements like nickel, copper, and graphite into the metal powder mix, allowing for customized material properties.
- This flexibility is valuable for meeting specific customer requirements, such as enhanced wear resistance, improved thermal conductivity, or controlled porosity for filters and catalysts.
-
Cost-Effectiveness
- Sintering is a near-net-shape manufacturing process, meaning the final product requires minimal machining or finishing, reducing material waste and production costs.
- It also uses less energy compared to melting metals, making it an environmentally friendly and economical option.
-
Versatility in Material Selection
- Sintering is particularly beneficial for materials with high melting points, large differences in melting points of constituent elements, and poor castability.
- Examples include tungsten, molybdenum, and ceramics, which are challenging to process using traditional methods.
-
High Repeatability and Consistency
- The sintering process is highly repeatable, ensuring consistent quality across large production runs.
- This reliability is critical for industries where precision and uniformity are paramount, such as electronics and medical devices.
-
Environmental and Energy Efficiency
- Sintering operates at lower temperatures compared to melting, reducing energy consumption and greenhouse gas emissions.
- The elimination of lubricants in the compacted powder and the reduction of surface oxygen further contribute to its eco-friendly nature.
-
Applications Across Industries
- Sintering is used to manufacture a wide range of products, including bearings, jewelry, heat pipes, shotgun shells, and filters.
- Its ability to produce components with specific porosity levels makes it ideal for applications like catalysts and filtration systems.
By leveraging these advantages, sintering in powder metallurgy provides a versatile, efficient, and sustainable manufacturing solution for a wide range of industries and applications.
Summary Table:
Advantage | Description |
---|---|
Complex Shapes with High Precision | Achieve intricate geometries with centesimal tolerances (0.01 mm). |
Improved Material Properties | Reduced porosity enhances strength, durability, and conductivity. |
Tailored Material Compositions | Customize properties with alloying elements like nickel, copper, and graphite. |
Cost-Effectiveness | Near-net-shape process reduces material waste and energy consumption. |
Versatility in Material Selection | Ideal for high-melting-point metals and challenging materials like ceramics. |
High Repeatability and Consistency | Ensures uniform quality across large production runs. |
Environmental and Energy Efficiency | Lower temperatures and reduced emissions make it eco-friendly. |
Applications Across Industries | Used in automotive, aerospace, medical devices, and more. |
Ready to explore how sintering can transform your manufacturing process? Contact us today to learn more!