Brazing is a versatile joining process widely used across various industries due to its ability to create strong, leak-proof, and durable joints between metal components. It is particularly suited for applications involving thin or thick cross-sections, complex geometries, and assemblies with multiple joints. Industries such as automotive, aerospace, electronics, medical, power generation, and defense rely on brazing for producing critical components like engine parts, hydraulic fittings, HVAC systems, and precision engineering assemblies. The process is also ideal for components with restricted access or joints located below the surface, making it a preferred choice for manufacturing complex and high-performance parts.
Key Points Explained:
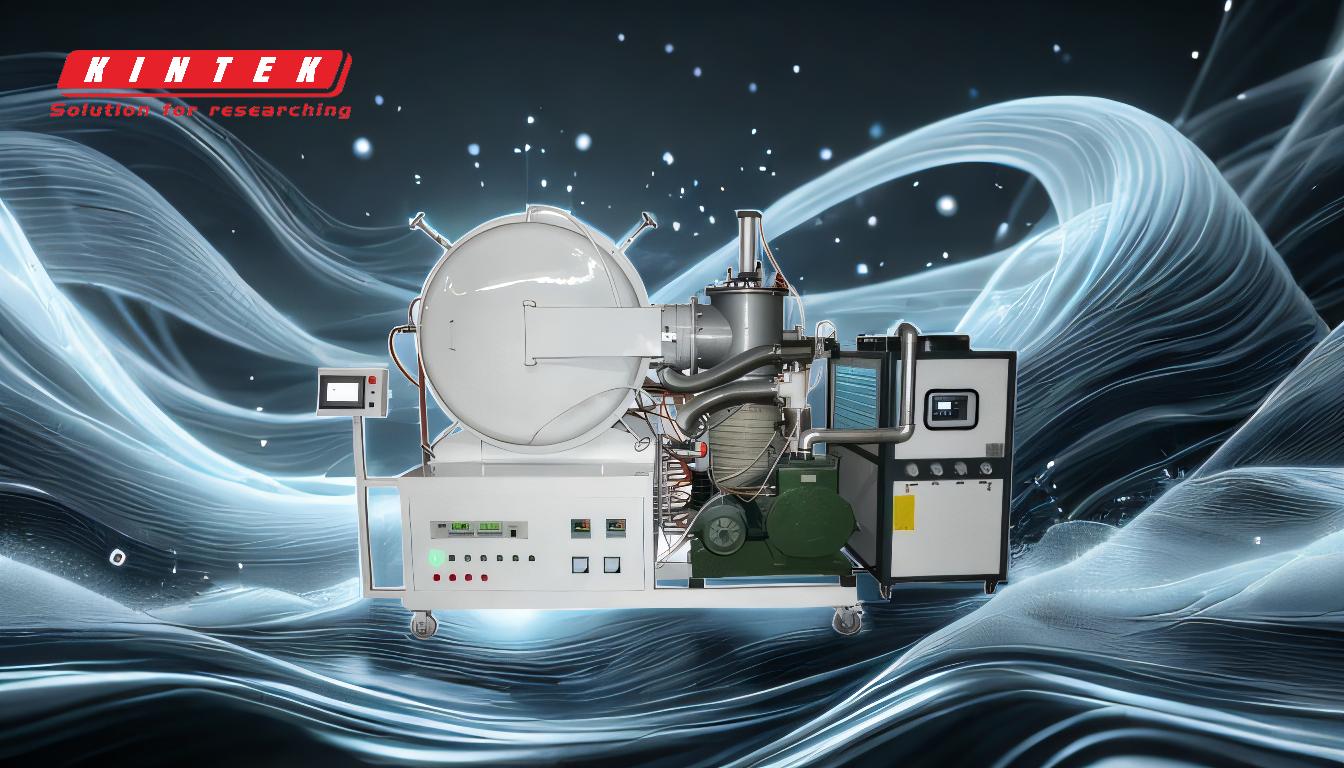
-
Automotive Industry Applications:
- Brazing is extensively used in the automotive sector for manufacturing engine components, exhaust systems, and heat exchangers.
- Examples include joining radiator cores, transmission parts, and fuel injection systems.
- The process ensures strong, leak-proof joints that can withstand high temperatures and mechanical stress.
-
Aerospace and Defense Applications:
- In aerospace, brazing is critical for producing turbine blades, heat exchangers, and structural components.
- It is also used in defense applications for manufacturing missile components, radar systems, and other high-performance assemblies.
- The ability to join dissimilar metals and create lightweight, durable joints makes brazing ideal for these industries.
-
Electronics and Electrical Components:
- Brazing is widely used in the electronics industry for joining electromechanical components, such as connectors, relays, and circuit breakers.
- It ensures reliable electrical conductivity and thermal management in devices like power modules and semiconductor packages.
-
HVAC and Refrigeration Systems:
- Brazing is a key process in the production of HVAC (Heating, Ventilation, and Air Conditioning) and refrigeration systems.
- It is used to join copper pipes, heat exchangers, and condensers, ensuring leak-proof and efficient thermal transfer.
-
Medical and Scientific Equipment:
- In the medical industry, brazing is used to manufacture precision components for surgical instruments, imaging devices, and diagnostic equipment.
- It is also applied in scientific equipment for creating vacuum-tight joints and assemblies that require high precision and reliability.
-
Power Generation and Industrial Applications:
- Brazing is employed in power generation for producing turbine components, heat exchangers, and nuclear reactor parts.
- It is also used in industrial gas turbines, offshore oil and gas equipment, and petrochemical processing systems.
-
Advantages of Brazing for Complex Components:
- Brazing is well-suited for parts with thin or thick cross-sections, joints located below the surface, or assemblies with restricted access.
- It is ideal for components with a large number of joints, such as heat exchangers and machined assemblies.
- The process allows for the joining of dissimilar metals, which is critical in many industrial applications.
-
Furnace Brazing for High-Volume Production:
- Furnace brazing is commonly used in industries like automotive, aerospace, and electronics for high-volume production of components.
- It ensures consistent quality and is suitable for complex assemblies with multiple joints.
-
Diverse Material Compatibility:
- Brazing can join a wide range of materials, including stainless steel, aluminum, copper, and nickel alloys.
- This versatility makes it applicable across various industries and for different types of components.
-
Environmental and Safety Considerations:
- Brazing is a cleaner and more environmentally friendly process compared to welding, as it produces fewer fumes and requires less energy.
- It is also safer for operators, as it typically involves lower temperatures and reduced risk of distortion or damage to the components.
In summary, brazing is a critical joining process used across multiple industries for manufacturing high-performance, durable, and precision components. Its ability to handle complex geometries, dissimilar materials, and high-volume production makes it indispensable in modern industrial applications.
Summary Table:
Industry | Applications |
---|---|
Automotive | Engine components, exhaust systems, heat exchangers, radiator cores |
Aerospace & Defense | Turbine blades, missile components, radar systems, structural parts |
Electronics | Connectors, relays, circuit breakers, power modules |
HVAC & Refrigeration | Copper pipes, heat exchangers, condensers |
Medical & Scientific | Surgical instruments, imaging devices, vacuum-tight joints |
Power Generation | Turbine components, nuclear reactor parts, industrial gas turbines |
Industrial Applications | Offshore oil and gas equipment, petrochemical systems |
Interested in how brazing can enhance your manufacturing process? Contact us today for expert guidance!