Hardening of steel is a critical process in metallurgy that enhances the mechanical properties of steel, making it suitable for a wide range of applications. This process involves heating the steel to a specific temperature and then rapidly cooling it, typically through quenching, to increase its hardness and strength. The applications of hardened steel are vast, ranging from industrial machinery and automotive components to construction tools and consumer goods. By understanding the key applications, one can appreciate the importance of this process in modern manufacturing and engineering.
Key Points Explained:
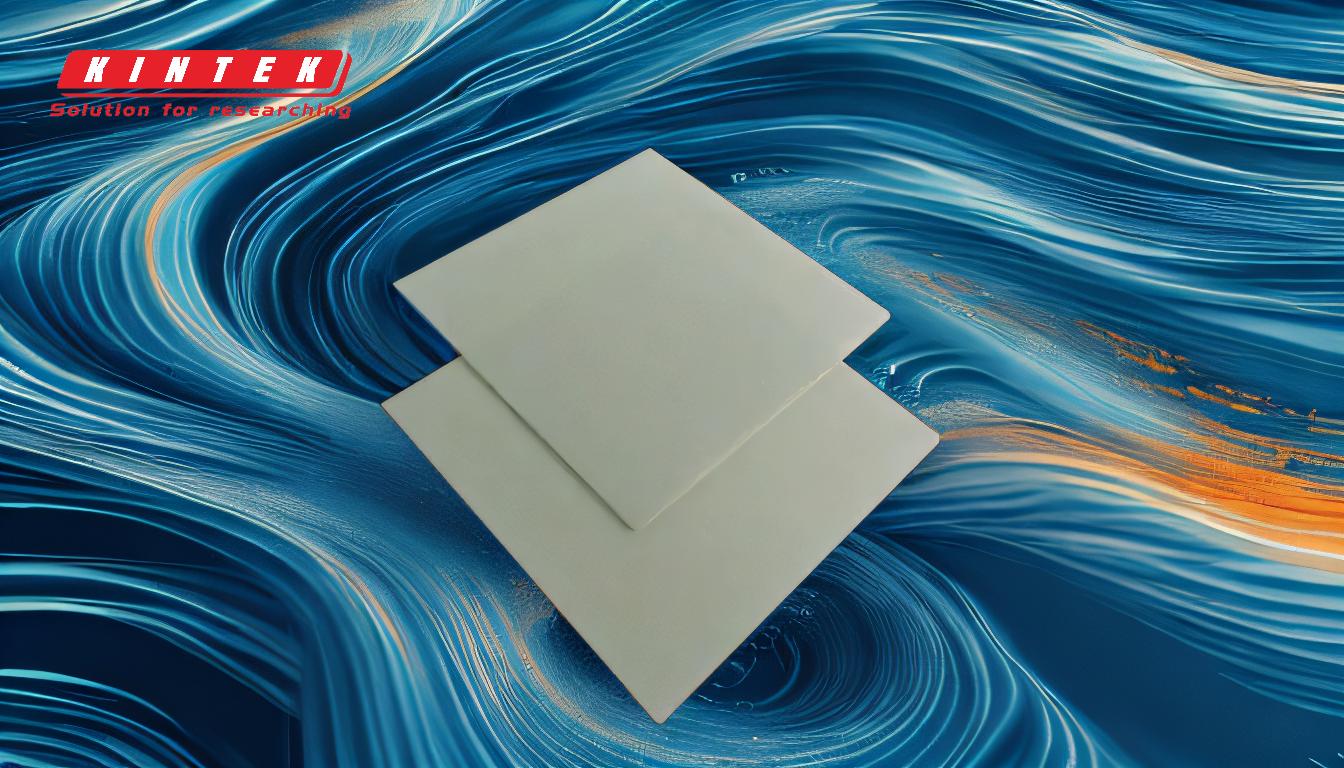
-
Industrial Machinery and Tools:
- Hardened steel is extensively used in the manufacturing of industrial machinery and tools. This includes components like gears, shafts, bearings, and cutting tools.
- The increased hardness and wear resistance of hardened steel ensure that these components can withstand high stress and repetitive use, thereby extending their lifespan and reducing maintenance costs.
- For example, cutting tools made from hardened steel can maintain their sharpness and precision over prolonged periods, which is crucial for maintaining high production standards.
-
Automotive Industry:
- The automotive industry relies heavily on hardened steel for various critical components such as engine parts, transmission systems, and suspension components.
- Hardened steel provides the necessary strength and durability to withstand the harsh conditions and high loads experienced by automotive parts.
- For instance, hardened steel is used in the production of crankshafts and camshafts, which are subjected to continuous cyclic loading and require high fatigue resistance.
-
Construction and Infrastructure:
- In the construction sector, hardened steel is used in the production of structural components, fasteners, and reinforcement bars.
- The enhanced mechanical properties of hardened steel make it ideal for applications where high strength and durability are required, such as in bridges, high-rise buildings, and heavy machinery.
- Reinforced concrete structures often use hardened steel bars to provide additional tensile strength, ensuring the stability and longevity of the construction.
-
Consumer Goods and Appliances:
- Hardened steel is also found in various consumer goods and household appliances, including kitchen utensils, hand tools, and electronic devices.
- The use of hardened steel in these products ensures that they are durable, resistant to wear, and capable of performing their intended functions effectively.
- For example, hardened steel is commonly used in the blades of kitchen knives, providing the necessary sharpness and edge retention for efficient cutting.
-
Aerospace and Defense:
- The aerospace and defense industries utilize hardened steel for components that require exceptional strength, toughness, and resistance to extreme conditions.
- Applications include aircraft landing gear, missile components, and armor plating.
- The ability of hardened steel to withstand high impact and stress makes it indispensable in these high-stakes environments.
-
Medical Devices and Equipment:
- In the medical field, hardened steel is used in the production of surgical instruments, implants, and diagnostic equipment.
- The biocompatibility, strength, and corrosion resistance of hardened steel are critical for ensuring the safety and effectiveness of medical devices.
- Surgical tools made from hardened steel can maintain their precision and durability even after repeated sterilization cycles.
-
Energy Sector:
- The energy sector, including oil and gas, nuclear, and renewable energy, relies on hardened steel for various applications such as drilling equipment, pipelines, and turbine components.
- The high strength and resistance to wear and corrosion of hardened steel are essential for the demanding conditions encountered in energy extraction and production.
- For example, drill bits used in oil and gas exploration are often made from hardened steel to withstand the abrasive and high-pressure environments.
In summary, the hardening of steel is a versatile and essential process that significantly enhances the mechanical properties of steel, making it suitable for a wide range of applications across various industries. From industrial machinery and automotive components to construction tools and consumer goods, the benefits of hardened steel are evident in the durability, strength, and performance of the products it is used to manufacture. Understanding these applications helps in appreciating the critical role that hardened steel plays in modern engineering and manufacturing.
Summary Table:
Industry | Applications |
---|---|
Industrial Machinery & Tools | Gears, shafts, bearings, cutting tools |
Automotive | Engine parts, transmission systems, suspension components |
Construction & Infrastructure | Structural components, fasteners, reinforcement bars |
Consumer Goods & Appliances | Kitchen utensils, hand tools, electronic devices |
Aerospace & Defense | Aircraft landing gear, missile components, armor plating |
Medical Devices & Equipment | Surgical instruments, implants, diagnostic equipment |
Energy Sector | Drilling equipment, pipelines, turbine components |
Unlock the potential of hardened steel for your industry—contact our experts today to learn more!