Heat treatment processes are widely used across various industries to enhance the physical and chemical properties of metals, making them suitable for specific applications. These processes involve controlled heating and cooling to achieve desired characteristics such as increased strength, ductility, toughness, and surface hardness. Industries like aviation, automotive, healthcare, energy, and electronics rely on heat treatment to improve the performance, durability, and longevity of metal components. Common processes include annealing, tempering, carburizing, and quenching, each tailored to modify specific properties of metals for industrial use.
Key Points Explained:
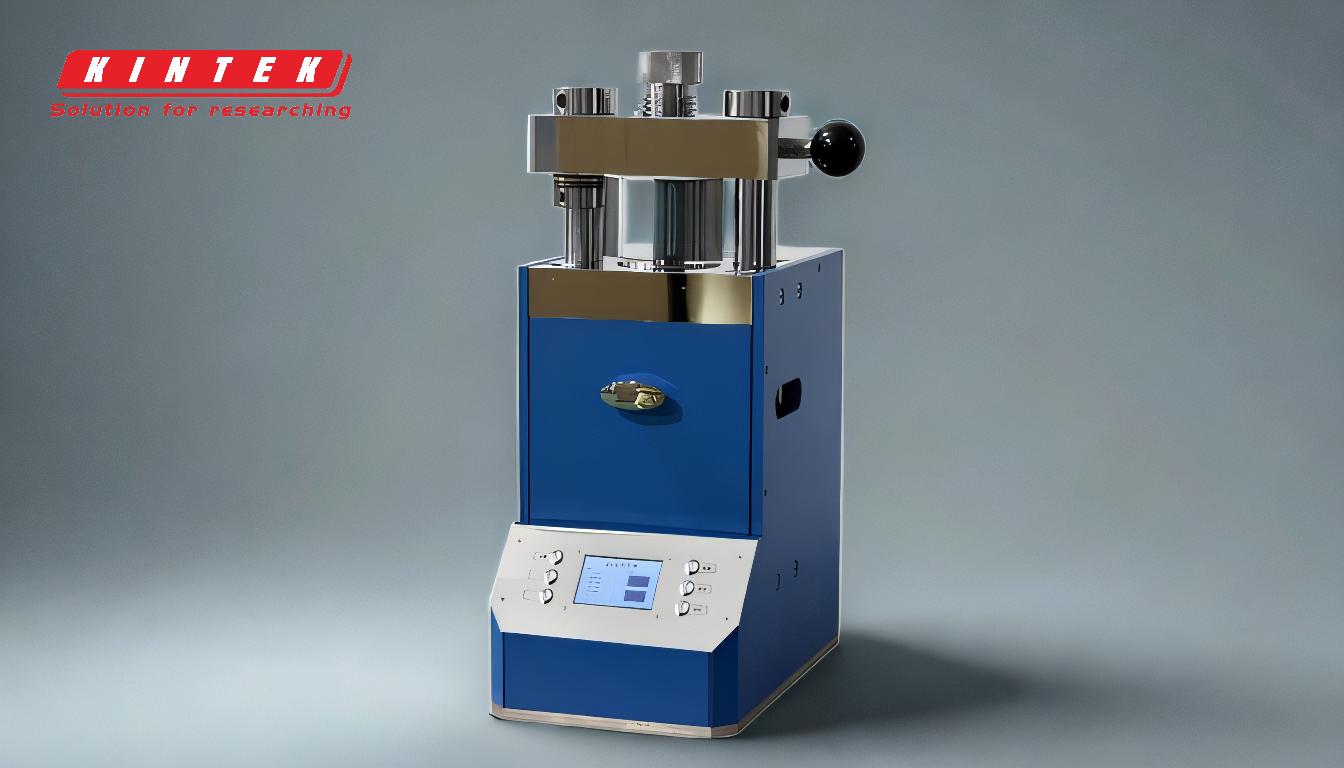
-
Improving Material Properties:
- Heat treatment processes are primarily used to alter the physical and chemical properties of metals. For example:
- Annealing softens metals, making them more ductile and easier to machine.
- Tempering increases toughness and reduces brittleness in hardened metals.
- Carburizing and case hardening enhance surface hardness while maintaining a tough core.
- Quenching rapidly cools metals to increase hardness and strength.
- These modifications make metals more versatile and suitable for demanding applications.
- Heat treatment processes are primarily used to alter the physical and chemical properties of metals. For example:
-
Applications in Key Industries:
- Aviation: Heat-treated components like turbine blades and landing gear must withstand extreme stress and temperature variations.
- Automotive: Engine parts, gears, and suspension components are heat-treated to improve durability and wear resistance.
- Healthcare: Surgical instruments and implants require precise heat treatment to ensure biocompatibility and strength.
- Energy: Heat treatment is critical for components in power plants, wind turbines, and oil rigs to endure harsh operating conditions.
- Electronics: Heat-treated metals are used in semiconductors and connectors to ensure reliability and performance.
-
Common Heat Treatment Processes:
- Annealing: Used to soften metals, reduce internal stresses, and improve machinability. Commonly applied to steel and copper alloys.
- Tempering: Follows quenching to balance hardness and toughness, often used in tool steels.
- Carburizing: Adds carbon to the surface of low-carbon steels to increase hardness while maintaining a ductile core.
- Quenching: Rapid cooling to achieve high hardness, often used in conjunction with tempering.
- Brazing: Joins metals using a filler material at high temperatures, commonly used in electronics and HVAC systems.
- Bright Annealing: Minimizes oxidation during annealing, ensuring a clean, shiny surface, often used for stainless steel.
-
Enhancing Durability and Longevity:
- Heat treatment extends the lifespan of metal components by improving their resistance to wear, fatigue, and corrosion.
- For example, case-hardened gears in automotive transmissions can withstand prolonged use without significant wear.
- Heat-treated turbine blades in aviation engines maintain their structural integrity under high temperatures and stress.
-
Tailored Solutions for Specific Needs:
- Different heat treatment processes are selected based on the desired outcome. For instance:
- Precipitation hardening is used for aluminum alloys to achieve high strength.
- Sintering is employed in powder metallurgy to create complex shapes with high density and strength.
- Bright annealing ensures a clean, oxidation-free surface for stainless steel used in medical devices.
- Different heat treatment processes are selected based on the desired outcome. For instance:
-
Role in Manufacturing Efficiency:
- Heat treatment is integral to manufacturing processes, enabling the production of components with precise properties.
- It reduces the need for additional machining or surface treatments, saving time and costs.
- For example, heat-treated fasteners and bolts are ready for immediate use without further processing.
-
Environmental and Safety Considerations:
- Heat treatment often involves controlled atmospheres (e.g., hydrogen, nitrogen, argon) to prevent oxidation and ensure consistent results.
- Modern heat treatment technologies focus on energy efficiency and reducing environmental impact, making them sustainable for large-scale industrial use.
By understanding the applications and benefits of heat treatment processes, manufacturers and engineers can select the appropriate methods to optimize the performance of metal components across various industries.
Summary Table:
Process | Purpose | Common Applications |
---|---|---|
Annealing | Softens metals, improves ductility, reduces internal stresses | Steel, copper alloys |
Tempering | Increases toughness, reduces brittleness | Tool steels |
Carburizing | Enhances surface hardness, maintains ductile core | Low-carbon steels |
Quenching | Increases hardness and strength | Hardened metals |
Brazing | Joins metals using filler material | Electronics, HVAC systems |
Bright Annealing | Minimizes oxidation, ensures clean surface | Stainless steel for medical devices |
Optimize your metal components with the right heat treatment process—contact our experts today!