Induction heating is a versatile and efficient method of heating that finds applications across a wide range of industries and processes. It utilizes electromagnetic induction to generate heat within conductive materials, offering precise, localized, and rapid heating without direct contact. Its applications span from industrial processes like metallurgy, semiconductor manufacturing, and surface hardening to domestic uses such as induction cooktops. Emerging applications include medical uses and advanced material development. The technology is valued for its energy efficiency, controllability, and ability to achieve high temperatures, making it indispensable in modern manufacturing and beyond.
Key Points Explained:
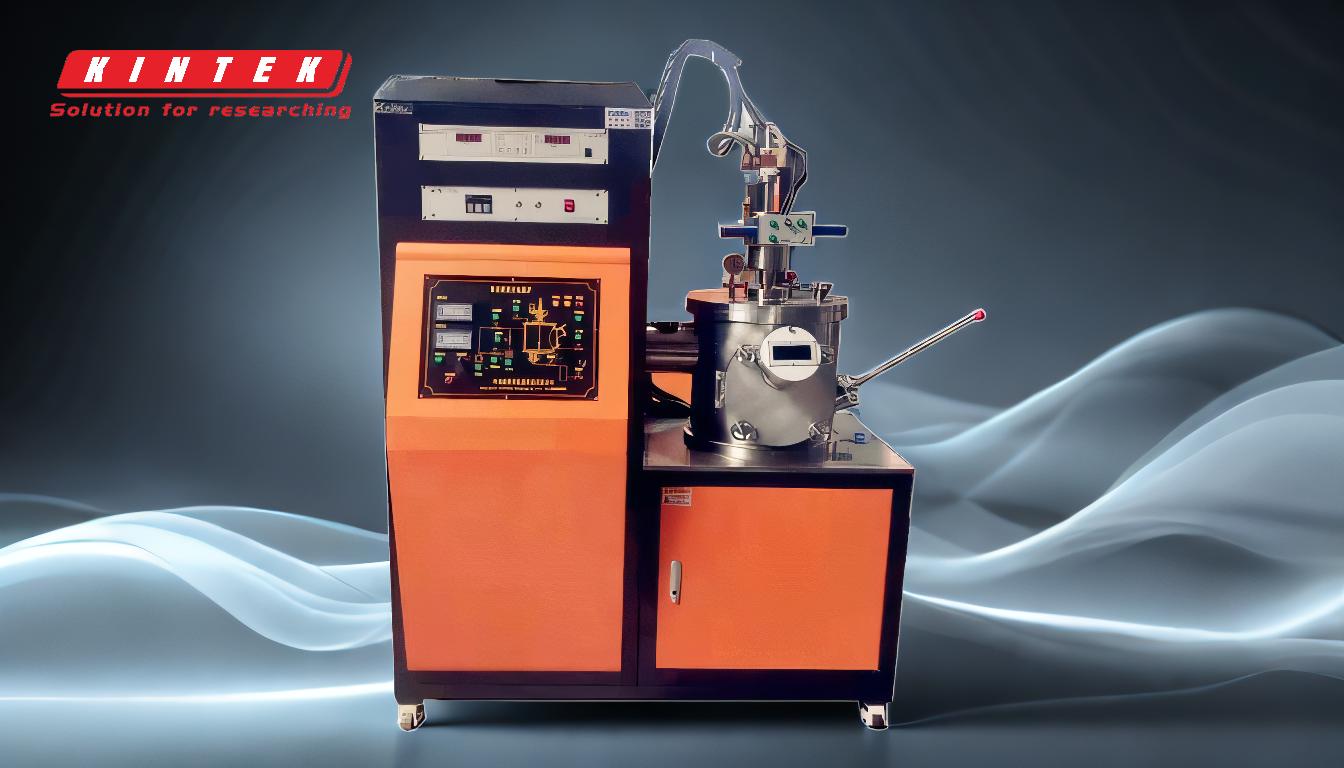
-
Industrial Heat Treatment in Metallurgy:
- Induction heating is extensively used for heat treatment processes such as annealing, tempering, and hardening of metals.
- It allows for precise control over the heating process, ensuring uniform and consistent results.
- Surface hardening, in particular, benefits from induction heating, as it selectively heats the surface of steel components to high temperatures, followed by quenching to achieve a hardened outer layer while keeping the core unaffected. This results in case hardnesses ranging from 37 to 58 Rc.
-
Semiconductor Industry Applications:
- Induction heating plays a critical role in the semiconductor industry, particularly in processes like Czochralski crystal growth and zone refining.
- These processes require precise and controlled heating to produce high-purity silicon crystals and refine semiconductor materials.
- The ability to achieve high temperatures in a controlled environment makes induction heating ideal for these applications.
-
Melting Refractory Metals:
- Refractory metals, such as tungsten and molybdenum, require extremely high temperatures to melt.
- Induction heating is capable of reaching these temperatures, making it suitable for melting and processing such materials.
- This application is crucial in industries that rely on high-performance alloys and specialized metals.
-
Domestic Use: Induction Cooktops:
- Induction cooktops are a common household application of induction heating.
- They heat cookware directly through electromagnetic induction, offering faster heating, energy efficiency, and precise temperature control compared to traditional gas or electric stoves.
- This technology is becoming increasingly popular due to its safety and convenience.
-
Emerging and Specialized Applications:
- Induction heating is being explored for medical applications, such as targeted heating of biological tissues for therapeutic purposes.
- It is also used for heating low-resistivity materials, which are challenging to heat using conventional methods.
- Research is ongoing to optimize process parameters for these and other emerging applications, including the development of highly engineered materials and alternative energy technologies.
-
Surface Heating, Melting, and Soldering:
- Induction heating is widely used for surface heating, melting, and soldering in various industries.
- It provides localized heating, which is ideal for processes like brazing carbide to shafts or sealing tamper-resistant caps on bottles and pharmaceuticals.
- This precision minimizes heat-affected zones and reduces energy consumption.
-
Induction Furnaces and Vacuum Furnaces:
- Induction furnaces are used to melt metals, while vacuum furnaces utilize induction heating to produce specialized steel and alloys.
- These applications benefit from the ability of induction heating to achieve high temperatures in controlled environments, ensuring high-quality outputs.
-
Plastic Injection Molding:
- Induction heating is employed in plastic injection molding machines to improve energy efficiency.
- By heating molds and components precisely, it reduces cycle times and enhances the overall efficiency of the molding process.
-
Future Potential:
- Induction heating is expected to play a key role in the development of advanced materials, alternative energy solutions, and empowering developing countries.
- Its unique capabilities, such as fast, efficient, and precise heating, make it a valuable tool for engineers and designers in a wide range of applications.
In summary, induction heating is a transformative technology with applications spanning industrial, domestic, and emerging fields. Its ability to deliver precise, localized, and efficient heating makes it indispensable in modern manufacturing and beyond. As technology advances, its applications are expected to expand further, driving innovation across various sectors.
Summary Table:
Application | Key Benefits |
---|---|
Industrial Heat Treatment | Precise control, uniform results, surface hardening (37-58 Rc) |
Semiconductor Manufacturing | High-purity crystal growth, controlled heating for refining materials |
Melting Refractory Metals | Reaches extreme temperatures for tungsten, molybdenum, and high-performance alloys |
Domestic Induction Cooktops | Faster heating, energy efficiency, precise temperature control |
Emerging Medical Applications | Targeted heating for therapeutic purposes, low-resistivity material heating |
Surface Heating and Soldering | Localized heating for brazing, sealing, and reduced energy consumption |
Induction and Vacuum Furnaces | High-temperature melting and alloy production in controlled environments |
Plastic Injection Molding | Improved energy efficiency, reduced cycle times, and enhanced molding precision |
Future Potential | Advanced materials, alternative energy solutions, and global innovation |
Ready to explore how induction heating can transform your processes? Contact our experts today to learn more!