Using inert gases in welding, particularly in processes like Gas Tungsten Arc Welding (GTAW), offers significant benefits in preventing oxidation and ensuring high-quality welds. Inert gases, such as argon or helium, create a protective shield around the weld area, preventing reactive gases like oxygen and nitrogen from contaminating the molten metal. This shielding effect reduces the formation of defects such as porosity, improves weld strength, and enhances the overall appearance of the weld. By maintaining a clean and stable environment, inert gases also protect the tungsten electrode from contamination, ensuring consistent arc performance and extending the lifespan of welding equipment.
Key Points Explained:
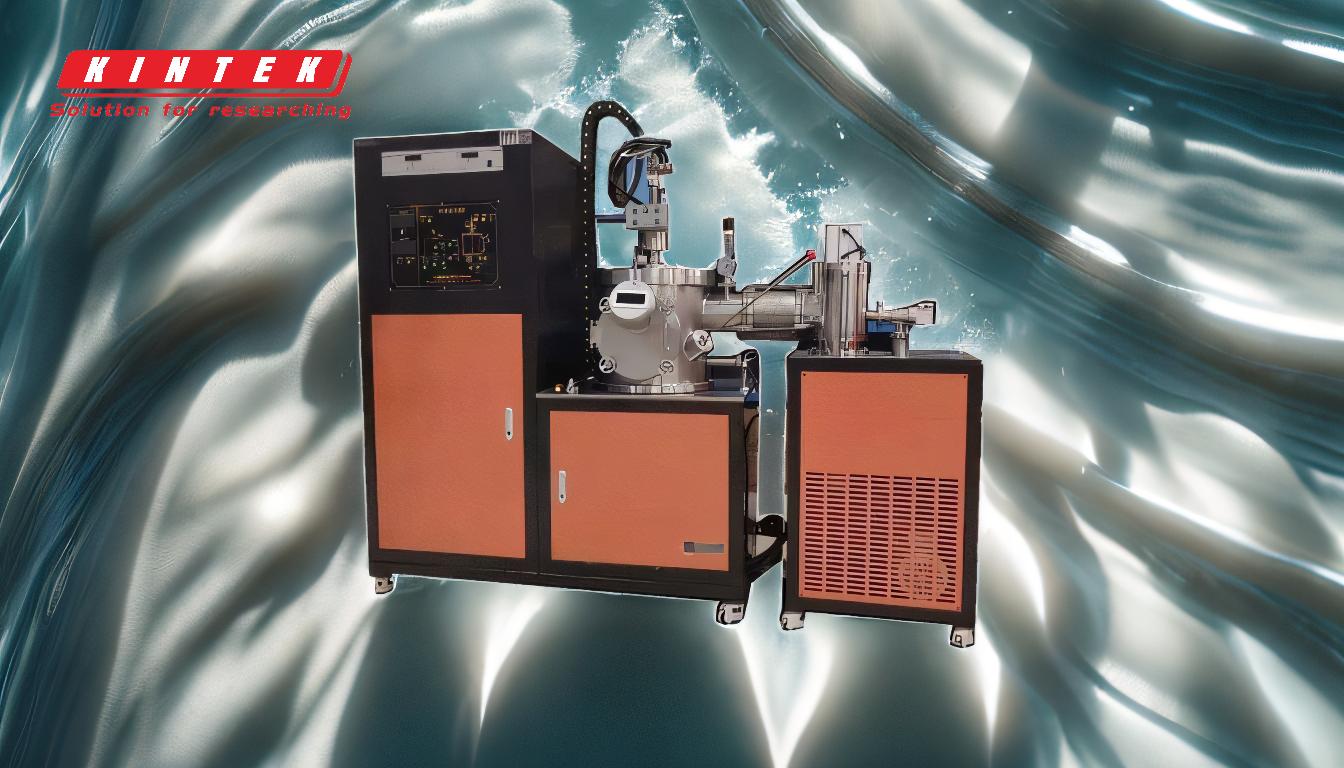
-
Prevention of Oxidation and Contamination
- Inert gases like argon and helium are chemically unreactive, meaning they do not react with the molten metal or the tungsten electrode.
- When used as a shielding gas, they displace reactive gases such as oxygen and nitrogen in the surrounding air, preventing oxidation and nitridation of the weld pool.
- Oxidation can lead to the formation of oxides, which weaken the weld and cause defects like porosity, cracks, and brittleness. By eliminating oxidation, inert gases ensure a cleaner, stronger weld.
-
Reduction of Porosity in Welds
- Porosity occurs when gases become trapped in the weld pool as it solidifies, creating voids or bubbles in the weld.
- Reactive gases like oxygen and nitrogen can dissolve into the molten metal and form bubbles as the metal cools.
- Inert gases prevent these gases from entering the weld pool, significantly reducing the risk of porosity and improving the structural integrity of the weld.
-
Protection of the Tungsten Electrode
- In GTAW, the tungsten electrode is critical for creating a stable arc. However, exposure to reactive gases can cause the electrode to degrade or become contaminated.
- Inert gases shield the electrode from oxidation and other chemical reactions, ensuring consistent arc performance and reducing the need for frequent electrode replacement.
- This protection also minimizes spatter and improves the precision of the welding process.
-
Improved Weld Appearance and Quality
- Inert gases create a stable and clean welding environment, which results in smoother, more uniform welds with fewer defects.
- The absence of oxidation and contamination leads to a brighter, cleaner weld surface, which is particularly important for aesthetic applications or when welding materials like stainless steel or aluminum.
- High-quality welds are essential for applications requiring strong, durable joints, such as in aerospace, automotive, and construction industries.
-
Enhanced Control Over the Welding Process
- Inert gases provide a consistent shielding environment, allowing welders to maintain better control over the heat input and weld pool dynamics.
- This control is especially important for welding thin materials or performing precision welds, where even minor defects can compromise the final product.
- The use of inert gases also reduces the likelihood of weld spatter, which can save time and resources during post-weld cleanup.
-
Compatibility with Reactive Metals
- Reactive metals like titanium, magnesium, and aluminum are highly susceptible to oxidation and contamination during welding.
- Inert gases are essential for welding these materials, as they prevent the formation of oxides and other compounds that can weaken the weld.
- This compatibility makes inert gases indispensable for industries that rely on lightweight, corrosion-resistant materials, such as aerospace and marine engineering.
-
Cost-Effectiveness in the Long Run
- While inert gases may have a higher upfront cost compared to reactive gases, their benefits often outweigh the initial investment.
- By reducing defects, improving weld quality, and extending the lifespan of welding equipment, inert gases can lower overall production costs.
- Additionally, the reduced need for post-weld repairs and rework saves time and labor, making inert gases a cost-effective choice for high-quality welding applications.
In summary, the use of inert gases in welding provides a comprehensive solution to prevent oxidation, reduce defects, and enhance the overall quality of welds. Their ability to create a stable and contamination-free environment makes them indispensable for critical welding applications across various industries.
Summary Table:
Key Benefits | Description |
---|---|
Prevents Oxidation | Shields the weld from reactive gases, reducing defects like porosity and cracks. |
Reduces Porosity | Minimizes trapped gases in the weld pool, improving structural integrity. |
Protects Tungsten Electrode | Ensures consistent arc performance and extends electrode lifespan. |
Enhances Weld Appearance | Produces cleaner, smoother welds with fewer defects. |
Improves Process Control | Provides a stable environment for precise welding of thin or delicate materials. |
Compatible with Reactive Metals | Essential for welding titanium, aluminum, and magnesium without contamination. |
Cost-Effective Long-Term | Reduces repair needs and equipment wear, lowering overall production costs. |
Ready to elevate your welding quality? Contact us today to learn more about using inert gases!