Fast pyrolysis is a highly efficient thermal conversion process designed to maximize the production of bio-oil from biomass. The process operates under specific conditions, including medium temperatures (typically 400–600°C), rapid heating rates (10^3 to 10^4 °C/s), and short residence times (less than 5 seconds). These conditions ensure the thermal decomposition of biomass in an inert atmosphere, preventing unwanted side reactions like combustion. The resulting vapor-gas mixture is then rapidly quenched to condense into bio-oil. The optimal temperature for bio-oil production is around 500°C, and the process requires precise control of heating rates and residence times to achieve high yields of liquid fuels.
Key Points Explained:
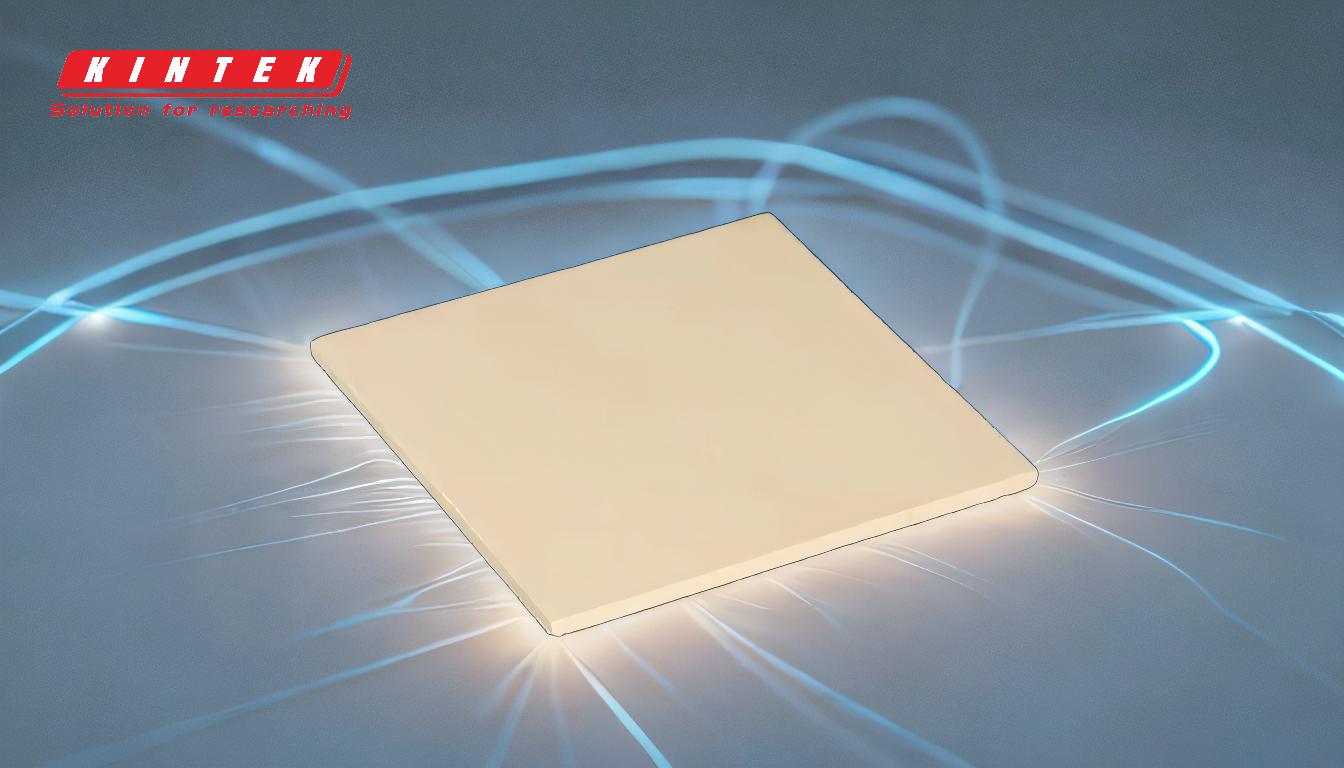
-
Temperature Range:
- Fast pyrolysis operates within a medium temperature range of 400–600°C, with an optimal temperature of 500°C for maximizing bio-oil production.
- Temperatures below this range may result in incomplete decomposition of biomass, while higher temperatures can lead to excessive gas production or char formation.
-
Heating Rate:
- The heating rate is critical and typically ranges between 10^3 to 10^4 °C/s. This rapid heating ensures that biomass particles decompose quickly, minimizing the formation of secondary products like char or gas.
- High heating rates are essential to achieve the desired bio-oil yield and quality.
-
Residence Time:
- Residence time refers to the duration that pyrolysis vapors remain in the reaction space. For fast pyrolysis, this is kept very short, typically less than 5 seconds.
- Short residence times prevent secondary reactions that could degrade the quality of the bio-oil or lead to the formation of unwanted byproducts.
-
Inert Atmosphere:
- Fast pyrolysis is conducted in an inert atmosphere (e.g., nitrogen or argon) to prevent oxidation or combustion of the biomass.
- The absence of oxygen ensures that the thermal decomposition process is controlled and that the primary product is bio-oil rather than gases or ash.
-
Rapid Quenching:
- After pyrolysis, the vapor-gas mixture is rapidly cooled or quenched to condense the bio-oil. This step is crucial for maximizing liquid yield and preventing further degradation of the pyrolysis products.
- Fast quenching ensures that the bio-oil is collected efficiently and retains its desired properties.
-
Biomass Particle Size:
- The size of biomass particles also plays a role in the efficiency of fast pyrolysis. Smaller particles heat more uniformly and rapidly, leading to better decomposition and higher bio-oil yields.
- Proper particle size control is necessary to achieve optimal results.
-
Avoidance of Side Reactions:
- By conducting pyrolysis in an inert atmosphere and controlling the residence time, side reactions such as combustion or hydrolysis are minimized.
- This ensures that the process remains focused on bio-oil production rather than generating unwanted byproducts.
-
Product Distribution:
- The primary product of fast pyrolysis is bio-oil, but the process also yields smaller amounts of char and non-condensable gases.
- The distribution of these products depends on the precise control of temperature, heating rate, and residence time.
By carefully managing these conditions, fast pyrolysis can efficiently convert biomass into bio-oil, making it a promising method for producing renewable liquid fuels. The process requires precise engineering and control to optimize yields and ensure the quality of the final product.
Summary Table:
Parameter | Optimal Range | Impact |
---|---|---|
Temperature Range | 400–600°C (optimal: 500°C) | Maximizes bio-oil yield; avoids incomplete decomposition or excessive gas. |
Heating Rate | 10^3 to 10^4 °C/s | Ensures rapid biomass decomposition, minimizing char or gas formation. |
Residence Time | Less than 5 seconds | Prevents secondary reactions, maintaining bio-oil quality. |
Inert Atmosphere | Nitrogen or argon | Prevents oxidation, ensuring controlled thermal decomposition. |
Rapid Quenching | Immediate cooling | Maximizes liquid yield and preserves bio-oil properties. |
Biomass Particle Size | Small, uniform particles | Enhances heating uniformity and decomposition efficiency. |
Interested in optimizing your bio-oil production? Contact our experts today to learn more about fast pyrolysis solutions!