Powder metallurgy (P/M) is a versatile manufacturing process that offers numerous advantages, such as high efficiency, low cost, and minimal waste. However, like any manufacturing method, it is not without its challenges. The most common defects in P/M parts include ejection cracks, density variations, microlaminations, and poor sintering. These defects can arise from various stages of the P/M process, including powder preparation, compacting, and sintering. Understanding these defects is crucial for improving the quality of P/M parts and ensuring their reliability in critical applications such as automotive and aerospace industries.
Key Points Explained:
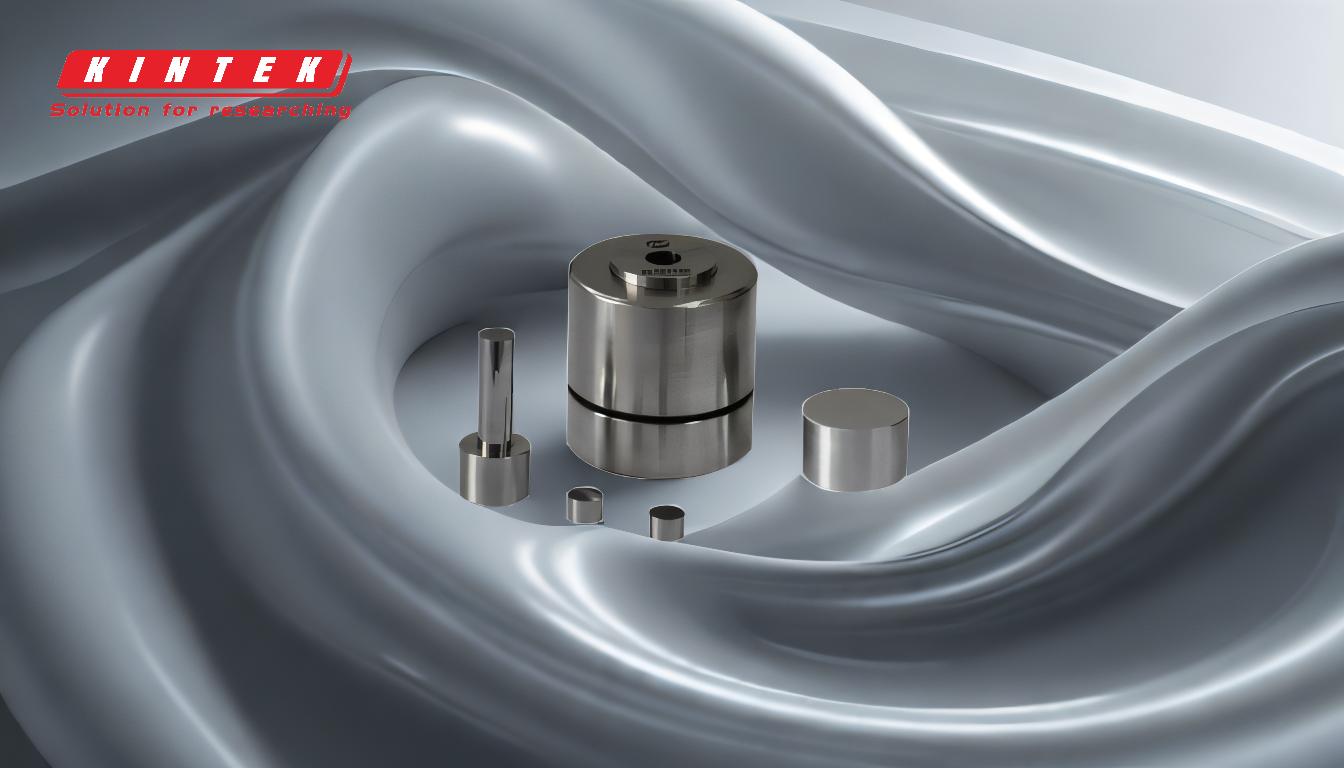
-
Ejection Cracks:
- Cause: Ejection cracks occur when the compacted powder part is ejected from the die. The friction between the part and the die, combined with the residual stresses from the compacting process, can cause cracks to form.
- Impact: These cracks can compromise the structural integrity of the part, leading to failure under stress.
- Prevention: Proper die design, lubrication, and controlled ejection forces can help minimize the occurrence of ejection cracks.
-
Density Variations:
- Cause: Density variations arise due to uneven distribution of powder during the compacting process. This can be due to improper die filling, inadequate pressing force, or variations in powder characteristics.
- Impact: Uneven density can lead to inconsistent mechanical properties, such as strength and wear resistance, across the part.
- Prevention: Ensuring uniform powder distribution, optimizing pressing parameters, and using high-quality powders can help achieve more consistent density.
-
Microlaminations:
- Cause: Microlaminations are thin layers of porosity or incomplete bonding between powder particles. They can occur due to insufficient compacting pressure or improper sintering conditions.
- Impact: These defects can act as stress concentrators, reducing the part's fatigue life and overall durability.
- Prevention: Adequate compacting pressure, proper sintering temperature, and time are essential to minimize microlaminations.
-
Poor Sintering:
- Cause: Poor sintering results from inadequate heating during the sintering process. This can be due to incorrect temperature, insufficient time, or improper atmosphere control.
- Impact: Poor sintering can lead to weak inter-particle bonds, resulting in parts with low strength and poor mechanical properties.
- Prevention: Accurate control of sintering temperature, time, and atmosphere is critical to ensure proper bonding and achieve the desired mechanical properties.
-
Process Variations and Their Impact on Defects:
- Conventional Methods: Traditional P/M processes are prone to defects like density variations and ejection cracks due to limitations in powder distribution and die design.
- Injection Molding: This method can reduce density variations but may introduce other defects like warping or incomplete filling if not properly controlled.
- Isostatic Pressing: This technique can produce parts with more uniform density, reducing the likelihood of density-related defects.
- Metal Additive Manufacturing: As the newest advancement, this method offers the potential for reduced defects due to precise layer-by-layer construction, but it also introduces new challenges like porosity and residual stresses.
-
Benefits of Powder Metallurgy:
- Despite these defects, P/M offers significant advantages, such as the ability to produce complex shapes with high precision, minimal material waste, and cost-effectiveness.
- The process is eco-friendly, with 97% of the material used becoming part of the final product, making it a sustainable choice for industries like automotive and aerospace.
In conclusion, while powder metallurgy is a highly efficient and cost-effective manufacturing process, it is essential to understand and address the common defects to ensure the production of high-quality parts. By optimizing each stage of the P/M process—powder preparation, compacting, and sintering—manufacturers can minimize defects and enhance the performance of P/M parts in critical applications.
Summary Table:
Defect | Cause | Impact | Prevention |
---|---|---|---|
Ejection Cracks | Friction during ejection, residual stresses | Structural integrity compromised, part failure under stress | Proper die design, lubrication, controlled ejection forces |
Density Variations | Uneven powder distribution, improper die filling, inadequate pressing | Inconsistent mechanical properties (strength, wear resistance) | Uniform powder distribution, optimized pressing, high-quality powders |
Microlaminations | Insufficient compacting pressure, improper sintering conditions | Stress concentrators, reduced fatigue life, poor durability | Adequate compacting pressure, proper sintering temperature and time |
Poor Sintering | Incorrect temperature, insufficient time, improper atmosphere control | Weak inter-particle bonds, low strength, poor mechanical properties | Accurate control of sintering temperature, time, and atmosphere |
Need help optimizing your powder metallurgy process? Contact our experts today for tailored solutions!