Brazing is a versatile joining process that involves the use of a filler metal to bond two or more base materials together. The process relies on heating the materials to a temperature above 450°C (842°F) but below the melting point of the base metals. The filler metal flows into the joint by capillary action, creating a strong and durable bond. There are several types of brazing methods, each suited to specific applications, materials, and production requirements. These methods vary based on the heating source, atmosphere, and equipment used. Below is a detailed explanation of the different types of brazing.
Key Points Explained:
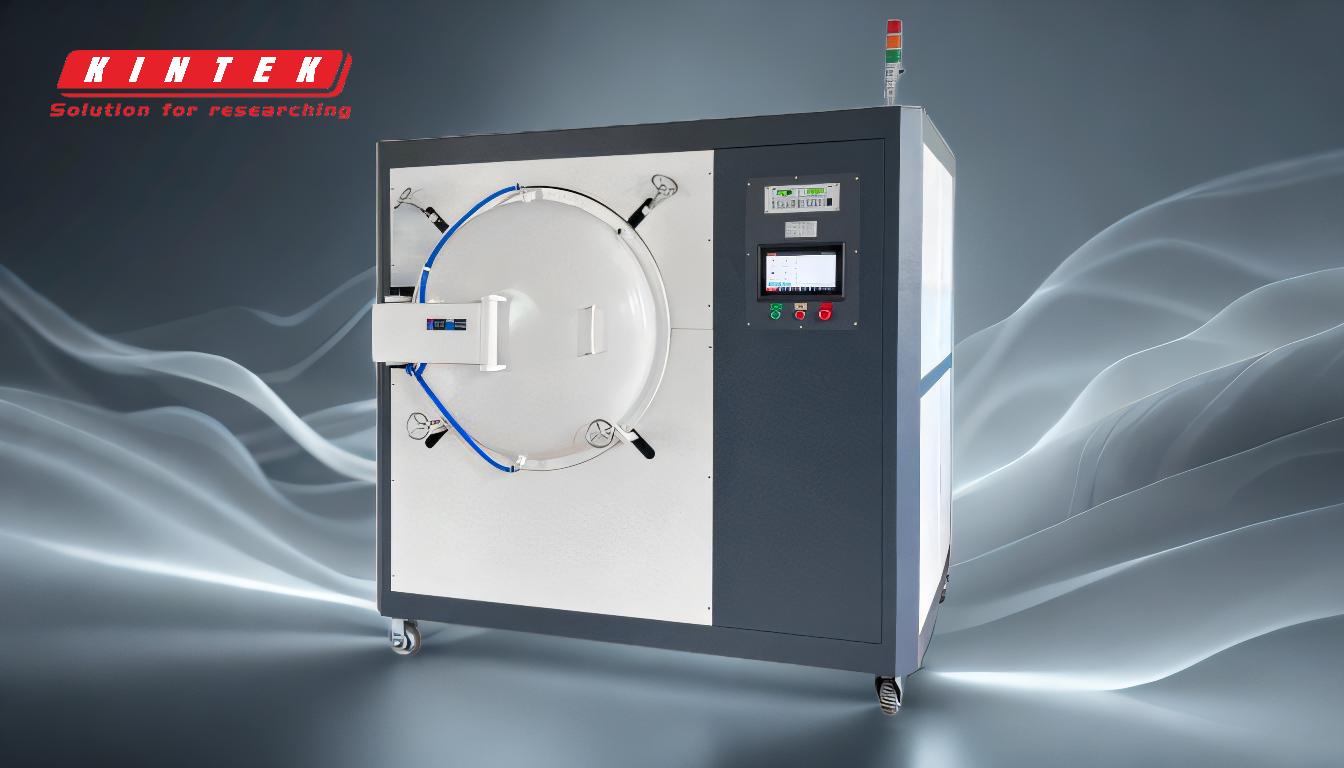
-
Torch Brazing
- Torch brazing is one of the most common and versatile methods, using a flame to heat the joint and filler metal.
- It is suitable for small-scale production, repairs, and field work.
- The heat source can be oxy-acetylene, propane, or other fuel gases, allowing for precise control over the heating process.
- This method is ideal for materials like copper, brass, and stainless steel.
-
Furnace Brazing
- Furnace brazing involves heating the entire assembly in a controlled environment, such as a furnace.
- It is highly efficient for mass production and complex assemblies.
- Different furnace atmospheres are used depending on the materials and filler metals:
- Exothermic Atmosphere: Reduces oxidation and is cost-effective.
- Hydrogen Atmosphere: Provides a reducing environment, ideal for stainless steel and other alloys.
- Argon Atmosphere: Inert gas prevents oxidation and is used for reactive materials.
- Vacuum Atmosphere: Eliminates oxidation entirely, suitable for high-performance materials like titanium and superalloys.
-
Induction Brazing
- Induction brazing uses electromagnetic induction to generate heat directly within the workpiece.
- It is fast, energy-efficient, and provides localized heating, minimizing thermal distortion.
- Commonly used for joining small components, such as electrical contacts and plumbing fittings.
-
Dip Brazing
- Dip brazing involves immersing the assembly into a molten salt bath or a bath of molten filler metal.
- The salt bath provides a protective atmosphere, preventing oxidation.
- This method is suitable for aluminum and other materials that require precise temperature control.
-
Resistance Brazing
- Resistance brazing uses electrical resistance to generate heat at the joint.
- It is similar to spot welding but uses a filler metal instead of fusion.
- This method is ideal for joining small, thin components, such as electrical connections.
-
Infrared Brazing
- Infrared brazing uses focused infrared radiation to heat the joint.
- It provides precise and localized heating, making it suitable for delicate or temperature-sensitive materials.
-
Blanket Brazing
- Blanket brazing uses a flexible heating blanket to apply heat to the joint.
- It is often used for large or irregularly shaped components, such as aerospace structures.
-
Electron Beam and Laser Brazing
- These advanced methods use high-energy beams to heat the joint.
- They offer exceptional precision and are used in high-tech industries, such as aerospace and medical devices.
- Electron beam brazing is performed in a vacuum, while laser brazing can be done in an open environment.
-
Braze Welding
- Braze welding is a hybrid process that combines brazing and welding techniques.
- It uses a filler metal with a melting point lower than the base metal but requires more heat than traditional brazing.
- This method is often used for repairing cast iron and other difficult-to-weld materials.
Each brazing method has its unique advantages and limitations, making it essential to choose the right technique based on the materials, joint design, and production requirements. By understanding the different types of brazing, equipment and consumable purchasers can make informed decisions to optimize their joining processes.
Summary Table:
Brazing Method | Key Features | Best For |
---|---|---|
Torch Brazing | Uses a flame for heating; versatile and precise. | Small-scale production, repairs, and materials like copper and stainless steel. |
Furnace Brazing | Heats assemblies in controlled environments; efficient for mass production. | Complex assemblies with materials like stainless steel, titanium, and alloys. |
Induction Brazing | Electromagnetic induction for fast, localized heating. | Small components like electrical contacts and plumbing fittings. |
Dip Brazing | Immerses assembly in molten salt or filler metal; prevents oxidation. | Aluminum and materials requiring precise temperature control. |
Resistance Brazing | Uses electrical resistance to generate heat. | Small, thin components like electrical connections. |
Infrared Brazing | Focused infrared radiation for precise heating. | Delicate or temperature-sensitive materials. |
Blanket Brazing | Uses flexible heating blankets for large or irregular components. | Aerospace structures and large assemblies. |
Electron Beam/Laser | High-energy beams for exceptional precision. | High-tech industries like aerospace and medical devices. |
Braze Welding | Combines brazing and welding; uses filler metal with lower melting point. | Repairing cast iron and difficult-to-weld materials. |
Need help choosing the right brazing method for your project? Contact our experts today to get started!