Ceramic sintering is a critical process in the production of ceramics, involving the consolidation of powdered materials into a solid structure through the application of heat, and sometimes pressure or electrical currents. The process reduces porosity and causes shrinkage as the particles bond together. Different types of ceramics require specific sintering techniques, ranging from simple kiln firing for materials like porcelain to more complex methods such as hot isostatic pressing or spark plasma sintering for advanced technical ceramics. The choice of sintering method depends on the material properties, desired final characteristics, and application requirements.
Key Points Explained:
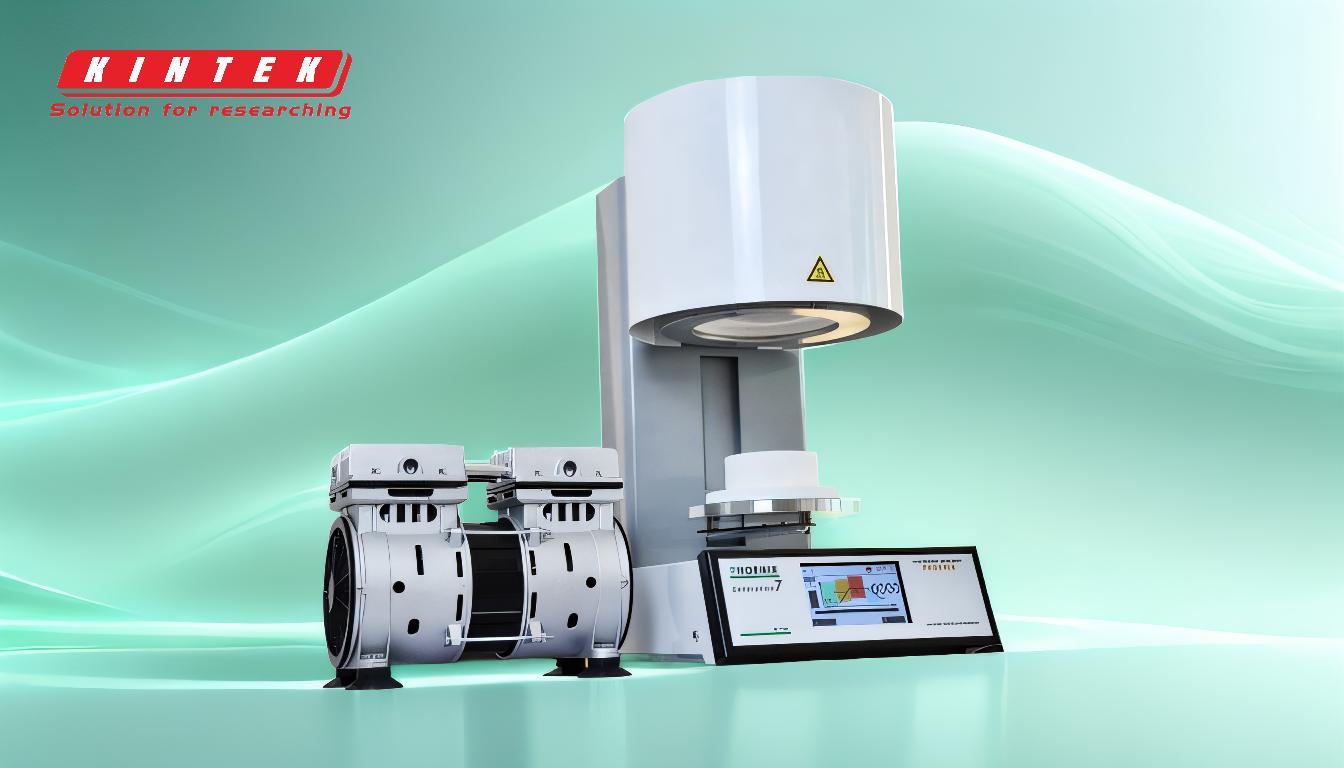
-
Solid-State Sintering:
- Process: Powdered material is heated just below its melting point, allowing particles to bond through atomic diffusion.
- Application: Commonly used for materials that do not require a liquid phase to achieve densification.
- Advantages: Simple and cost-effective for many ceramic materials.
- Considerations: Requires precise temperature control to avoid melting.
-
Liquid Phase Sintering:
- Process: A solvent liquid is introduced to reduce porosity and facilitate particle bonding. The liquid is later driven off by heating.
- Application: Suitable for ceramics that benefit from reduced porosity and enhanced bonding.
- Advantages: Can achieve high density and strong bonds.
- Considerations: The presence of a liquid phase can complicate the process and may require additional steps to remove the solvent.
-
Reactive Sintering:
- Process: Involves a chemical reaction between powder particles during heating, leading to densification.
- Application: Used for ceramics that require specific chemical compositions or properties.
- Advantages: Can produce unique material properties through in-situ reactions.
- Considerations: Requires careful control of reaction conditions to avoid unwanted phases or defects.
-
Microwave Sintering:
- Process: Uses microwave energy to rapidly heat the ceramic material, leading to faster integration and densification.
- Application: Ideal for materials that require rapid heating or have specific microwave absorption properties.
- Advantages: Faster processing times and potential energy savings.
- Considerations: Requires specialized equipment and may not be suitable for all materials.
-
Spark Plasma Sintering (SPS):
- Process: Combines electric current and physical compression to rapidly sinter ceramic powders.
- Application: Suitable for advanced technical ceramics that require high density and fine microstructures.
- Advantages: Rapid sintering with minimal grain growth, leading to superior mechanical properties.
- Considerations: High equipment costs and complexity.
-
Hot Isostatic Pressing (HIP):
- Process: Applies high pressure and temperature simultaneously to form and fuse powder particles.
- Application: Used for high-performance ceramics that require near-theoretical density and uniformity.
- Advantages: Produces materials with excellent mechanical properties and minimal defects.
- Considerations: Expensive and requires specialized equipment.
-
Conventional Sintering:
- Process: Involves heating the ceramic material in a kiln or furnace without additional pressure or electrical currents.
- Application: Common for traditional ceramics like pottery and porcelain.
- Advantages: Simple and widely applicable.
- Considerations: Limited to materials that can achieve densification through heat alone.
-
Hydrogen Protection and Vacuum Sintering:
- Process: Sintering is carried out in a controlled atmosphere, such as hydrogen or vacuum, to prevent oxidation or other reactions.
- Application: Used for ceramics that are sensitive to atmospheric conditions.
- Advantages: Prevents contamination and allows for precise control of the sintering environment.
- Considerations: Requires specialized equipment and careful handling of gases.
-
Hot Press Sintering:
- Process: Combines heat and uniaxial pressure to densify ceramic powders.
- Application: Suitable for materials that require high density and specific shapes.
- Advantages: Can achieve high density with controlled grain growth.
- Considerations: Limited to simple shapes due to the uniaxial pressure application.
-
Air Pressure Sintering:
- Process: Involves sintering under elevated air pressure to enhance densification.
- Application: Used for ceramics that benefit from increased pressure during sintering.
- Advantages: Can improve density and mechanical properties.
- Considerations: Requires specialized equipment capable of handling high pressures.
Each sintering method has its own set of advantages and considerations, making it essential to choose the appropriate technique based on the specific requirements of the ceramic material and its intended application. The selection of the sintering process can significantly impact the final properties of the ceramic, including density, strength, and microstructure.
Summary Table:
Sintering Method | Process Overview | Applications | Advantages | Considerations |
---|---|---|---|---|
Solid-State Sintering | Heated just below melting point; particles bond via atomic diffusion. | Materials without a liquid phase. | Simple and cost-effective. | Requires precise temperature control. |
Liquid Phase Sintering | Introduces a solvent liquid to reduce porosity; liquid is later removed by heating. | Ceramics needing reduced porosity and enhanced bonding. | High density and strong bonds. | Complicated by the liquid phase; additional steps to remove solvent. |
Reactive Sintering | Chemical reaction between particles during heating. | Ceramics requiring specific chemical compositions or properties. | Unique material properties through in-situ reactions. | Requires careful control of reaction conditions. |
Microwave Sintering | Uses microwave energy for rapid heating and densification. | Materials needing rapid heating or with microwave absorption properties. | Faster processing and potential energy savings. | Requires specialized equipment; not suitable for all materials. |
Spark Plasma Sintering | Combines electric current and compression for rapid sintering. | Advanced technical ceramics needing high density and fine microstructures. | Rapid sintering with minimal grain growth; superior mechanical properties. | High equipment costs and complexity. |
Hot Isostatic Pressing | Applies high pressure and temperature simultaneously. | High-performance ceramics requiring near-theoretical density and uniformity. | Excellent mechanical properties and minimal defects. | Expensive and requires specialized equipment. |
Conventional Sintering | Heating in a kiln or furnace without additional pressure or electrical currents. | Traditional ceramics like pottery and porcelain. | Simple and widely applicable. | Limited to materials densifying through heat alone. |
Hydrogen/Vacuum Sintering | Sintering in a controlled atmosphere (hydrogen or vacuum) to prevent oxidation. | Ceramics sensitive to atmospheric conditions. | Prevents contamination; precise control of the sintering environment. | Requires specialized equipment and careful handling of gases. |
Hot Press Sintering | Combines heat and uniaxial pressure for densification. | Materials needing high density and specific shapes. | High density with controlled grain growth. | Limited to simple shapes due to uniaxial pressure. |
Air Pressure Sintering | Sintering under elevated air pressure to enhance densification. | Ceramics benefiting from increased pressure during sintering. | Improved density and mechanical properties. | Requires specialized equipment for high pressures. |
Need help selecting the right sintering method for your ceramics? Contact our experts today for tailored solutions!