Chemical Vapor Deposition (CVD) is a versatile process used to produce high-quality, high-performance solid materials, typically in thin-film form. It involves the reaction of gaseous precursors to form a solid material on a substrate. The different types of CVD processes are categorized based on their operating conditions, such as pressure, temperature, and the use of additional energy sources like plasma or lasers. Each type of CVD has unique characteristics and is suited for specific applications, depending on the desired film properties and the materials involved.
Key Points Explained:
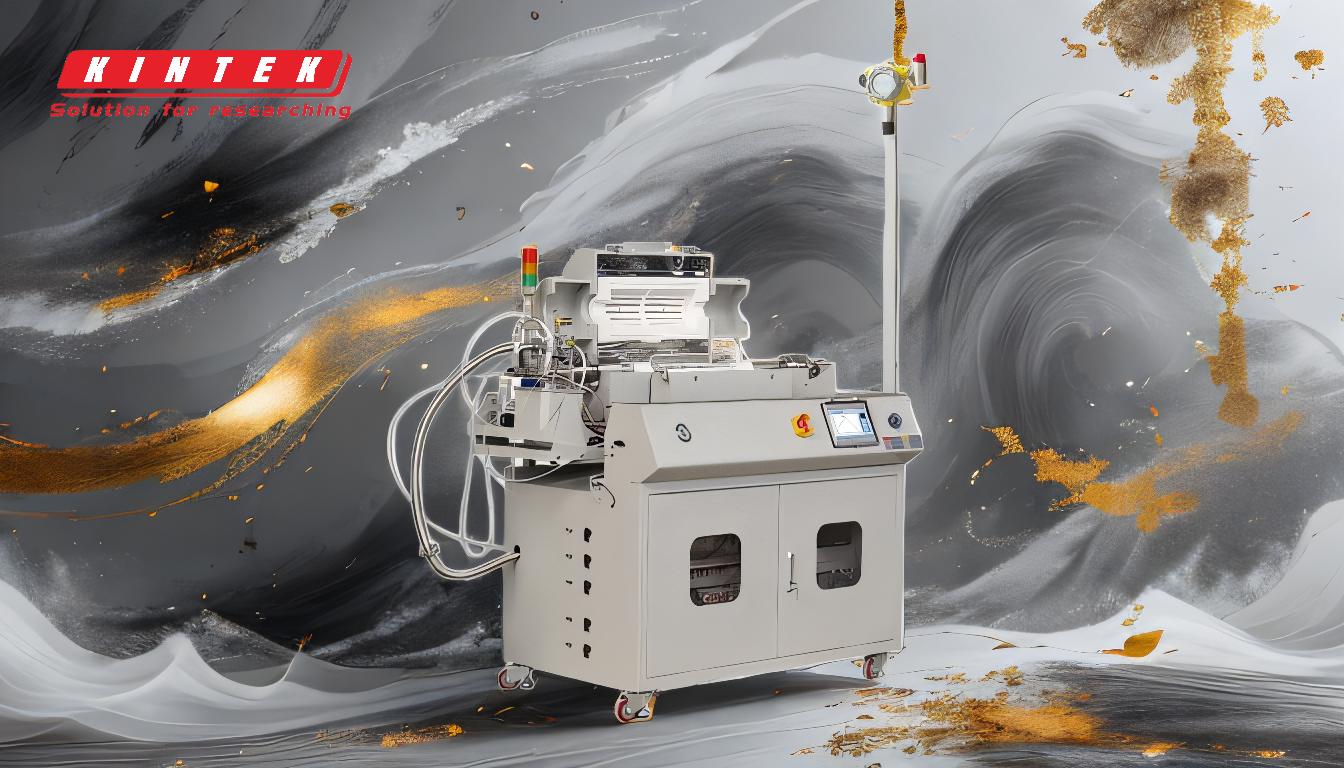
-
Atmospheric Pressure CVD (APCVD):
- Definition: APCVD operates at atmospheric pressure, making it one of the simplest forms of CVD.
- Applications: It is commonly used for depositing oxides, nitrides, and other materials where high purity is not the primary concern.
- Advantages: Simple setup, cost-effective, and suitable for large-scale production.
- Limitations: Limited to materials that can be deposited at atmospheric pressure without requiring high vacuum conditions.
-
Low-Pressure CVD (LPCVD):
- Definition: LPCVD operates at sub-atmospheric pressures, typically between 0.1 to 10 torr.
- Applications: Widely used in the semiconductor industry for depositing polysilicon, silicon nitride, and silicon dioxide.
- Advantages: Produces high-quality films with excellent uniformity and step coverage.
- Limitations: Requires more complex equipment compared to APCVD and may have slower deposition rates.
-
Ultrahigh Vacuum CVD (UHVCVD):
- Definition: UHVCVD operates at very low pressures, typically below 10^-6 Pa (≈ 10^-8 torr).
- Applications: Used for depositing high-purity materials, especially in research and development settings.
- Advantages: Produces extremely high-purity films with minimal contamination.
- Limitations: Requires sophisticated vacuum systems and is generally slower and more expensive.
-
Plasma-Enhanced CVD (PECVD):
- Definition: PECVD uses plasma to enhance the chemical reaction, allowing deposition at lower temperatures.
- Applications: Commonly used for depositing silicon nitride, silicon dioxide, and amorphous silicon in microelectronics and solar cells.
- Advantages: Lower deposition temperatures, which are beneficial for temperature-sensitive substrates.
- Limitations: More complex equipment and higher costs compared to thermal CVD processes.
-
Metal-Organic CVD (MOCVD):
- Definition: MOCVD uses metal-organic precursors to deposit compound semiconductors and other materials.
- Applications: Widely used in the production of LEDs, laser diodes, and high-efficiency solar cells.
- Advantages: Precise control over composition and doping, enabling the growth of complex multilayer structures.
- Limitations: Requires careful handling of toxic and pyrophoric precursors.
-
Laser-Induced CVD (LCVD):
- Definition: LCVD uses a laser to locally heat the substrate, inducing the deposition reaction.
- Applications: Used for selective area deposition and patterning in microfabrication.
- Advantages: High spatial resolution and the ability to deposit materials on heat-sensitive substrates.
- Limitations: Limited to small areas and requires precise control of laser parameters.
-
Aerosol-Assisted CVD (AACVD):
- Definition: AACVD uses an aerosol to deliver the precursor to the substrate.
- Applications: Suitable for depositing complex oxides and other materials where liquid precursors are advantageous.
- Advantages: Can use a wide range of precursors, including those that are not easily vaporized.
- Limitations: May require additional steps to generate and control the aerosol.
-
Hot-Wire CVD (HWCVD):
- Definition: HWCVD uses a hot filament to decompose the precursor gases.
- Applications: Used for depositing amorphous silicon and other materials in thin-film solar cells.
- Advantages: High deposition rates and the ability to operate at low pressures.
- Limitations: Filament degradation over time can affect process stability.
-
Atomic Layer CVD (ALCVD):
- Definition: ALCVD is a variant of CVD where the deposition occurs in a layer-by-layer fashion, with precise control over each atomic layer.
- Applications: Used for depositing ultra-thin films with atomic-level precision, such as in advanced semiconductor devices.
- Advantages: Excellent control over film thickness and composition.
- Limitations: Slower deposition rates and more complex process control.
-
Rapid Thermal CVD (RTCVD):
- Definition: RTCVD uses rapid thermal processing to heat the substrate, allowing for fast deposition rates.
- Applications: Used in semiconductor manufacturing for depositing silicon-based films.
- Advantages: High deposition rates and the ability to achieve high temperatures quickly.
- Limitations: Requires precise temperature control and may have limited uniformity over large areas.
-
Microwave Plasma-Assisted CVD (MPACVD):
- Definition: MPACVD uses microwave-generated plasma to enhance the deposition process.
- Applications: Used for depositing diamond films and other hard coatings.
- Advantages: High-energy plasma allows for the deposition of high-quality films at lower temperatures.
- Limitations: Requires specialized equipment and may have limited scalability.
-
Direct Liquid Injection CVD (DLICVD):
- Definition: DLICVD involves injecting a liquid precursor directly into the reaction chamber, where it is vaporized.
- Applications: Suitable for depositing complex oxides and other materials where liquid precursors are advantageous.
- Advantages: Precise control over precursor delivery and the ability to use a wide range of precursors.
- Limitations: Requires careful control of the injection process to avoid precursor decomposition.
Each type of CVD process has its own set of advantages and limitations, making it suitable for specific applications. The choice of CVD method depends on factors such as the desired film properties, substrate material, and production scale. Understanding these differences is crucial for selecting the appropriate CVD process for a given application.
Summary Table:
CVD Type | Key Features | Applications | Advantages | Limitations |
---|---|---|---|---|
APCVD | Operates at atmospheric pressure | Depositing oxides, nitrides | Simple setup, cost-effective | Limited to materials at atmospheric pressure |
LPCVD | Sub-atmospheric pressures (0.1–10 torr) | Polysilicon, silicon nitride, silicon dioxide | High-quality films, excellent uniformity | Complex equipment, slower deposition |
UHVCVD | Ultrahigh vacuum (below 10^-6 Pa) | High-purity materials, R&D | Extremely high-purity films | Sophisticated vacuum systems, expensive |
PECVD | Uses plasma for lower temperature deposition | Silicon nitride, silicon dioxide, amorphous silicon | Lower deposition temperatures | Complex equipment, higher costs |
MOCVD | Uses metal-organic precursors | LEDs, laser diodes, solar cells | Precise control over composition and doping | Handling toxic/pyrophoric precursors |
LCVD | Laser-induced local heating | Selective area deposition, microfabrication | High spatial resolution | Limited to small areas, precise laser control |
AACVD | Uses aerosol for precursor delivery | Complex oxides | Wide range of precursors | Additional steps for aerosol control |
HWCVD | Hot filament decomposes precursors | Amorphous silicon, thin-film solar cells | High deposition rates | Filament degradation over time |
ALCVD | Layer-by-layer deposition | Ultra-thin films, advanced semiconductors | Atomic-level precision | Slower deposition, complex process control |
RTCVD | Rapid thermal processing | Silicon-based films | High deposition rates, quick heating | Limited uniformity over large areas |
MPACVD | Microwave-generated plasma | Diamond films, hard coatings | High-quality films at lower temperatures | Specialized equipment, limited scalability |
DLICVD | Direct liquid injection of precursors | Complex oxides | Precise precursor delivery | Requires careful injection control |
Need help selecting the right CVD process for your application? Contact our experts today for tailored solutions!