Induction heating, particularly core type induction heating, is widely used in industrial applications due to its efficiency and precision. However, it comes with several disadvantages that can impact its suitability for certain applications. These include high initial costs, the need for specialized equipment and skilled personnel, limitations in refining capacity, challenges in managing high-current densities, and the requirement for robust control algorithms. Additionally, its effectiveness is primarily limited to surface heating, which may restrict its use in processes requiring uniform or deep heating.
Key Points Explained:
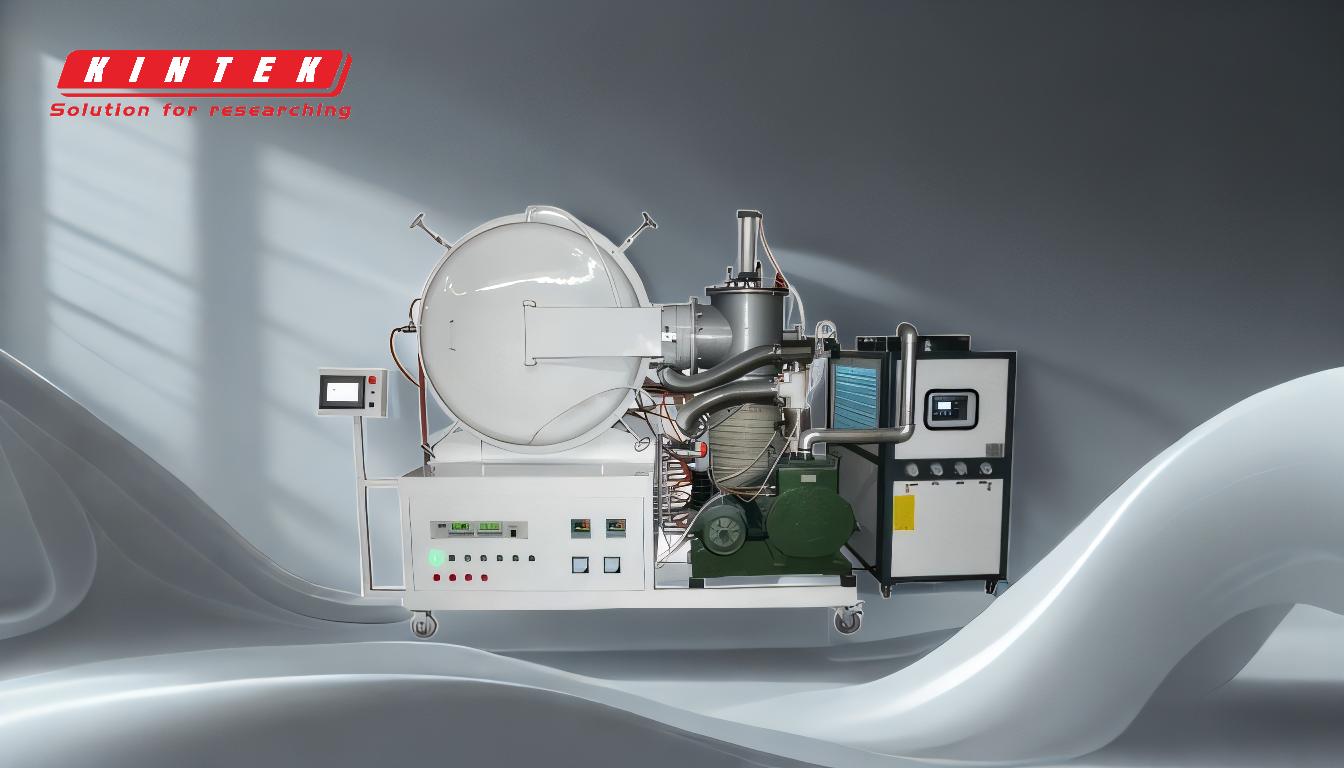
-
High Initial Investment and Operating Costs:
- Initial Costs: Core type induction heating systems require significant upfront investment. This includes the cost of specialized equipment, power supplies, and inductors tailored to specific applications.
- Operating Costs: Operating these systems necessitates skilled personnel who are well-versed in induction heating principles and safety procedures. This adds to the overall cost of operation.
-
Specialized Equipment and Engineering:
- Dedicated Inductors: The need to produce dedicated inductors for various applications can be expensive and time-consuming. Each inductor must be precisely designed to match the specific requirements of the application.
- Copper-Fitting: Managing high-current densities in small copper inductors often requires specialized engineering and 'copper-fitting,' which can further increase costs and complexity.
-
Lack of Refining Capacity:
- Material Purity: Induction furnaces lack the refining capacity found in other types of furnaces. Charge materials must be free of oxides and of a known composition to ensure quality.
- Alloying Elements: Some alloying elements may be lost due to oxidation during the heating process, necessitating their re-addition to the melt. This can complicate the process and increase material costs.
-
Challenges in Control and Optimization:
- Robust Control Algorithms: Proper operation of power converters for different induction heating loads and operating points requires robust control algorithms. This is particularly challenging in multi-coil systems.
- Real-Time Identification and Adaptive Algorithms: Improved performance and optimization of transient processes can be achieved through real-time identification control units with adaptive algorithms. However, implementing these advanced control systems adds to the complexity and cost.
-
Limitations in Heating Applications:
- Surface Heating: Induction heating is most effective for surface heating, which may limit its application in processes requiring uniform or deep heating. This can be a significant drawback for certain heat treatment processes.
In summary, while core type induction heating offers many advantages, such as efficiency and precision, it also presents several challenges. These include high initial and operating costs, the need for specialized equipment and skilled personnel, limitations in refining capacity, and challenges in control and optimization. Additionally, its effectiveness is primarily limited to surface heating, which may restrict its use in certain applications. Understanding these disadvantages is crucial for making informed decisions about the suitability of core type induction heating for specific industrial processes.
Summary Table:
Disadvantage | Details |
---|---|
High Initial and Operating Costs | Significant upfront investment and skilled personnel required. |
Specialized Equipment Needs | Dedicated inductors and copper-fitting increase complexity and cost. |
Lack of Refining Capacity | Materials must be oxide-free, and alloying elements may be lost. |
Control and Optimization Issues | Robust algorithms and adaptive systems add to complexity and expense. |
Surface Heating Limitations | Primarily effective for surface heating, not uniform or deep heating. |
Need help deciding if core type induction heating is right for your application? Contact our experts today for tailored advice!