Electric Arc Furnaces (EAFs) are widely used in steel production due to their efficiency, flexibility, and ability to recycle scrap metal. However, they also come with several disadvantages that can impact their operation, cost, and the quality of the final product. Key drawbacks include high energy consumption, difficulty in controlling chemical composition when using 100% scrap, contamination risks, operational challenges, and limitations in alloy production. These factors must be carefully considered when evaluating the suitability of EAFs for specific steelmaking applications.
Key Points Explained:
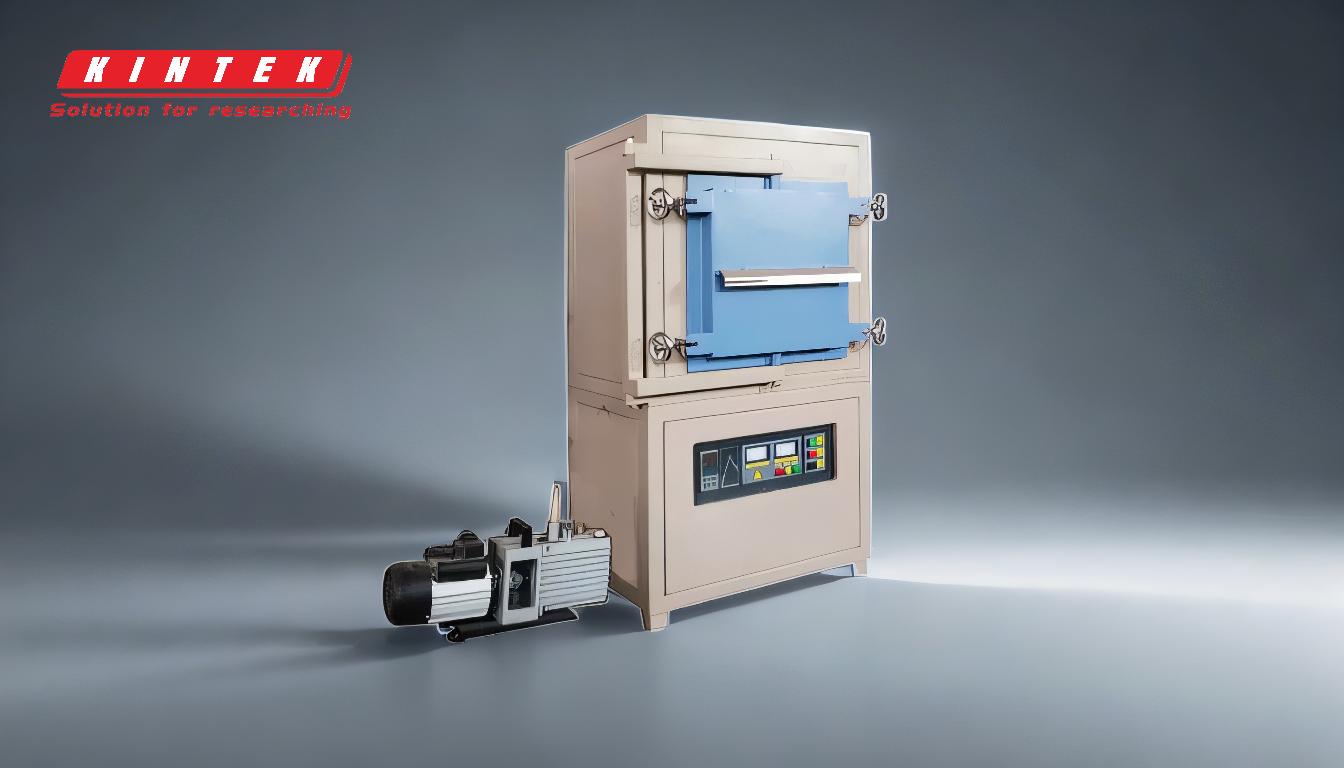
-
High Energy Consumption
- EAFs require a significant amount of electrical power to operate, which can strain local electrical grids and increase operational costs.
- The reliance on electricity makes EAFs vulnerable to power outages or fluctuations, which can disrupt production and lead to downtime.
- High energy consumption also contributes to a larger carbon footprint if the electricity is generated from non-renewable sources.
-
Difficulty in Controlling Chemical Composition
- While EAFs offer flexibility in controlling the chemical composition of steel, this becomes challenging when using 100% scrap material.
- Scrap metal often contains impurities or unknown alloying elements, which can lead to inconsistencies in the final product.
- Achieving precise chemical composition requires careful monitoring and adjustments, which can increase complexity and cost.
-
Risk of Contamination
- In non-self-consuming electrode EAFs, the molten metal can be contaminated by the electrode material, although this is usually localized and rare.
- Contamination can affect the quality and properties of the steel, making it unsuitable for certain high-precision applications.
-
Operational Challenges
- Non-self-consuming arc furnaces often face stability issues, making them difficult to operate, especially under vacuum conditions.
- The process requires forming a molten pool before degassing, which adds to the complexity and time required for production.
- Tap-to-tap times (the time between successive batches) typically range from 50 to 80 minutes, depending on transformer power and vessel size, which can limit throughput.
-
Limitations in Alloy Production
- Non-self-consuming EAFs are typically limited to small-scale alloy production, with batch sizes ranging from dozens to hundreds of grams.
- Controlling the proportion of alloy composition is difficult, and achieving consistent results can be challenging.
- This limitation makes EAFs less suitable for applications requiring large quantities of high-precision alloys.
-
Economic and Environmental Considerations
- While EAFs are more energy-efficient than blast furnaces, their high electricity consumption can offset some of these savings, especially in regions with expensive or unreliable power.
- The reliance on scrap metal, while environmentally beneficial, can also introduce variability in raw material quality, leading to potential inefficiencies.
In summary, while EAFs offer significant advantages in terms of efficiency, flexibility, and environmental benefits, they also present several challenges. These include high energy consumption, difficulty in controlling chemical composition, contamination risks, operational complexities, and limitations in alloy production. These factors must be carefully weighed when deciding whether to use EAFs for specific steelmaking needs.
Summary Table:
Disadvantage | Key Details |
---|---|
High Energy Consumption | - Strains local grids, increases costs, and contributes to carbon footprint. |
Chemical Composition Control | - Difficult with 100% scrap; impurities lead to inconsistencies and higher costs. |
Contamination Risks | - Molten metal may be contaminated by electrode material, affecting quality. |
Operational Challenges | - Stability issues, complex degassing process, and longer tap-to-tap times. |
Alloy Production Limitations | - Limited to small-scale production; difficulty in achieving consistent alloy composition. |
Economic & Environmental Impact | - High electricity costs and variability in scrap quality can offset efficiency benefits. |
Considering Electric Arc Furnaces for your steelmaking needs? Contact our experts today to discuss the best solutions for your operations!