Hardening is a process used to increase the hardness and strength of materials, typically metals, through heat treatment or other methods. While it offers significant advantages, such as improved wear resistance and durability, it also comes with several disadvantages. These include increased brittleness, reduced ductility, potential for cracking, and limitations in material selection. Additionally, the process can be costly, time-consuming, and may introduce residual stresses that affect the material's performance. Understanding these drawbacks is crucial for making informed decisions in material selection and application.
Key Points Explained:
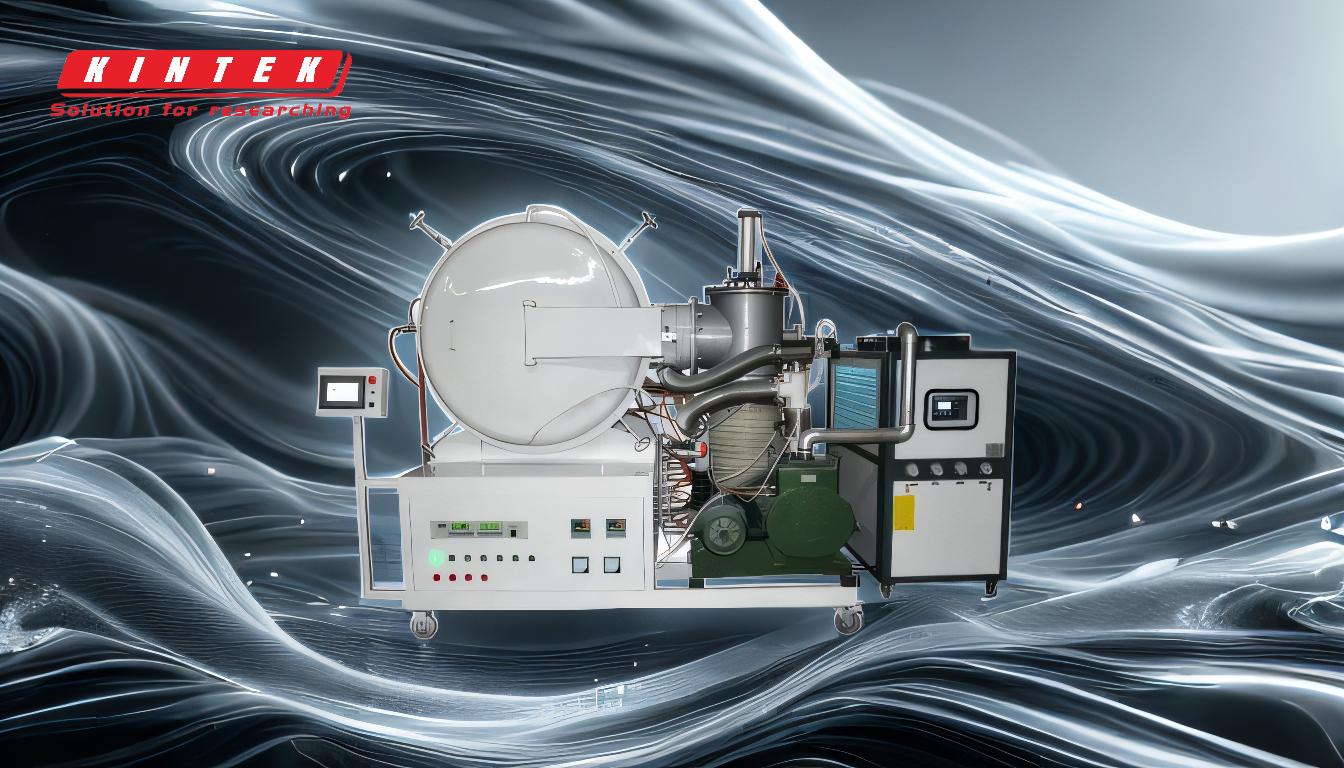
-
Increased Brittleness:
- Hardening often leads to a significant increase in brittleness, making the material more prone to sudden failure under impact or stress.
- This is particularly problematic in applications where the material is subjected to dynamic loads or shock.
-
Reduced Ductility:
- The process of hardening typically reduces the ductility of the material, meaning it becomes less capable of undergoing plastic deformation without breaking.
- This reduction in ductility can limit the material's ability to absorb energy, making it unsuitable for applications requiring flexibility.
-
Potential for Cracking:
- During the hardening process, especially in rapid cooling methods like quenching, there is a high risk of cracking due to thermal stresses.
- Cracks can compromise the structural integrity of the material, leading to premature failure.
-
Residual Stresses:
- Hardening can introduce residual stresses within the material, which can lead to distortion or warping.
- These stresses may also reduce the fatigue life of the material, making it more susceptible to failure under cyclic loading.
-
Material Limitations:
- Not all materials are suitable for hardening. Some alloys and metals may not respond well to the process, limiting the range of materials that can be effectively hardened.
- This can restrict design options and necessitate the use of alternative materials or treatments.
-
Cost and Time Considerations:
- The hardening process can be expensive, requiring specialized equipment and controlled environments.
- It is also time-consuming, which can increase production lead times and overall costs.
-
Surface Hardness vs. Core Properties:
- Hardening often results in a surface that is much harder than the core of the material. This discrepancy can lead to issues such as delamination or spalling under certain conditions.
- Balancing surface hardness with core properties is a critical consideration in the design and application of hardened materials.
-
Environmental and Safety Concerns:
- The hardening process, particularly those involving high temperatures and chemical treatments, can pose environmental and safety risks.
- Proper handling and disposal of chemicals, as well as adherence to safety protocols, are essential to mitigate these risks.
In summary, while hardening offers significant benefits in terms of material strength and wear resistance, it is essential to carefully consider its disadvantages. These include increased brittleness, reduced ductility, potential for cracking, residual stresses, material limitations, cost and time considerations, surface-core property discrepancies, and environmental and safety concerns. Understanding these drawbacks allows for better decision-making in material selection and application, ensuring that the benefits of hardening are maximized while minimizing its negative impacts.
Summary Table:
Disadvantage | Description |
---|---|
Increased Brittleness | Higher risk of sudden failure under stress or impact. |
Reduced Ductility | Decreased ability to deform without breaking, limiting flexibility. |
Potential for Cracking | High risk of cracks due to thermal stresses during rapid cooling. |
Residual Stresses | Introduces internal stresses, leading to distortion or reduced fatigue life. |
Material Limitations | Not all materials can be hardened, restricting design options. |
Cost and Time Considerations | Expensive and time-consuming process requiring specialized equipment. |
Surface-Core Discrepancy | Harder surface compared to the core, risking delamination or spalling. |
Environmental and Safety Risks | High temperatures and chemicals pose safety and environmental concerns. |
Need help selecting the right material or process? Contact our experts today for tailored solutions!