Pressing and sintering are widely used in manufacturing processes, particularly for ceramics and metals, but they come with several disadvantages. These include variations in part strength due to process inconsistencies, challenges in controlling the sintering environment, and limitations in material composition and furnace design. Additionally, the process can be time-consuming, and improper control of parameters like temperature, pressure, and atmosphere can lead to defects such as sooting, retained austenite, or uneven densification. While sintering furnaces, such as sintering furnace, offer benefits like complex shape production and improved mechanical properties, the drawbacks must be carefully managed to ensure reliable and high-quality outputs.
Key Points Explained:
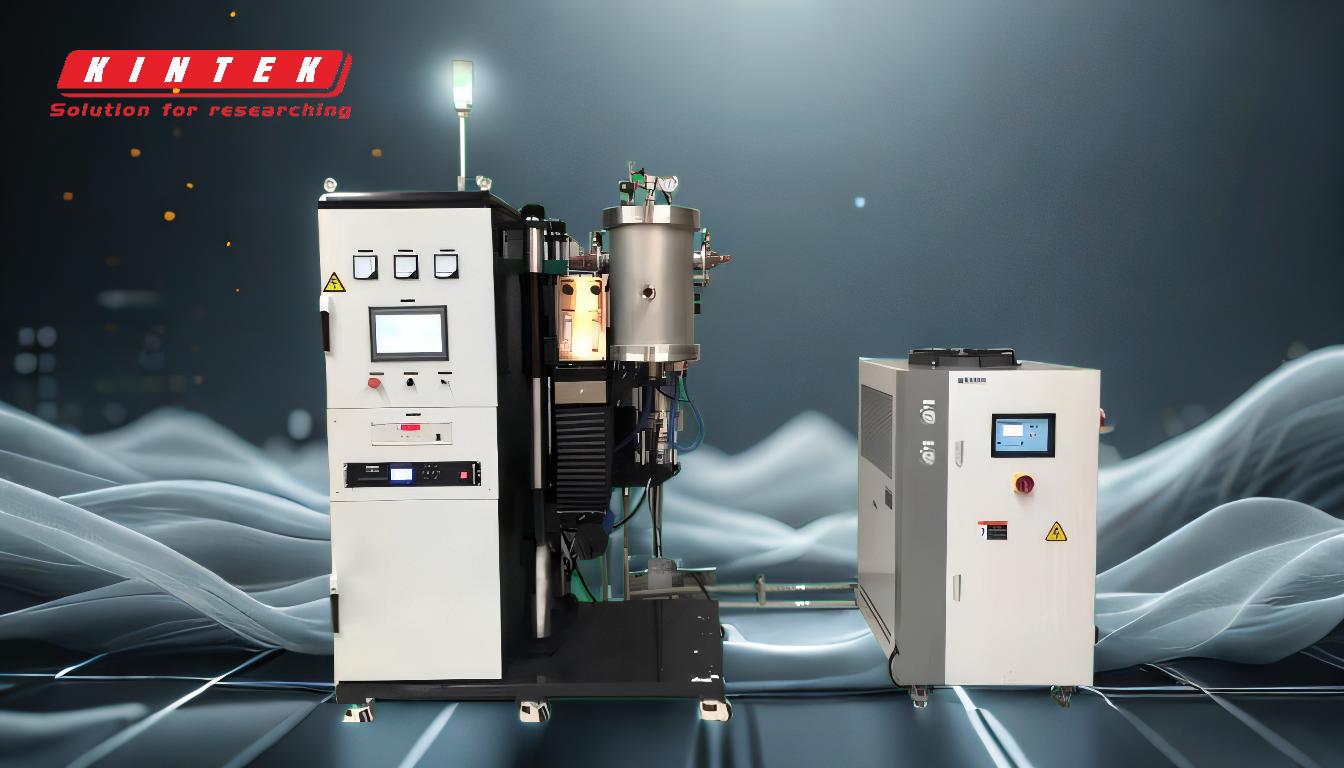
-
Variability in Part Strength and Quality:
- The sintering process can result in weak and inconsistent parts due to variations in temperature, pressure, and material composition. This variability compromises the strength and reliability of the final product, making it unsuitable for applications requiring high precision or durability.
-
Challenges in Controlling the Sintering Environment:
- Maintaining a consistent environment in a sintering furnace is critical but challenging. Improper control of the atmosphere, such as excessive carbon content, can lead to sooting, which overloads the furnace refractory and increases the risk of defects like retained austenite. This makes it difficult to achieve uniform material properties.
-
Time-Consuming Process:
- Sintering, especially in furnaces like muffle furnaces, can take a long time to reach the desired temperature. This makes the process less efficient for projects requiring quick turnarounds. Additionally, the design of some furnaces, such as muffle furnaces, limits accessibility, complicating material placement and handling.
-
Material Composition Limitations:
- The sintering process requires precise control over material composition. For instance, induction furnaces lack refining capacity, meaning charge materials must be free of oxides and of known composition. Alloying elements may be lost due to oxidation, requiring re-addition, which complicates the process and increases costs.
-
Unbalanced Densification and Shrinkage:
- Hot press sintering involves an unbalanced process where powders with crystal defects achieve greater density due to activated hot pressing. However, this can lead to uneven shrinkage and densification, resulting in parts with inconsistent dimensions and properties.
-
Furnace Design Limitations:
- While sintering furnaces like hot press sintering furnaces offer benefits such as short sintering times and excellent product performance, their design can limit accessibility and complicate maintenance. For example, the closed environment, while preventing oxidation and pollution, makes it harder to monitor and adjust the process in real-time.
-
Risk of Oxidation and Contamination:
- Despite the closed environment of some sintering furnaces, improper control of parameters like temperature and pressure can still lead to oxidation or contamination. This can degrade material properties and reduce the overall quality of the final product.
By understanding these disadvantages, manufacturers can take steps to mitigate risks, such as optimizing process parameters, using advanced furnace designs, and ensuring precise control over material composition and sintering conditions.
Summary Table:
Disadvantage | Key Details |
---|---|
Variability in Part Strength and Quality | Inconsistent parts due to temperature, pressure, and material composition variations. |
Challenges in Controlling Environment | Sooting, retained austenite, and uneven material properties due to improper control. |
Time-Consuming Process | Long heating times and limited accessibility in furnace designs. |
Material Composition Limitations | Requires precise control; alloying elements may be lost due to oxidation. |
Unbalanced Densification and Shrinkage | Uneven shrinkage and densification lead to inconsistent dimensions. |
Furnace Design Limitations | Closed environments complicate monitoring, maintenance, and real-time adjustments. |
Risk of Oxidation and Contamination | Improper control of parameters can degrade material properties. |
Learn how to overcome sintering challenges—contact our experts today for tailored solutions!