The tempering process, while essential for improving the mechanical properties of metals, has several disadvantages. These include the potential for reduced hardness and wear resistance, increased brittleness if not properly controlled, and the risk of distortion or cracking due to thermal stresses. Additionally, tempering requires precise temperature control and can be time-consuming, making it less efficient for high-volume production. The process may also introduce surface oxidation or decarburization, affecting the material's surface quality. Despite these drawbacks, tempering remains a critical step in achieving the desired balance between hardness and toughness in many industrial applications.
Key Points Explained:
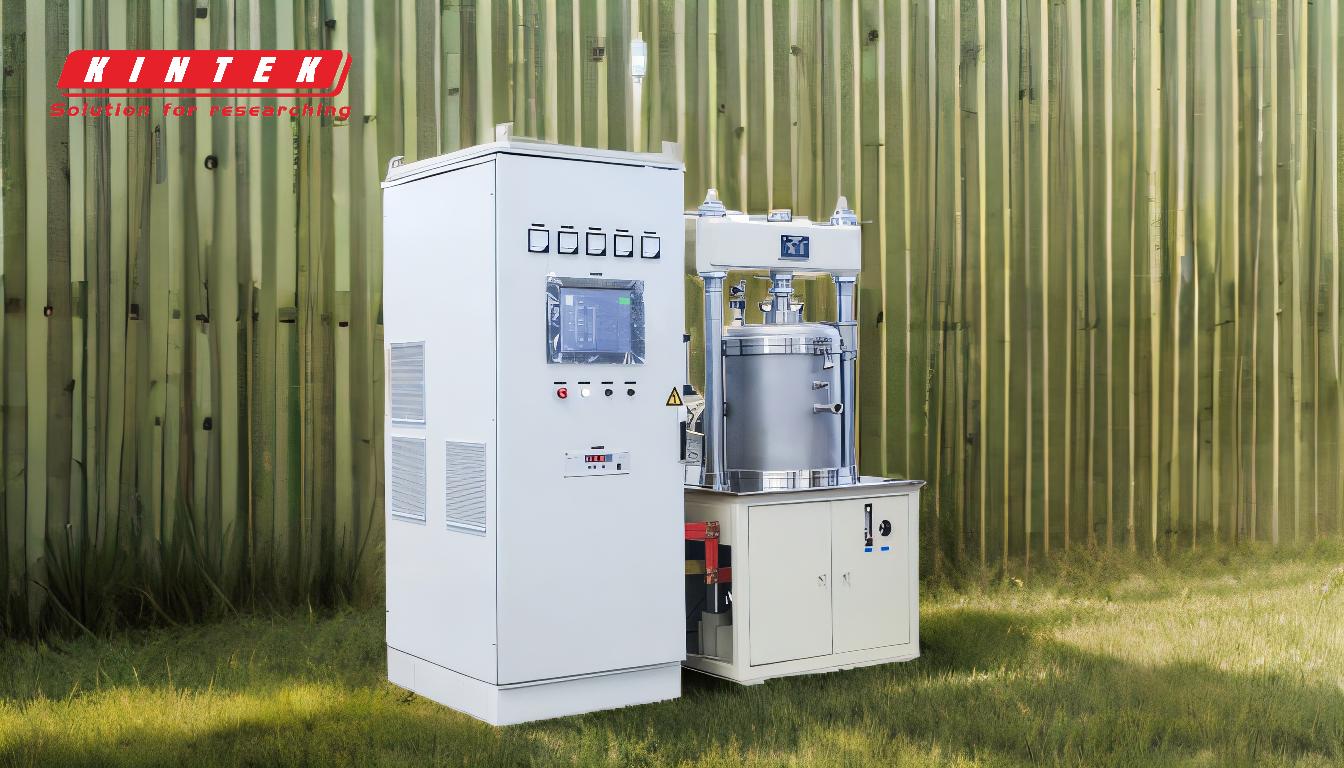
-
Reduction in Hardness and Wear Resistance
- Tempering involves heating the metal to a specific temperature below its critical point and then cooling it. This process reduces the hardness achieved during quenching, as the microstructure transitions from martensite to tempered martensite or other softer phases.
- While this reduction in hardness improves toughness, it can be a disadvantage for applications requiring high wear resistance or surface hardness.
-
Risk of Increased Brittleness
- If tempering is not performed at the correct temperature or for the appropriate duration, the material may become overly brittle. This is particularly problematic for high-carbon steels, where improper tempering can lead to catastrophic failure under stress.
- Brittleness can also result from temper embrittlement, a phenomenon that occurs when certain steels are tempered in specific temperature ranges, leading to reduced impact strength.
-
Thermal Stresses and Distortion
- The tempering process involves heating and cooling cycles, which can introduce thermal stresses in the material. These stresses may cause distortion, warping, or even cracking, especially in complex geometries or thin sections.
- Distortion can lead to dimensional inaccuracies, requiring additional machining or corrective measures, which increase production costs.
-
Surface Oxidation and Decarburization
- During tempering, exposure to air at elevated temperatures can cause surface oxidation, leading to the formation of scale or discoloration. This affects the material's surface finish and may require post-processing to restore the desired appearance.
- Decarburization, the loss of carbon from the surface layer, can also occur, reducing the hardness and strength of the material near the surface. This is particularly detrimental for components subjected to surface stresses.
-
Precision and Time Requirements
- Tempering requires precise control of temperature and time to achieve the desired mechanical properties. Variations in these parameters can lead to inconsistent results, affecting the performance of the final product.
- The process can be time-consuming, especially for large or thick components, as sufficient time is needed for the heat to penetrate uniformly. This can reduce production efficiency and increase costs.
-
Limited Applicability for High-Volume Production
- Due to the time and precision required, tempering may not be suitable for high-volume manufacturing processes where speed and efficiency are critical. Alternative heat treatment methods, such as induction hardening, may be preferred in such cases.
-
Environmental and Energy Considerations
- Tempering involves significant energy consumption, particularly for large-scale operations. This can lead to higher operational costs and a larger environmental footprint.
- Proper ventilation and safety measures are also required to manage the heat and fumes generated during the process, adding to the complexity and cost of implementation.
-
Material-Specific Limitations
- Not all materials respond well to tempering. For example, some stainless steels and non-ferrous alloys may not benefit significantly from tempering, or the process may introduce undesirable properties.
- The effectiveness of tempering also depends on the initial heat treatment (e.g., quenching) and the alloy composition, making it less versatile for certain applications.
In summary, while tempering is a valuable process for enhancing the mechanical properties of metals, it comes with several disadvantages, including reduced hardness, brittleness, distortion, and surface degradation. These challenges must be carefully managed to ensure the desired performance and quality of the final product.
Summary Table:
Disadvantage | Description |
---|---|
Reduced Hardness & Wear Resistance | Tempering reduces hardness, impacting wear resistance and surface hardness. |
Risk of Increased Brittleness | Improper tempering can lead to brittleness and catastrophic failure. |
Thermal Stresses & Distortion | Heating and cooling cycles may cause distortion, warping, or cracking. |
Surface Oxidation & Decarburization | Exposure to air can cause oxidation and carbon loss, affecting surface quality. |
Precision & Time Requirements | Requires precise temperature control and can be time-consuming. |
Limited High-Volume Applicability | Less efficient for high-volume production due to time and precision needs. |
Environmental & Energy Concerns | High energy consumption and environmental impact in large-scale operations. |
Material-Specific Limitations | Not all materials benefit from tempering, and effectiveness varies by alloy. |
Need help optimizing your tempering process? Contact our experts today for tailored solutions!