Vacuum heat treatment is a highly advanced process that offers numerous advantages, such as no oxidation, decarburization, or carburization, as well as surface purification and brightness. However, despite its benefits, there are several disadvantages associated with this method. These include high initial costs, complex equipment requirements, limited suitability for certain materials, and challenges in scaling up for large-scale production. Additionally, the process may require specialized expertise and longer cycle times compared to conventional heat treatment methods. Below, we explore these disadvantages in detail to provide a comprehensive understanding of the limitations of vacuum heat treatment.
Key Points Explained:
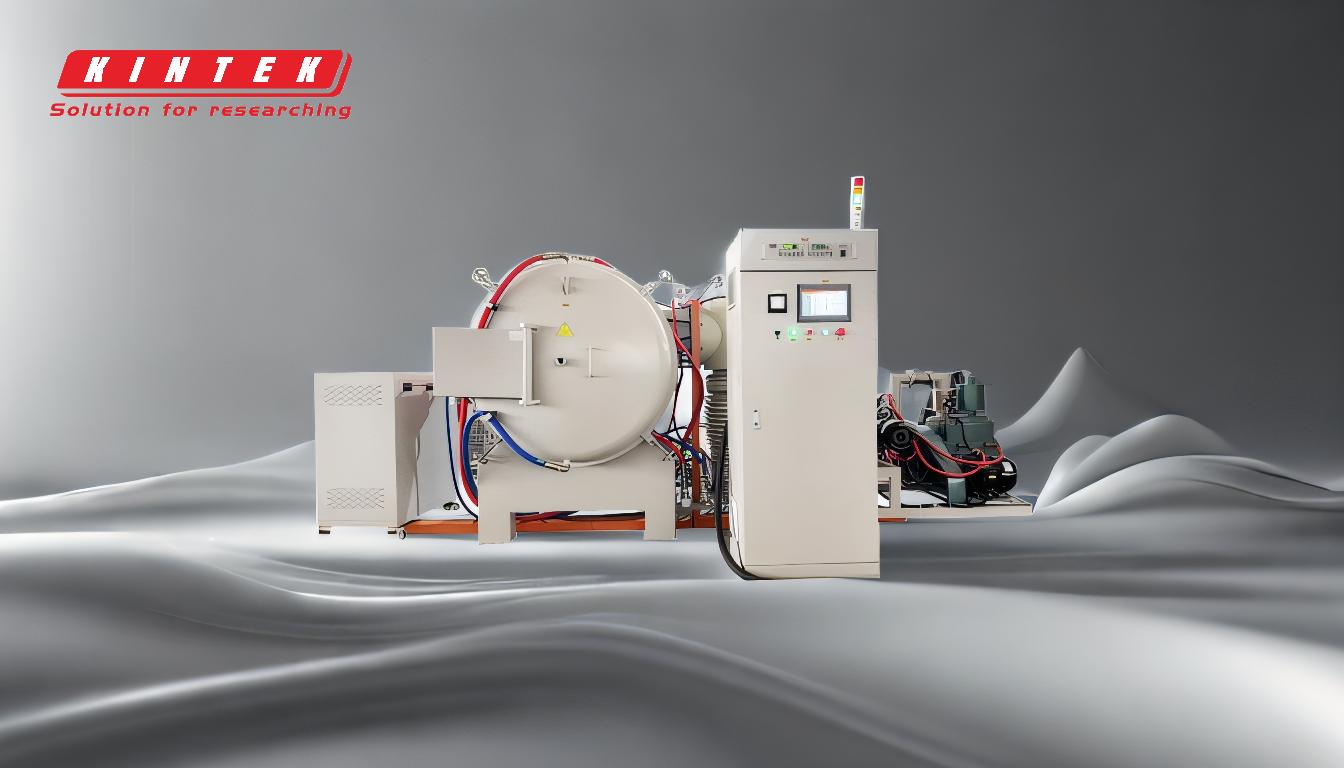
-
High Initial Costs
- Vacuum heat treatment requires specialized equipment, such as vacuum furnaces, which are significantly more expensive than conventional heat treatment furnaces.
- The cost of maintaining a vacuum environment, including pumps and seals, adds to the overall expense.
- For small-scale operations or businesses with limited budgets, the high upfront investment can be a significant barrier.
-
Complex Equipment and Maintenance
- The equipment used in vacuum heat treatment is highly sophisticated and requires regular maintenance to ensure optimal performance.
- Components like vacuum pumps, heating elements, and cooling systems are prone to wear and tear, necessitating frequent inspections and replacements.
- The complexity of the equipment also demands skilled technicians, increasing operational costs.
-
Limited Suitability for Certain Materials
- While vacuum heat treatment is ideal for materials that are sensitive to oxidation or decarburization, it may not be suitable for all types of metals or alloys.
- Some materials may require specific atmospheres or cooling rates that are difficult to achieve in a vacuum environment.
- For example, certain steels or alloys might not achieve the desired mechanical properties under vacuum conditions.
-
Challenges in Scaling Up for Large-Scale Production
- Vacuum heat treatment is often more suitable for small batches or precision components due to the limitations of vacuum furnace sizes.
- Scaling up the process for large-scale production can be challenging, as it requires larger furnaces and more sophisticated control systems.
- The longer cycle times associated with vacuum heat treatment can also hinder productivity in high-volume manufacturing settings.
-
Specialized Expertise Required
- Operating vacuum heat treatment equipment requires specialized knowledge and training.
- The process involves precise control of parameters such as temperature, vacuum degree, and cooling rates, which demands a high level of expertise.
- A lack of skilled personnel can lead to inconsistent results or equipment damage.
-
Longer Cycle Times
- Compared to conventional heat treatment methods, vacuum heat treatment often involves longer heating and cooling cycles.
- The need to achieve and maintain a high vacuum level, as well as the slower cooling rates in a vacuum environment, contribute to extended processing times.
- This can be a disadvantage in industries where rapid turnaround times are critical.
-
Energy Consumption
- While vacuum heat treatment is generally energy-efficient, the process of creating and maintaining a vacuum requires significant energy input.
- The energy consumption of vacuum pumps and other auxiliary systems can offset some of the environmental benefits of the process.
-
Potential for Surface Contamination
- Although vacuum heat treatment is designed to prevent oxidation and contamination, improper handling or equipment malfunctions can lead to surface contamination.
- For example, residual gases or impurities in the vacuum chamber can affect the quality of the treated components.
In conclusion, while vacuum heat treatment offers numerous advantages, such as enhanced surface quality and precise control over heat treatment parameters, it also comes with several disadvantages. These include high costs, complex equipment, limited material suitability, scalability challenges, and the need for specialized expertise. Understanding these limitations is crucial for making informed decisions about whether vacuum heat treatment is the right choice for a specific application.
Summary Table:
Disadvantage | Key Details |
---|---|
High Initial Costs | Expensive equipment and maintenance costs, challenging for small-scale operations. |
Complex Equipment and Maintenance | Requires skilled technicians and frequent upkeep for optimal performance. |
Limited Suitability for Materials | Not ideal for all metals or alloys; specific conditions may be hard to achieve. |
Scaling Up Challenges | Difficult to adapt for large-scale production due to furnace size and cycle times. |
Specialized Expertise Required | Demands precise control of parameters and skilled personnel. |
Longer Cycle Times | Slower heating and cooling compared to conventional methods. |
Energy Consumption | High energy use for vacuum pumps and auxiliary systems. |
Potential Surface Contamination | Risk of contamination due to residual gases or equipment malfunctions. |
Need help deciding if vacuum heat treatment is right for your application? Contact our experts today for personalized advice!