Metal foam, while offering unique properties such as lightweight structure and high porosity, has several downsides that limit its widespread adoption. The primary disadvantages include its high cost, which restricts its use to high-end applications, and insufficient characterization of its long-term resistance to fouling, corrosion, and erosion. These limitations pose challenges for industries seeking durable and cost-effective materials.
Key Points Explained:
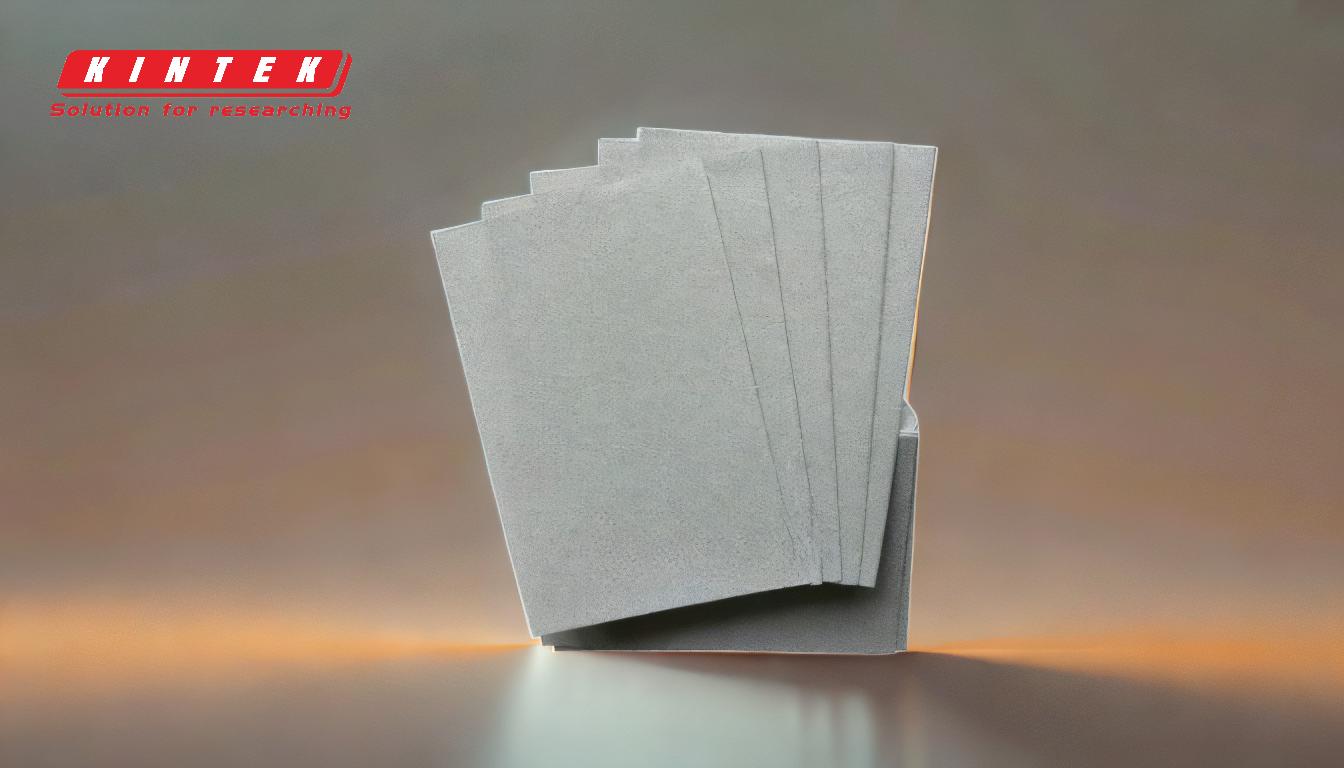
-
High Cost of Metal Foam
- Metal foam is expensive to produce due to the complex manufacturing processes involved, such as powder metallurgy, gas injection, or sintering. These methods require specialized equipment and materials, driving up production costs.
- The high cost limits its use to niche or high-end applications, such as aerospace, automotive, and advanced thermal management systems, where its unique properties justify the expense.
- For industries with budget constraints, the cost of metal foam may outweigh its benefits, making it less attractive compared to traditional materials like solid metals or composites.
-
Insufficient Characterization of Long-Term Resistance
- Fouling: Metal foam's porous structure makes it susceptible to fouling, where particulate matter or biological growth accumulates in the pores. This can reduce its effectiveness in applications like filtration or heat exchange.
- Corrosion: While some metal foams are made from corrosion-resistant alloys, their long-term performance in corrosive environments is not well-documented. The porous nature may expose more surface area to corrosive agents, accelerating degradation.
- Erosion: In high-velocity or abrasive environments, the foam's structure may erode over time, compromising its mechanical integrity and performance.
-
Limited Mechanical Strength
- Metal foam typically has lower mechanical strength compared to solid metals due to its porous structure. This limits its use in load-bearing applications where high strength and durability are required.
- The trade-off between lightweight properties and strength must be carefully considered when selecting metal foam for specific applications.
-
Challenges in Manufacturing and Quality Control
- Producing metal foam with consistent properties (e.g., pore size, density, and distribution) is challenging. Variability in manufacturing can lead to inconsistent performance.
- Quality control is more complex compared to solid metals, as defects in the foam structure may not be easily detectable.
-
Limited Availability and Standardization
- Metal foam is not as widely available as traditional materials, and there is a lack of standardized specifications for its properties and performance. This makes it difficult for engineers and designers to incorporate it into their projects with confidence.
-
Potential Solutions and Future Directions
- Cost Reduction: Advances in manufacturing technologies, such as additive manufacturing (3D printing), could potentially reduce the cost of producing metal foam by streamlining the process and minimizing material waste.
- Improved Characterization: Further research and testing are needed to better understand the long-term behavior of metal foam in various environments. This would help establish reliable performance metrics and expand its applicability.
- Hybrid Materials: Combining metal foam with other materials, such as coatings or composites, could enhance its resistance to fouling, corrosion, and erosion while maintaining its lightweight properties.
In conclusion, while metal foam offers unique advantages, its high cost, insufficient long-term performance data, and manufacturing challenges are significant downsides. Addressing these limitations through technological advancements and further research could unlock its potential for broader applications.
Summary Table:
Disadvantage | Details |
---|---|
High Cost | Expensive manufacturing processes limit use to high-end applications. |
Insufficient Long-Term Resistance | Poorly characterized resistance to fouling, corrosion, and erosion. |
Limited Mechanical Strength | Lower strength compared to solid metals, unsuitable for load-bearing uses. |
Manufacturing Challenges | Inconsistent properties and complex quality control. |
Limited Availability | Lack of standardization and widespread availability. |
Potential Solutions | Cost reduction, improved research, and hybrid materials for better performance. |
Interested in overcoming the limitations of metal foam? Contact our experts today to explore innovative solutions!