Heat treatment is a critical process in metallurgy, where the properties of metals are altered by controlled heating and cooling. The essential controllable parameters in a heat treatment process include temperature, time, cooling rate, furnace atmosphere, humidity, pressure, and uniformity of temperature distribution. These parameters must be carefully monitored and adjusted based on the material type, desired properties, and specific application requirements. By controlling these factors, manufacturers can achieve precise and repeatable results, ensuring improved product quality, consistency, and performance. Below, the key parameters are explained in detail, along with their significance in the heat treatment process.
Key Points Explained:
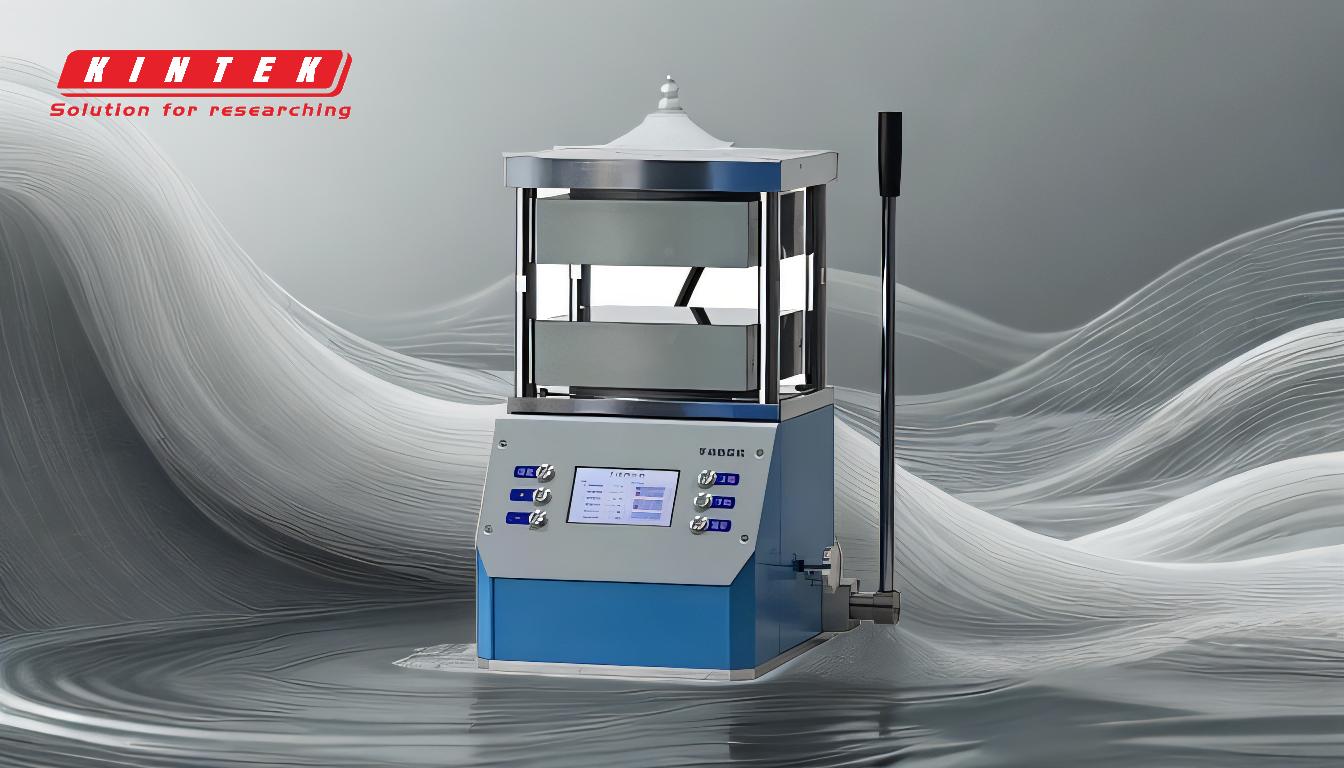
-
Temperature
- Temperature is the most critical parameter in heat treatment, as it directly influences the material's microstructure and properties.
- The temperature must be carefully controlled within tight tolerances to achieve the desired metallurgical transformation, such as hardening, annealing, or tempering.
- Heat-up and cool-down rates are also important to avoid thermal stress, cracking, or distortion in the material.
- The maximum temperature must be restricted to prevent overheating, which can lead to grain growth or other undesirable effects.
-
Time
- The duration for which the material is held at the target temperature (soak time) is crucial for achieving uniform heating and the desired transformation.
- Insufficient time can result in incomplete transformation, while excessive time can lead to over-aging or grain coarsening.
- Cycle times must be optimized to minimize process time without compromising metallurgical quality.
-
Cooling Rate
- The method and rate of cooling determine the final microstructure and properties of the material.
- Rapid cooling (quenching) is used to harden materials, while slower cooling rates are employed for processes like annealing or normalizing.
- The cooling medium (e.g., air, oil, water) and its flow rate must be controlled to achieve the desired results.
-
Furnace Atmosphere
- The composition of the furnace atmosphere is critical for preventing oxidation, decarburization, or other surface reactions.
- Common atmospheres include inert gases (e.g., nitrogen, argon), reducing gases (e.g., hydrogen), or carburizing gases (e.g., methane).
- Maintaining the correct gas composition ensures consistent product quality and surface integrity.
-
Humidity
- Humidity levels in the furnace atmosphere must be controlled to prevent oxidation or decarburization of the metal components.
- High humidity can lead to unwanted surface reactions, while low humidity may cause excessive drying or cracking.
-
Pressure
- Pressure control is necessary to avoid excessive gas flow into the furnace, which can disrupt the atmosphere and affect the heat treatment process.
- Proper pressure regulation ensures stable and uniform heat transfer within the furnace.
-
Uniformity of Temperature Distribution
- Uniform temperature distribution throughout the furnace's hot zone is essential for consistent product quality.
- Hot spots or cold spots can lead to uneven transformation, resulting in parts with varying properties.
- Proper gas circulation and heat distribution mechanisms must be employed to achieve uniformity.
-
Gas Circulation
- Proper gas circulation ensures even heat transfer and uniform atmosphere composition throughout the furnace.
- Partial pressure or quench gas flow must be optimized to achieve the desired cooling rate and surface properties.
By carefully controlling these parameters, manufacturers can achieve precise and repeatable heat treatment results, ensuring that the final product meets the required specifications for strength, hardness, ductility, and other mechanical properties. Additionally, anticipating potential issues and maintaining tight control over these factors can reduce downtime, minimize maintenance, and improve overall process efficiency.
Summary Table:
Parameter | Significance |
---|---|
Temperature | Controls microstructure and properties; critical for hardening, annealing, etc. |
Time | Ensures uniform heating and desired transformation; avoids over-aging. |
Cooling Rate | Determines final microstructure; rapid cooling for hardening, slow for annealing. |
Furnace Atmosphere | Prevents oxidation, decarburization; uses inert, reducing, or carburizing gases. |
Humidity | Controls surface reactions; prevents oxidation or cracking. |
Pressure | Ensures stable heat transfer; avoids excessive gas flow. |
Uniformity of Temperature | Achieves consistent product quality; prevents hot or cold spots. |
Gas Circulation | Ensures even heat transfer and uniform atmosphere composition. |
Ready to optimize your heat treatment process? Contact our experts today for tailored solutions!