Compression molding, while a widely used manufacturing process for producing high-quality parts, has several limitations that can affect efficiency, cost, and product quality. These limitations include challenges in material preparation, potential defects due to improper stock placement, labor-intensive operations, and issues with flash removal. Understanding these limitations is crucial for equipment and consumable purchasers to make informed decisions and optimize their processes.
Key Points Explained:
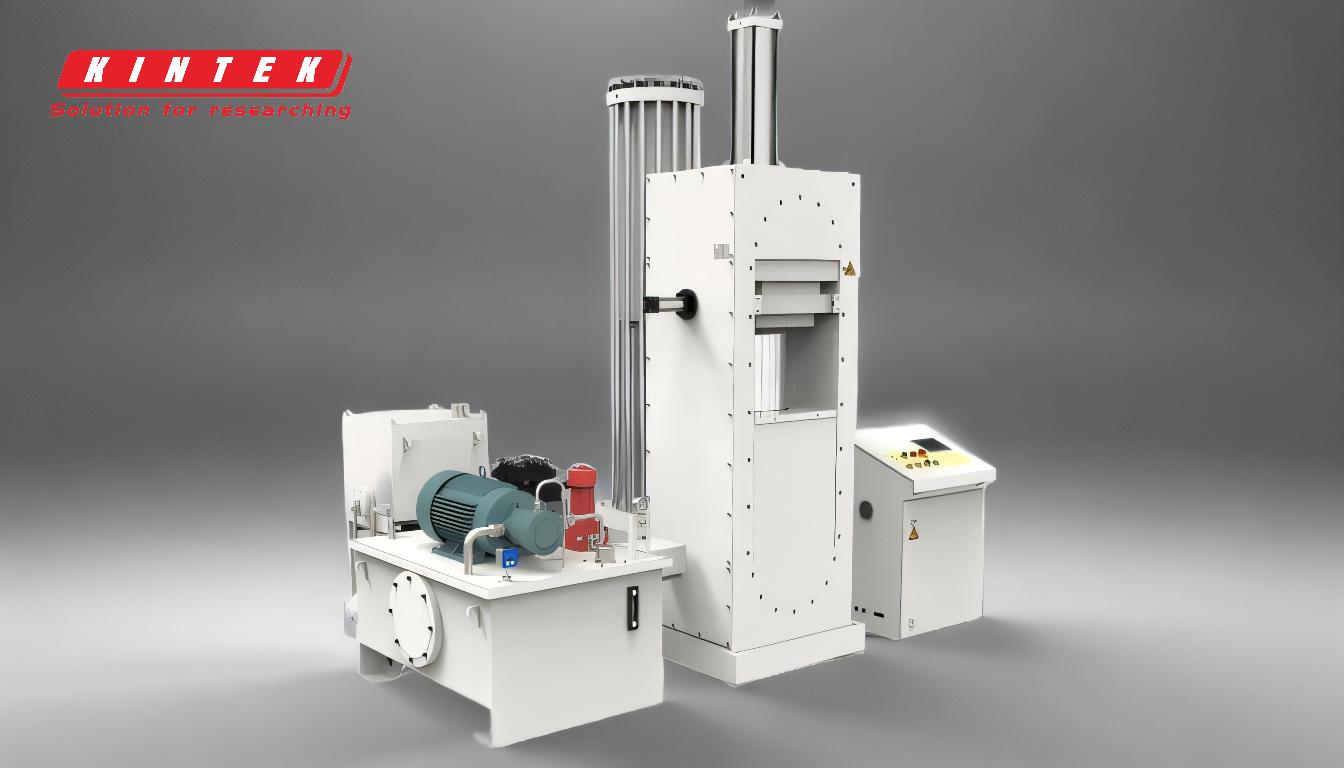
-
Material Preparation Challenges:
- Accurate Stock Measurement: One of the primary limitations of compression molding is the need for precise measurement of the material stock. The stock must be accurately cut or weighed to ensure that each mold cavity receives the correct amount of material. Inaccurate measurements can lead to defects in the final product.
- Impact on Product Quality: If too little material is used, it can result in defects such as flow lines, blisters, or unfilled parts. These defects not only compromise the structural integrity of the product but also increase the likelihood of product rejection during quality control checks.
-
Defects Due to Improper Stock Placement:
- Flow Lines and Blisters: Incorrect placement of the material stock within the mold can lead to flow lines and blisters. Flow lines are visible marks on the surface of the molded part, while blisters are raised areas caused by trapped air or gas. Both defects can significantly affect the aesthetic and functional quality of the product.
- Unfilled Parts: If the material does not fully fill the mold cavity, the resulting part may have incomplete or thin sections. This can lead to weak spots in the product, making it unsuitable for its intended application.
-
Labor-Intensive Process:
- Loading and Unloading: Compression molding requires manual loading and unloading of the mold, which can be labor-intensive. This increases the overall production time and labor costs, making the process less efficient compared to other molding techniques.
- Skill Requirement: The process demands skilled labor to ensure proper material placement and mold handling. The need for skilled workers can further increase operational costs and complicate the hiring process.
-
Flash Removal Issues:
- Excessive Rubber and Heavy Flash: Using too much material can result in heavy flash, which is the excess material that escapes from the mold cavity. Heavy flash is difficult to remove and can require additional post-processing steps, such as trimming or grinding, to achieve the desired final product dimensions.
- Impact on Production Efficiency: The need for additional flash removal steps can slow down the production process and increase costs. It also adds complexity to the workflow, requiring additional equipment and labor.
-
Economic and Operational Considerations:
- Cost Implications: The labor-intensive nature of compression molding, combined with the potential for material waste and defects, can lead to higher production costs. Equipment and consumable purchasers need to consider these factors when evaluating the overall cost-effectiveness of the process.
- Process Optimization: To mitigate some of these limitations, manufacturers may need to invest in advanced equipment, such as automated material handling systems, or adopt process optimization techniques to improve efficiency and reduce defects.
In summary, while compression molding is a versatile and effective manufacturing process, it comes with several limitations that can impact product quality, production efficiency, and costs. Equipment and consumable purchasers should carefully consider these factors and explore potential solutions, such as process optimization and automation, to overcome these challenges and achieve better outcomes in their manufacturing operations.
Summary Table:
Limitation | Key Challenges | Impact |
---|---|---|
Material Preparation | Accurate stock measurement required; too little material causes defects. | Poor product quality, increased rejection rates. |
Improper Stock Placement | Flow lines, blisters, and unfilled parts due to incorrect material placement. | Aesthetic and functional defects in final products. |
Labor-Intensive Process | Manual loading/unloading and skilled labor requirements. | Increased production time, higher labor costs. |
Flash Removal Issues | Heavy flash requires trimming/grinding, slowing production. | Added complexity, higher costs, and reduced efficiency. |
Economic Considerations | High costs due to labor, material waste, and defects. | Reduced cost-effectiveness; need for process optimization. |
Struggling with compression molding limitations? Contact our experts today to optimize your process and improve efficiency!