Brazing is a versatile joining process that involves heating a filler metal above its melting point and distributing it between two or more close-fitting parts by capillary action. The choice of heating method is crucial and depends on factors such as the materials being joined, joint geometry, production volume, and desired quality. Common methods include torch brazing, furnace brazing, induction brazing, dip brazing, resistance brazing, infrared brazing, and advanced techniques like laser and electron beam brazing. Each method has unique advantages and limitations, making it essential to select the most suitable approach based on the application's specific requirements.
Key Points Explained:
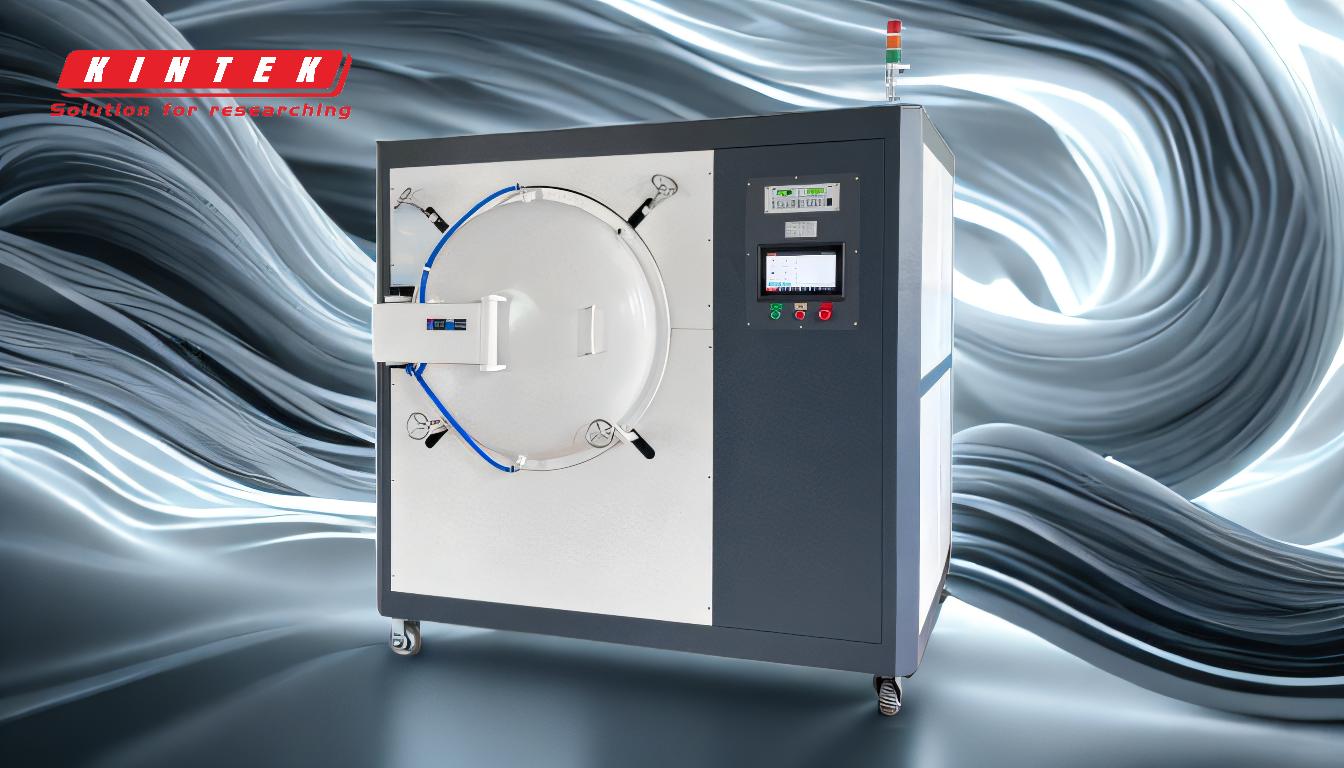
-
Torch Brazing:
- Torch brazing uses a flame produced by a gas torch to heat the joint and melt the filler metal. It is a manual process, often used for small-scale or repair work.
- Advantages: High flexibility, portability, and suitability for localized heating.
- Limitations: Requires skilled operators, and heat control can be challenging.
-
Furnace Brazing:
- Furnace brazing involves heating the entire assembly in a controlled environment, such as exothermic, hydrogen, argon, or vacuum atmospheres.
- Advantages: Uniform heating, high production rates, and excellent joint quality.
- Limitations: High equipment costs and limited flexibility for large or complex parts.
-
Induction Brazing:
- Induction brazing uses electromagnetic induction to generate heat directly in the workpiece, making it highly efficient for localized heating.
- Advantages: Rapid heating, precise control, and suitability for high-volume production.
- Limitations: Requires conductive materials and specialized equipment.
-
Dip Brazing:
- Dip brazing involves immersing the assembly in a molten salt or metal bath to achieve uniform heating.
- Advantages: Excellent heat transfer and suitability for complex geometries.
- Limitations: Limited to specific materials and requires post-brazing cleaning.
-
Resistance Brazing:
- Resistance brazing uses electrical resistance to generate heat at the joint interface, often with electrodes.
- Advantages: Fast heating and precise control over the joint area.
- Limitations: Limited to small parts and requires conductive materials.
-
Infrared Brazing:
- Infrared brazing uses focused infrared radiation to heat the joint, providing a non-contact heating method.
- Advantages: Clean process with minimal contamination and precise heat control.
- Limitations: Limited penetration depth and requires reflective surfaces.
-
Advanced Techniques (Laser and Electron Beam Brazing):
- Laser and electron beam brazing use highly focused energy sources for precise and localized heating.
- Advantages: High precision, minimal heat-affected zones, and suitability for delicate or complex parts.
- Limitations: High equipment costs and specialized setup requirements.
-
Factors Influencing Heating Method Selection:
- Heat Transfer Efficiency: Ensures uniform heating and proper filler metal flow.
- Heat Capacity of Base Metals: Prevents overheating or damage to the materials.
- Joint Geometry: Determines the accessibility and heating method required.
- Production Rate and Volume: Influences the choice between manual and automated methods.
-
Distortion Prevention in Brazing:
- Distortion is a common challenge in brazing, especially in vacuum brazing. Methods to minimize distortion include:
- Stress relieving parts before brazing.
- Using rigid fixtures to hold parts in place during heating.
- Designing heavier or larger parts to resist deformation.
- Despite these measures, some distortion may still occur due to thermal expansion and contraction.
- Distortion is a common challenge in brazing, especially in vacuum brazing. Methods to minimize distortion include:
By understanding these methods and their respective advantages and limitations, manufacturers can select the most appropriate brazing heating technique for their specific application, ensuring high-quality joints and efficient production processes.
Summary Table:
Method | Advantages | Limitations |
---|---|---|
Torch Brazing | High flexibility, portable, suitable for localized heating | Requires skilled operators, challenging heat control |
Furnace Brazing | Uniform heating, high production rates, excellent joint quality | High equipment costs, limited flexibility for large or complex parts |
Induction Brazing | Rapid heating, precise control, suitable for high-volume production | Requires conductive materials, specialized equipment |
Dip Brazing | Excellent heat transfer, suitable for complex geometries | Limited to specific materials, requires post-brazing cleaning |
Resistance Brazing | Fast heating, precise control over joint area | Limited to small parts, requires conductive materials |
Infrared Brazing | Clean process, minimal contamination, precise heat control | Limited penetration depth, requires reflective surfaces |
Advanced Techniques | High precision, minimal heat-affected zones, suitable for delicate/complex parts | High equipment costs, specialized setup requirements |
Need help selecting the right brazing heating method for your project? Contact our experts today!