Graphene, a single layer of carbon atoms arranged in a hexagonal lattice, is prepared using various methods, each with its own advantages and limitations. The primary methods include mechanical exfoliation, liquid-phase exfoliation, reduction of graphene oxide (GO), and chemical vapor deposition (CVD). Mechanical exfoliation is ideal for fundamental research but not scalable, while liquid-phase exfoliation is suitable for mass production but yields graphene with lower electrical quality. Reduction of GO is cost-effective but often results in graphene with defects. CVD is the most promising method for producing large-area, high-quality graphene, especially when using transition metal catalysts like copper. Each method is chosen based on the desired application, scalability, and quality requirements.
Key Points Explained:
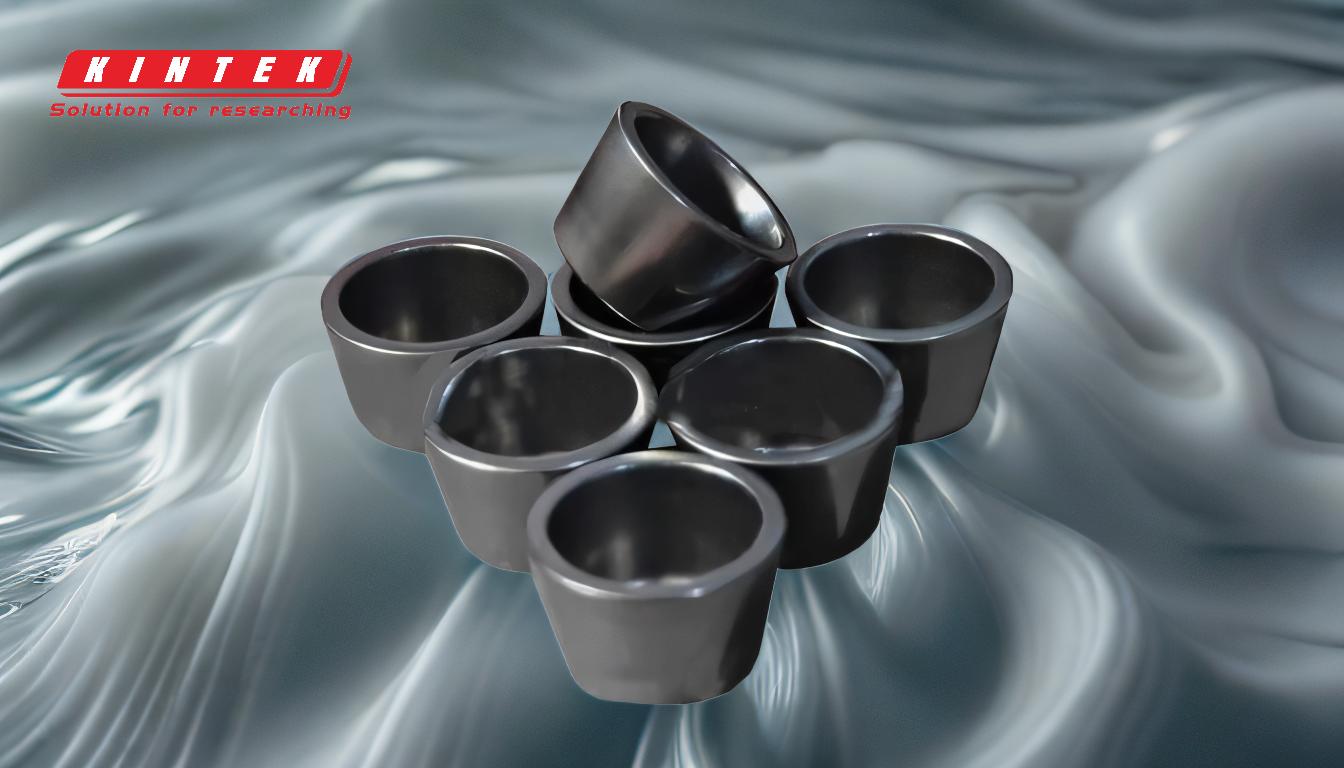
-
Mechanical Exfoliation
- Process: Involves peeling layers of graphene from graphite using adhesive tape or other mechanical means.
- Advantages: Produces high-quality graphene with minimal defects, ideal for fundamental research and small-scale applications.
- Limitations: Not scalable for industrial production, time-consuming, and yields small quantities of graphene.
- Applications: Primarily used in laboratory settings for studying graphene's intrinsic properties.
-
Liquid-Phase Exfoliation
- Process: Graphite is dispersed in a liquid medium and subjected to sonication or shear forces to separate graphene layers.
- Advantages: Scalable and suitable for mass production, relatively low cost.
- Limitations: Produces graphene with lower electrical conductivity and more defects compared to other methods.
- Applications: Used in applications where high electrical quality is not critical, such as conductive inks or composites.
-
Reduction of Graphene Oxide (GO)
- Process: Graphene oxide is chemically reduced to produce graphene, often using reducing agents like hydrazine or thermal reduction.
- Advantages: Cost-effective, scalable, and can produce graphene in large quantities.
- Limitations: The resulting graphene often contains residual oxygen and defects, which can affect its electrical and mechanical properties.
- Applications: Suitable for applications like energy storage, sensors, and polymer composites where high purity is not essential.
-
Chemical Vapor Deposition (CVD)
- Process: A transition metal substrate (e.g., copper or nickel) is exposed to hydrocarbon gases at high temperatures, causing graphene to form on the substrate.
- Advantages: Produces large-area, high-quality graphene with excellent electrical and mechanical properties.
- Limitations: Requires expensive equipment and precise control of conditions, making it less cost-effective for some applications.
- Applications: Ideal for electronic devices, transparent conductive films, and high-performance sensors.
-
Sublimation of Silicon Carbide (SiC)
- Process: Silicon atoms are sublimated from a single-crystal SiC substrate at high temperatures, leaving behind a graphene layer.
- Advantages: Produces high-quality graphene with good electrical properties.
- Limitations: High cost due to the expensive SiC substrate and energy-intensive process.
- Applications: Used in niche applications where high-quality graphene is required, such as high-frequency electronics.
-
Substrate Treatment in CVD
- Process: The substrate (e.g., copper) is chemically treated to optimize its surface morphology and catalytic activity, improving graphene growth.
- Advantages: Enhances the quality of graphene by reducing defects and increasing grain size.
- Limitations: Adds complexity to the CVD process.
- Applications: Used in advanced CVD processes to produce high-quality graphene for demanding applications like flexible electronics.
In summary, the choice of graphene preparation method depends on the intended application, with CVD being the most promising for high-quality, large-area production, while other methods like liquid-phase exfoliation and GO reduction are more suitable for cost-sensitive or less demanding applications.
Summary Table:
Method | Advantages | Limitations | Applications |
---|---|---|---|
Mechanical Exfoliation | High-quality graphene, minimal defects | Not scalable, time-consuming, small quantities | Laboratory research, small-scale applications |
Liquid-Phase Exfoliation | Scalable, low cost, suitable for mass production | Lower electrical quality, more defects | Conductive inks, composites |
Reduction of Graphene Oxide (GO) | Cost-effective, scalable, large quantities | Residual oxygen, defects | Energy storage, sensors, polymer composites |
Chemical Vapor Deposition (CVD) | High-quality, large-area graphene, excellent properties | Expensive equipment, precise conditions required | Electronic devices, transparent conductive films, high-performance sensors |
Sublimation of Silicon Carbide (SiC) | High-quality graphene, good electrical properties | High cost, energy-intensive | High-frequency electronics |
Substrate Treatment in CVD | Enhanced graphene quality, reduced defects, larger grain size | Adds complexity to the CVD process | Flexible electronics, advanced CVD applications |
Need help selecting the right graphene preparation method for your project? Contact our experts today!