Vacuum deposition is a critical process in the fabrication of thin films, particularly for metal layers, and involves several techniques that operate under vacuum conditions to deposit materials onto substrates. The primary methods include Physical Vapor Deposition (PVD) and Chemical Vapor Deposition (CVD), with PVD being the most commonly used for metal layers. Within PVD, techniques such as thermal evaporation, sputtering, electron beam deposition, and pulsed laser deposition are widely employed. Each method has its unique advantages and is chosen based on the specific requirements of the application, such as film thickness, uniformity, and material properties.
Key Points Explained:
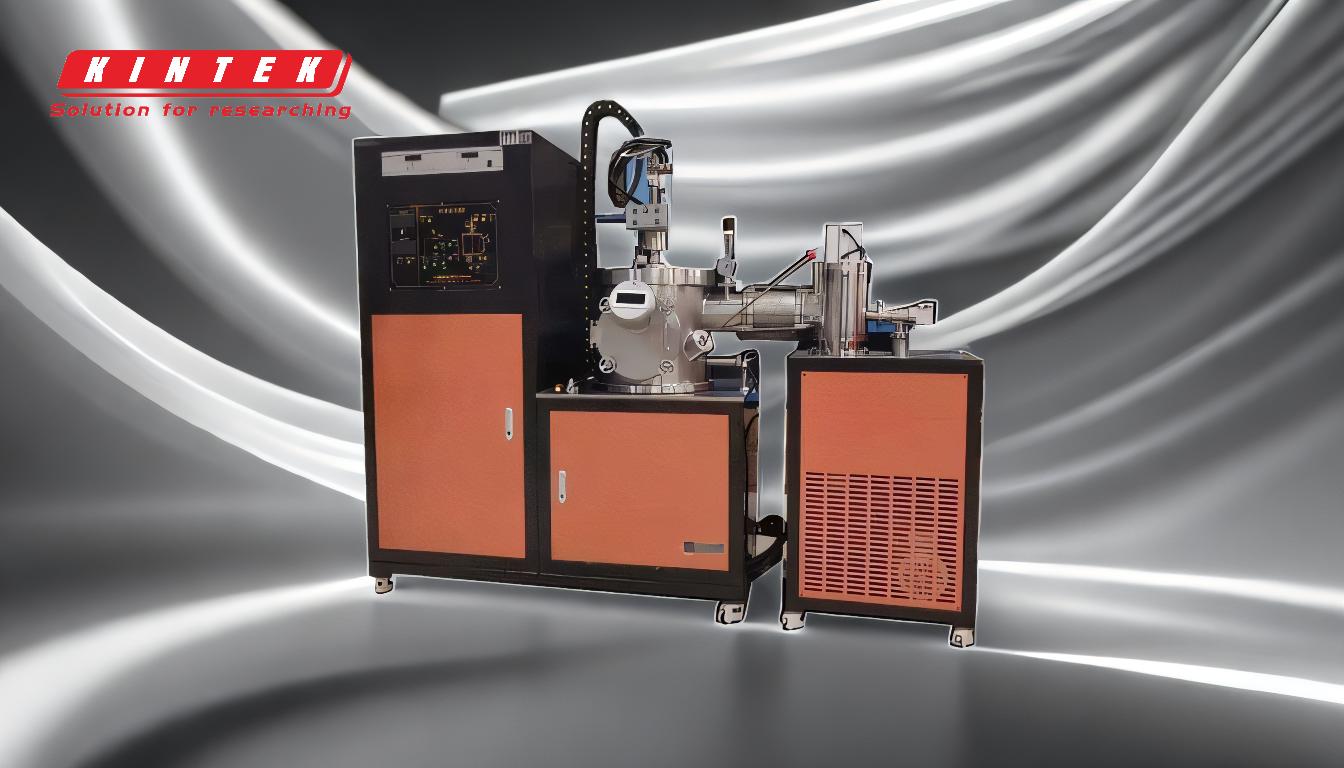
-
Physical Vapor Deposition (PVD):
- Thermal Evaporation: This technique involves heating the material to be deposited until it vaporizes in a vacuum. The vapor then condenses on the substrate to form a thin film. It is suitable for materials with low melting points and is widely used for depositing metals like aluminum and gold.
- Sputtering: In this method, high-energy ions bombard a target material, causing atoms to be ejected and deposited onto the substrate. Sputtering is versatile and can deposit a wide range of materials, including metals, alloys, and compounds. It provides excellent film uniformity and adhesion.
- Electron Beam Deposition: This technique uses a focused electron beam to heat and vaporize the material in a vacuum. It is particularly useful for depositing high-purity metals and materials with high melting points.
- Pulsed Laser Deposition (PLD): PLD uses a high-power laser to ablate material from a target, which then deposits onto the substrate. It is ideal for complex materials like oxides and multi-component films, offering precise control over film composition.
-
Chemical Vapor Deposition (CVD):
- CVD involves the use of chemical reactions to deposit a thin film on a substrate. A precursor gas is introduced into a vacuum chamber, where it reacts or decomposes on the heated substrate to form a solid film. CVD is suitable for depositing a wide range of materials, including metals, semiconductors, and insulators, and is known for producing high-quality, uniform films over large areas.
- Plasma-Enhanced Chemical Vapor Deposition (PECVD): This variant of CVD uses plasma to enhance the chemical reaction, allowing deposition at lower temperatures. It is particularly useful for depositing films on temperature-sensitive substrates.
-
Atomic Layer Deposition (ALD):
- ALD is a specialized form of CVD that deposits films one atomic layer at a time. It offers exceptional control over film thickness and uniformity, making it ideal for applications requiring ultra-thin, conformal coatings, such as in semiconductor manufacturing.
-
Other Techniques:
- Cathodic Arc Deposition: This method uses an electric arc to vaporize material from a cathode target, which then deposits onto the substrate. It is commonly used for depositing hard coatings like titanium nitride.
- Spray Pyrolysis: This technique involves spraying a solution onto a heated substrate, where it thermally decomposes to form a thin film. It is less common for metal deposition but is used for certain oxides and compounds.
Each of these methods has specific advantages and is chosen based on factors such as the material to be deposited, the desired film properties, and the application requirements. For example, sputtering is often preferred for its versatility and ability to deposit high-quality films, while thermal evaporation is favored for its simplicity and cost-effectiveness for certain metals. Understanding these techniques helps in selecting the most appropriate method for a given application in metal layer vacuum deposition.
Summary Table:
Technique | Key Features | Applications |
---|---|---|
Thermal Evaporation | Low melting point materials, simple, cost-effective | Aluminum, gold deposition |
Sputtering | Versatile, excellent uniformity, strong adhesion | Metals, alloys, compounds |
Electron Beam Deposition | High-purity metals, high melting point materials | High-purity metal films |
Pulsed Laser Deposition | Precise control, complex materials | Oxides, multi-component films |
CVD | High-quality, uniform films, large areas | Metals, semiconductors, insulators |
PECVD | Lower temperature deposition, temperature-sensitive substrates | Thin films on sensitive materials |
ALD | Atomic-level control, ultra-thin, conformal coatings | Semiconductor manufacturing |
Cathodic Arc Deposition | Hard coatings, electric arc vaporization | Titanium nitride coatings |
Spray Pyrolysis | Solution-based, thermal decomposition | Oxides, certain compounds |
Need help selecting the right vacuum deposition technique for your application? Contact our experts today!