Industrial heating is a critical process in various industries, including manufacturing, food processing, and chemical production. The choice of heating method depends on factors such as energy efficiency, cost, environmental impact, and the specific requirements of the application. Common options for industrial heating include electric heating, gas heating, steam heating, and renewable energy-based systems. Each method has its advantages and limitations, making it essential to evaluate the specific needs of the application before selecting the most suitable option.
Key Points Explained:
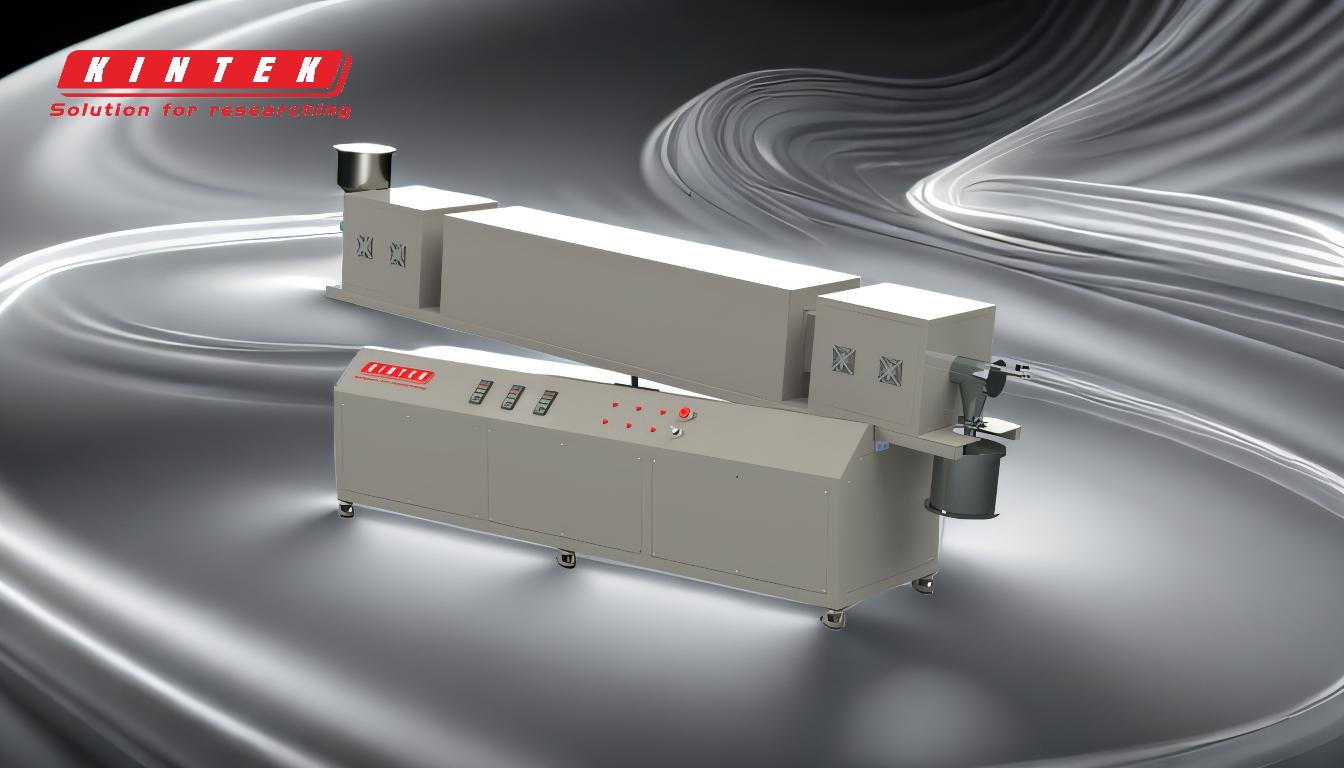
-
Electric Heating
- How it works: Electric heating uses electrical energy to generate heat through resistance, induction, or infrared technologies.
-
Advantages:
- High efficiency and precise temperature control.
- Clean and environmentally friendly, as it produces no direct emissions.
- Suitable for applications requiring uniform heating, such as in laboratories or small-scale manufacturing.
-
Limitations:
- High operational costs due to electricity prices.
- Limited suitability for large-scale industrial processes due to energy consumption constraints.
-
Applications:
- Small-scale manufacturing, food processing, and laboratory equipment.
-
Gas Heating
- How it works: Gas heating systems burn natural gas or propane to produce heat, which is then transferred to the process or material.
-
Advantages:
- Cost-effective for large-scale operations due to the lower cost of natural gas.
- High heat output, making it suitable for heavy industrial applications.
- Rapid heating capabilities.
-
Limitations:
- Environmental concerns due to greenhouse gas emissions.
- Requires proper ventilation and safety measures to prevent gas leaks or combustion hazards.
-
Applications:
- Metal processing, glass manufacturing, and large-scale food production.
-
Steam Heating
- How it works: Steam heating systems use steam generated from boilers to transfer heat to industrial processes.
-
Advantages:
- Efficient heat transfer due to the high thermal capacity of steam.
- Versatile and can be used for both heating and humidification.
- Suitable for processes requiring consistent and uniform heat distribution.
-
Limitations:
- High initial investment in boiler systems and infrastructure.
- Maintenance-intensive due to the complexity of steam systems.
-
Applications:
- Chemical processing, textile manufacturing, and power generation.
-
Renewable Energy-Based Heating
- How it works: Renewable energy sources, such as solar thermal, biomass, or geothermal energy, are used to generate heat for industrial processes.
-
Advantages:
- Environmentally sustainable and reduces carbon footprint.
- Long-term cost savings due to the use of free or low-cost energy sources.
- Government incentives and subsidies may be available for renewable energy projects.
-
Limitations:
- High initial setup costs and infrastructure requirements.
- Dependence on weather conditions (e.g., solar thermal systems).
-
Applications:
- Food processing, paper manufacturing, and district heating systems.
-
Infrared Heating
- How it works: Infrared heating uses electromagnetic radiation to directly heat objects or surfaces without heating the surrounding air.
-
Advantages:
- Energy-efficient and provides rapid heating.
- Precise and localized heating, reducing energy waste.
- Suitable for processes requiring surface heating or drying.
-
Limitations:
- Limited to applications where direct heating is feasible.
- May require specialized equipment and setup.
-
Applications:
- Paint curing, plastic welding, and drying processes.
-
Induction Heating
- How it works: Induction heating uses electromagnetic fields to generate heat within conductive materials, such as metals.
-
Advantages:
- Fast and efficient heating with precise control.
- Clean and safe, as it does not involve open flames or combustion.
- Suitable for applications requiring localized heating.
-
Limitations:
- High equipment costs and limited to conductive materials.
- Requires specialized knowledge for setup and operation.
-
Applications:
- Metal forging, heat treatment, and semiconductor manufacturing.
-
Microwave Heating
- How it works: Microwave heating uses electromagnetic waves to generate heat within materials, particularly those with high dielectric properties.
-
Advantages:
- Rapid and uniform heating.
- Energy-efficient for specific materials.
- Suitable for processes requiring internal heating.
-
Limitations:
- Limited to materials that absorb microwave energy.
- High equipment costs and safety concerns.
-
Applications:
- Food processing, chemical synthesis, and material drying.
-
Heat Pumps
- How it works: Heat pumps transfer heat from a lower-temperature source to a higher-temperature sink using a refrigeration cycle.
-
Advantages:
- Energy-efficient and environmentally friendly.
- Can provide both heating and cooling.
- Suitable for low- to medium-temperature applications.
-
Limitations:
- Limited to applications with moderate temperature requirements.
- High initial investment and maintenance costs.
-
Applications:
- Space heating, water heating, and industrial drying.
-
Combined Heat and Power (CHP) Systems
- How it works: CHP systems generate electricity and capture waste heat for industrial heating processes.
-
Advantages:
- High overall energy efficiency.
- Reduces energy costs and carbon emissions.
- Suitable for large-scale industrial facilities.
-
Limitations:
- High initial investment and infrastructure requirements.
- Requires careful planning and integration.
-
Applications:
- Power plants, chemical processing, and district heating.
-
Thermal Oil Heating
- How it works: Thermal oil heating systems use heated oil to transfer heat to industrial processes.
-
Advantages:
- High-temperature capabilities without high-pressure requirements.
- Uniform heat distribution and precise temperature control.
- Suitable for processes requiring consistent high temperatures.
-
Limitations:
- High maintenance and operational costs.
- Risk of oil degradation and leakage.
-
Applications:
- Chemical processing, plastic manufacturing, and asphalt production.
By carefully evaluating the specific requirements of the industrial process, including temperature range, energy efficiency, environmental impact, and cost considerations, the most suitable heating method can be selected to optimize performance and sustainability.
Summary Table:
Heating Method | Advantages | Limitations | Applications |
---|---|---|---|
Electric Heating | High efficiency, precise control, clean, no emissions | High operational costs, limited for large-scale processes | Small-scale manufacturing, food processing, lab equipment |
Gas Heating | Cost-effective, high heat output, rapid heating | Environmental concerns, requires safety measures | Metal processing, glass manufacturing, large-scale food production |
Steam Heating | Efficient heat transfer, versatile, uniform heat distribution | High initial investment, maintenance-intensive | Chemical processing, textile manufacturing, power generation |
Renewable Energy | Sustainable, reduces carbon footprint, long-term cost savings | High setup costs, weather-dependent | Food processing, paper manufacturing, district heating |
Infrared Heating | Energy-efficient, rapid heating, precise and localized | Limited to direct heating, specialized equipment required | Paint curing, plastic welding, drying |
Induction Heating | Fast, efficient, precise, clean, safe | High equipment costs, limited to conductive materials | Metal forging, heat treatment, semiconductor manufacturing |
Microwave Heating | Rapid, uniform heating, energy-efficient | Limited to microwave-absorbing materials, high equipment costs | Food processing, chemical synthesis, material drying |
Heat Pumps | Energy-efficient, environmentally friendly, heating and cooling | Limited to moderate temperatures, high initial investment | Space heating, water heating, industrial drying |
CHP Systems | High energy efficiency, reduces costs and emissions | High initial investment, requires careful planning | Power plants, chemical processing, district heating |
Thermal Oil Heating | High-temperature capabilities, uniform heat distribution, precise control | High maintenance costs, risk of oil degradation | Chemical processing, plastic manufacturing, asphalt production |
Need help choosing the right industrial heating method? Contact our experts today for tailored solutions!