Annealing is a heat treatment process used to alter the physical and sometimes chemical properties of a material, typically metals, to increase its ductility and reduce its hardness, making it more workable. The process involves three main stages: Recovery, Recrystallization, and Grain Growth. Each stage is crucial for achieving the desired material properties, and the process requires precise control over temperature and cooling rates to ensure the material achieves the intended structural changes.
Key Points Explained:
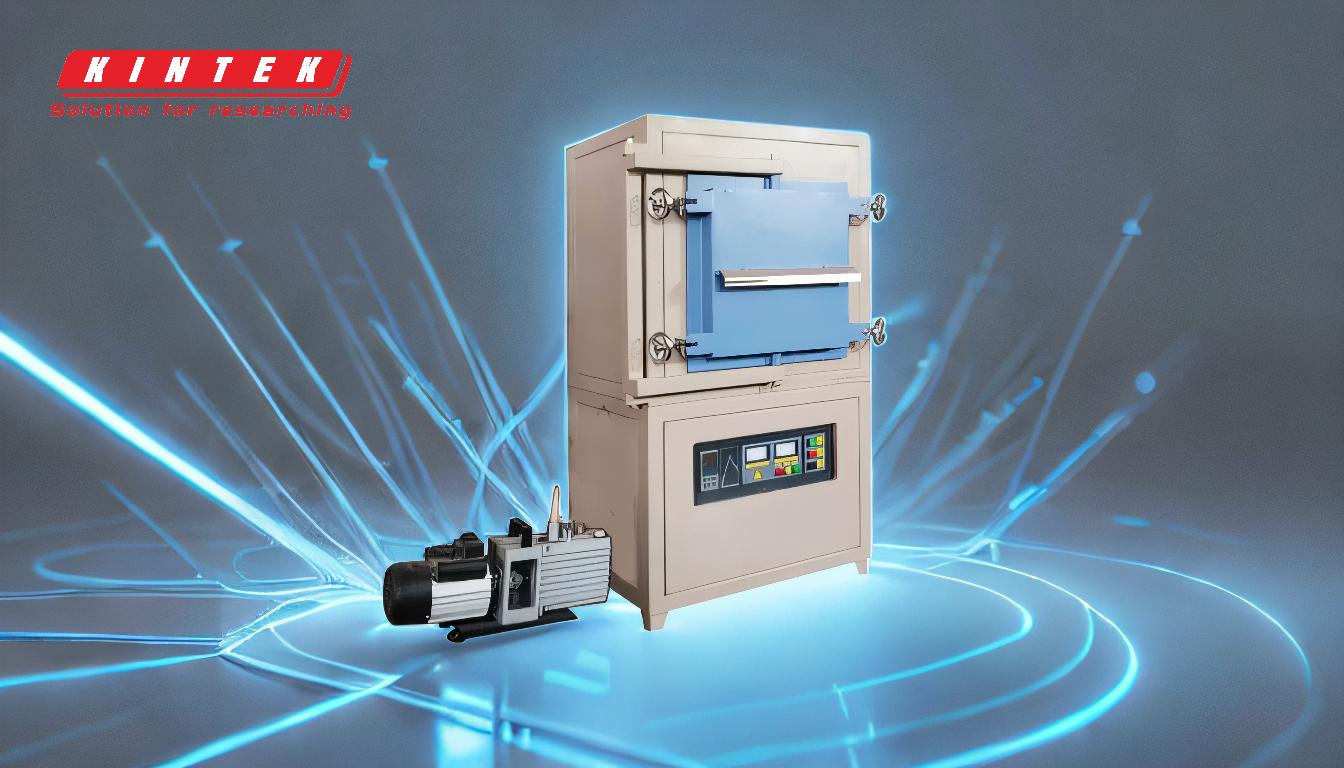
-
Heating to a Specific Temperature:
- Purpose: The primary requirement for annealing is heating the metal to a specific temperature where its crystalline structure becomes fluid but remains in a solid state. This temperature varies depending on the type of metal and its specific alloy composition.
- Importance: Heating to the correct temperature is crucial because it allows the internal stresses and defects within the metal to be relieved. This stage sets the foundation for the subsequent stages of annealing.
-
Holding at Temperature:
- Purpose: After reaching the desired temperature, the metal must be held at that temperature for a specific period. This holding time allows for the defects in the material to repair themselves through a process known as recovery.
- Importance: The holding time is critical because it ensures that the metal undergoes sufficient recovery, which is the first stage of annealing. During recovery, dislocations in the metal's structure are reduced, leading to a decrease in internal stresses.
-
Controlled Cooling:
- Purpose: After the holding period, the metal is allowed to cool slowly back to room temperature. This slow cooling rate is essential to produce a more ductile crystalline structure.
- Importance: Controlled cooling is vital because it prevents the formation of new stresses and allows the metal to achieve a more uniform and refined grain structure. Rapid cooling, on the other hand, could lead to the formation of a brittle structure, which is undesirable for most applications.
-
Stages of Annealing:
- Recovery: This is the first stage where the metal is heated to a temperature below its recrystallization point. During this stage, the internal stresses are relieved, and the dislocations in the metal's structure are reduced.
- Recrystallization: In this stage, the metal is heated to a temperature above its recrystallization point. New, stress-free grains begin to form, replacing the deformed grains from the previous stage.
- Grain Growth: The final stage involves holding the metal at a temperature where the newly formed grains can grow. This stage is controlled to ensure that the grains do not grow too large, which could negatively impact the metal's mechanical properties.
-
Material-Specific Requirements:
- Importance: Different metals and alloys have specific annealing requirements, including temperature ranges and cooling rates. For example, the annealing temperature for steel is different from that of aluminum or copper.
- Considerations: The specific requirements for annealing must be carefully considered based on the material's properties and the desired outcome. This includes understanding the material's phase diagram and the effects of different temperatures on its microstructure.
-
Equipment and Environment:
- Importance: The equipment used for annealing, such as furnaces, must be capable of maintaining precise temperature control and uniform heating. The environment within the furnace should also be controlled to prevent oxidation or other surface reactions that could affect the metal's properties.
- Considerations: The choice of equipment and the environment in which annealing is performed can significantly impact the quality of the annealed material. Proper insulation, temperature monitoring, and atmosphere control are essential for achieving consistent results.
In summary, the requirements for annealing involve precise control over heating, holding, and cooling processes, as well as understanding the specific needs of the material being treated. Each stage of the annealing process plays a critical role in achieving the desired material properties, and careful attention must be paid to the equipment and environment to ensure successful outcomes.
Summary Table:
Stage | Purpose | Importance |
---|---|---|
Heating | Heat metal to a specific temperature for crystalline structure fluidity. | Relieves internal stresses and defects, setting the foundation for annealing. |
Holding | Maintain temperature to allow defect recovery. | Ensures sufficient recovery, reducing dislocations and internal stresses. |
Cooling | Slowly cool metal to room temperature. | Prevents new stresses, achieving a uniform and refined grain structure. |
Recovery | Relieve internal stresses and reduce dislocations. | Prepares the metal for recrystallization. |
Recrystallization | Form new, stress-free grains. | Replaces deformed grains, improving material properties. |
Grain Growth | Allow newly formed grains to grow under controlled conditions. | Ensures grains do not grow too large, maintaining mechanical properties. |
Optimize your annealing process with expert guidance—contact us today for tailored solutions!