Refractory materials are essential in high-temperature industrial processes, and their selection depends on specific requirements such as thermal conductivity, corrosion resistance, thermal shock resistance, ease of installation, and maintenance. The choice of refractory material is also influenced by the specific process and environment, such as the type of kiln or furnace, the materials being processed, and the desired energy efficiency. For example, low-iron alumina or magnesium-spinel bricks are used in iron ore reduction kilns, while magnesite bricks are preferred in cement kilns. Additionally, crucibles require extremely high-temperature resistance, chemical stability, and compatibility with the materials they contain to prevent contamination. Multi-layer insulation designs, such as those using lightweight alumina ceramic fiber and insulation boards, are also critical for reducing heat loss and energy consumption.
Key Points Explained:
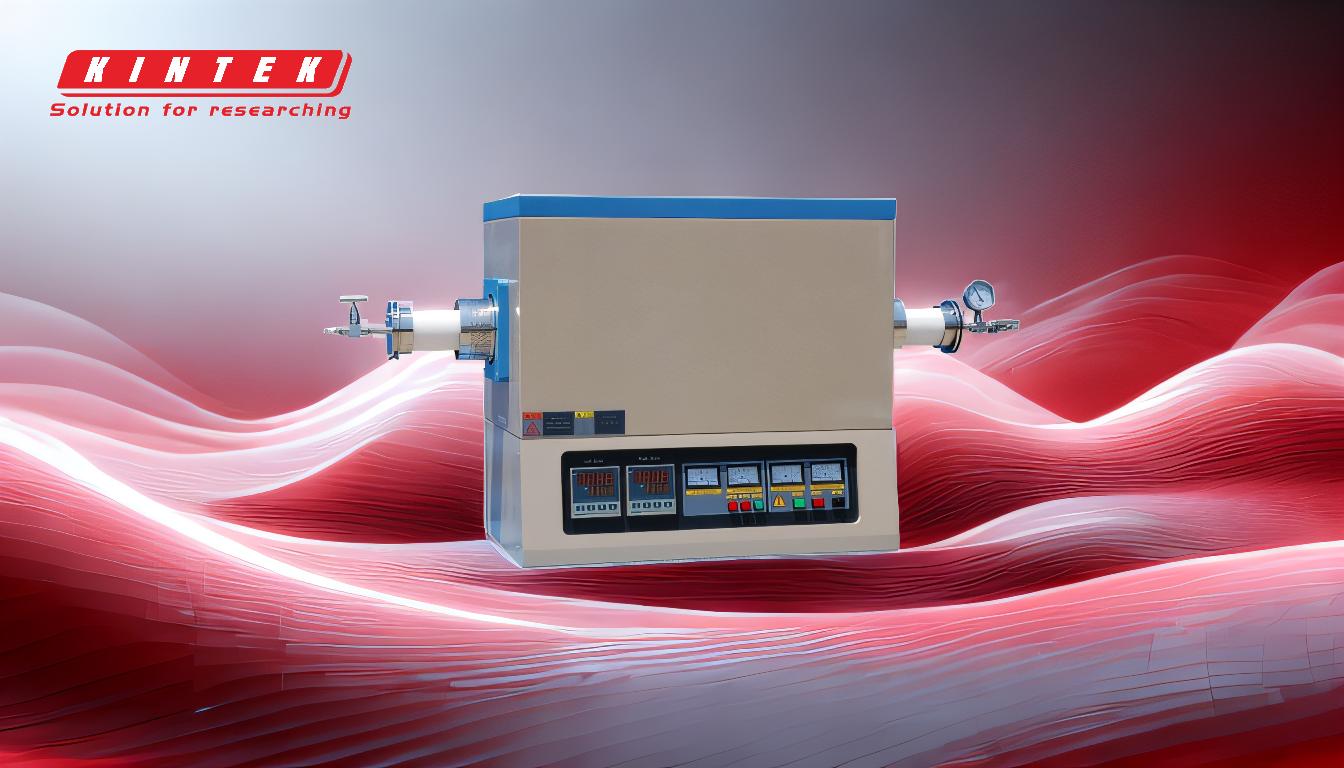
-
Low Thermal Conductivity:
- Refractory materials must have low thermal conductivity to minimize heat loss and improve energy efficiency. This is particularly important in high-temperature environments like kilns and furnaces, where maintaining consistent temperatures is crucial. For example, multi-layer insulation designs using lightweight alumina ceramic fiber and insulation boards are effective in reducing heat loss.
-
Resistance to Corrosion:
- Refractories must withstand chemical reactions with the materials they come into contact with, such as molten metals or slag. This is especially critical in processes like iron ore reduction or cement production, where the materials can be highly corrosive. Low-iron alumina or magnesium-spinel bricks are often used in such environments due to their chemical stability.
-
Thermal Shock Resistance:
- Refractory materials must endure rapid temperature changes without cracking or degrading. Thermal shock resistance is vital in processes where temperatures fluctuate significantly, such as in furnaces or kilns. Materials like magnesite bricks are commonly used in cement kilns because of their ability to withstand thermal stress.
-
Ease of Installation and Maintenance:
- Refractory linings should be easy to install and maintain to reduce downtime and operational costs. This includes considerations like modular designs or pre-fabricated components that can be quickly replaced or repaired. A stable refractory lining that is easy to maintain ensures long-term reliability and cost-effectiveness.
-
Material-Specific Requirements:
- The choice of refractory material depends on the specific process and environment. For example:
- In iron ore reduction kilns, low-iron alumina or magnesium-spinel bricks are used due to their resistance to high temperatures and corrosive materials.
- In cement kilns, magnesite bricks are preferred for their thermal shock resistance and durability.
- Crucibles require materials with extremely high-temperature resistance and chemical compatibility to prevent contamination of the melts.
- The choice of refractory material depends on the specific process and environment. For example:
-
Insulation Design:
- Multi-layer insulation designs, such as those incorporating lightweight alumina ceramic fiber and high-quality insulation boards, are essential for reducing heat loss and energy consumption. These designs also ensure that the refractory material does not contain harmful components like asbestos, making them safer and more environmentally friendly.
-
Chemical and Physical Stability:
- Refractory materials must maintain their structural integrity and chemical composition under extreme conditions. For example, crucibles must have a melting point higher than the materials they contain and be chemically compatible to avoid reactions that could lead to deterioration or contamination.
By considering these key points, purchasers can select refractory materials that meet the specific needs of their industrial processes, ensuring efficiency, durability, and cost-effectiveness.
Summary Table:
Key Factor | Importance | Example Materials |
---|---|---|
Low Thermal Conductivity | Minimizes heat loss, improves energy efficiency | Lightweight alumina ceramic fiber, insulation boards |
Resistance to Corrosion | Withstands chemical reactions with molten metals or slag | Low-iron alumina, magnesium-spinel bricks |
Thermal Shock Resistance | Endures rapid temperature changes without cracking | Magnesite bricks |
Ease of Installation | Reduces downtime and operational costs | Modular designs, pre-fabricated components |
Material-Specific Needs | Tailored to the process (e.g., iron ore reduction, cement production) | Low-iron alumina for iron ore kilns, magnesite bricks for cement kilns |
Insulation Design | Reduces heat loss, improves energy efficiency | Multi-layer insulation with alumina ceramic fiber |
Chemical Stability | Prevents contamination and maintains structural integrity | Crucibles with high-temperature resistance and chemical compatibility |
Need help selecting the perfect refractory materials for your application? Contact our experts today for tailored solutions!