Spark Plasma Sintering (SPS) is an advanced sintering technique that utilizes pulsed direct current (DC) and uniaxial pressure to rapidly consolidate powders into dense and homogeneous bulk materials. The process involves passing an electrical current through a conductive die (typically graphite) and, if applicable, the sample itself, generating localized high temperatures and plasma discharges. This results in rapid heating, uniform temperature distribution, and efficient densification at lower temperatures compared to conventional sintering methods. Key parameters include heating rate, sintering temperature, applied pressure, pulse current characteristics, and the atmosphere (vacuum or controlled gas). These parameters are carefully controlled to achieve optimal material properties and microstructure.
Key Points Explained:
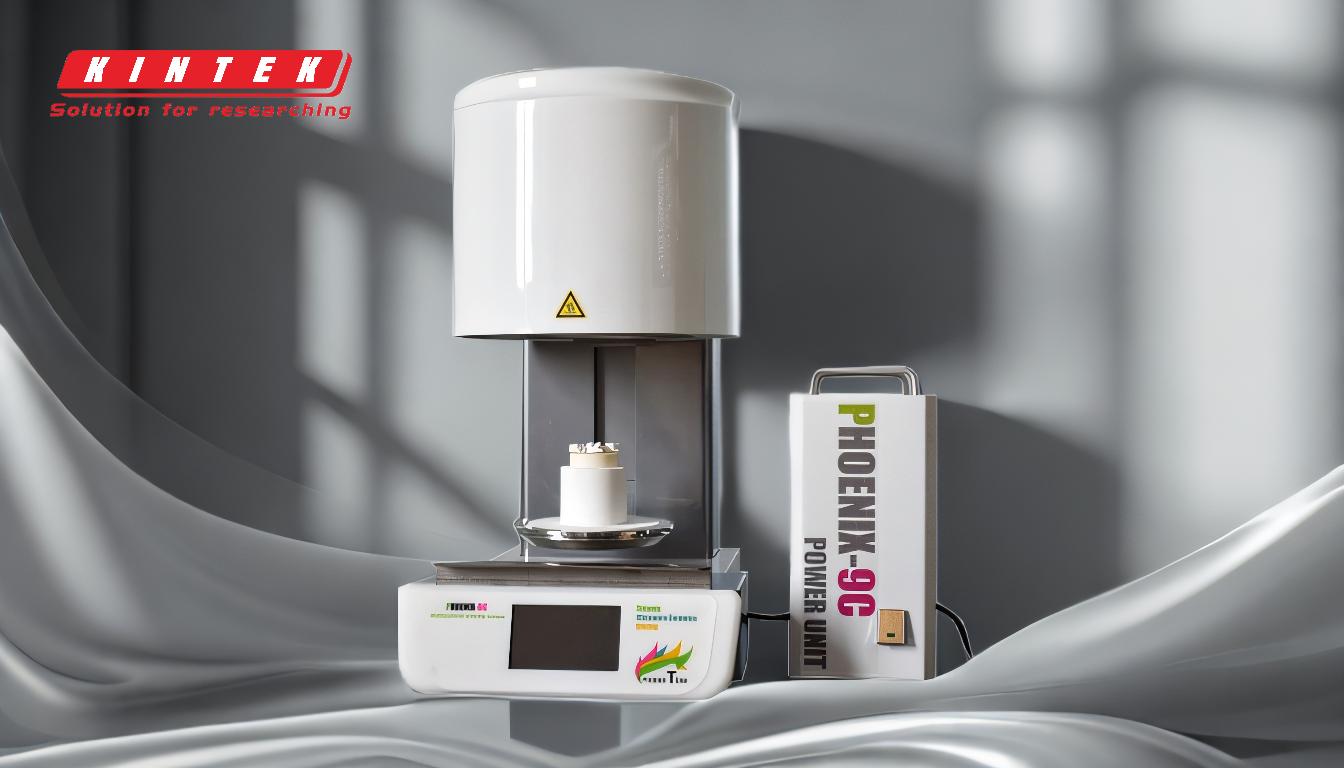
-
Heating Rate:
- The heating rate in SPS is significantly faster than in traditional sintering methods, often reaching hundreds of degrees per minute. This rapid heating minimizes grain growth and allows for the retention of fine microstructures.
- High heating rates are achieved by the direct passage of current through the die and sample, enabling internal and external heating simultaneously.
-
Sintering Temperature:
- SPS typically operates at lower sintering temperatures compared to conventional methods, often several hundred degrees lower. This is due to the localized heating and plasma generation at particle interfaces, which enhances diffusion and bonding.
- The sintering temperature is precisely controlled to ensure complete densification without excessive grain growth or material degradation.
-
Applied Pressure:
- Uniaxial pressure is applied during the sintering process to aid in particle rearrangement, plastic deformation, and densification. The pressure helps close pores and improve the mechanical properties of the final product.
- The applied pressure is typically in the range of 10-100 MPa, depending on the material and desired properties.
-
Pulse Current Characteristics:
- The pulsed DC current is a defining feature of SPS, generating plasma discharges between particles. This plasma enhances surface diffusion and boundary defect diffusion, promoting rapid sintering.
- The pulse duration, frequency, and amplitude are critical parameters that influence the sintering kinetics and final material properties.
-
Atmosphere:
- SPS is often conducted in a vacuum or controlled atmosphere (e.g., inert gas) to prevent oxidation and contamination of the material. This is particularly important for reactive or high-purity materials.
- The controlled atmosphere ensures the integrity of the sintered product and minimizes defects.
-
Equipment Components:
- The SPS system includes a furnace body, pressurization system, vacuum system, pulse DC power supply, control system, and safety features. The graphite die and water cooling system are essential for maintaining temperature uniformity and preventing overheating.
- Automated program control allows precise regulation of temperature, pressure, and current, ensuring reproducibility and quality.
-
Advantages of SPS:
- Rapid heating and cooling rates enable the production of materials with fine microstructures and enhanced properties.
- Lower sintering temperatures reduce energy consumption and minimize thermal stress on the material.
- The process is versatile and applicable to a wide range of materials, including ceramics, metals, and composites.
-
Applications:
- SPS is widely used in research and industry to fabricate advanced materials such as nanostructured ceramics, intermetallics, and functionally graded materials.
- The technique is particularly valuable for materials that are difficult to sinter using conventional methods due to high melting points or sensitivity to grain growth.
By carefully controlling these parameters, SPS enables the production of high-quality materials with tailored properties, making it a powerful tool in materials science and engineering.
Summary Table:
Parameter | Description |
---|---|
Heating Rate | Rapid heating (hundreds of degrees/min) minimizes grain growth. |
Sintering Temperature | Lower than conventional methods, ensuring densification without degradation. |
Applied Pressure | 10-100 MPa aids particle rearrangement and densification. |
Pulse Current | Generates plasma discharges, enhancing diffusion and bonding. |
Atmosphere | Vacuum or controlled gas prevents oxidation and contamination. |
Advantages | Fine microstructures, lower energy use, and versatility for various materials. |
Applications | Nanostructured ceramics, intermetallics, and functionally graded materials. |
Unlock the potential of Spark Plasma Sintering for your materials—contact our experts today!