The electric arc furnace (EAF) process is a critical method in steelmaking, primarily used for recycling scrap metal into high-quality steel. The process involves a series of stages, collectively known as the tap-to-tap cycle, which ensures efficient melting, refining, and casting of steel. These stages include furnace charging, melting, refining, deslagging, and tapping. Each stage plays a vital role in transforming scrap metal into usable steel, with the process relying on high-temperature electric arcs to achieve rapid melting. Below, the key stages of the electric arc furnace process are explained in detail.
Key Points Explained:
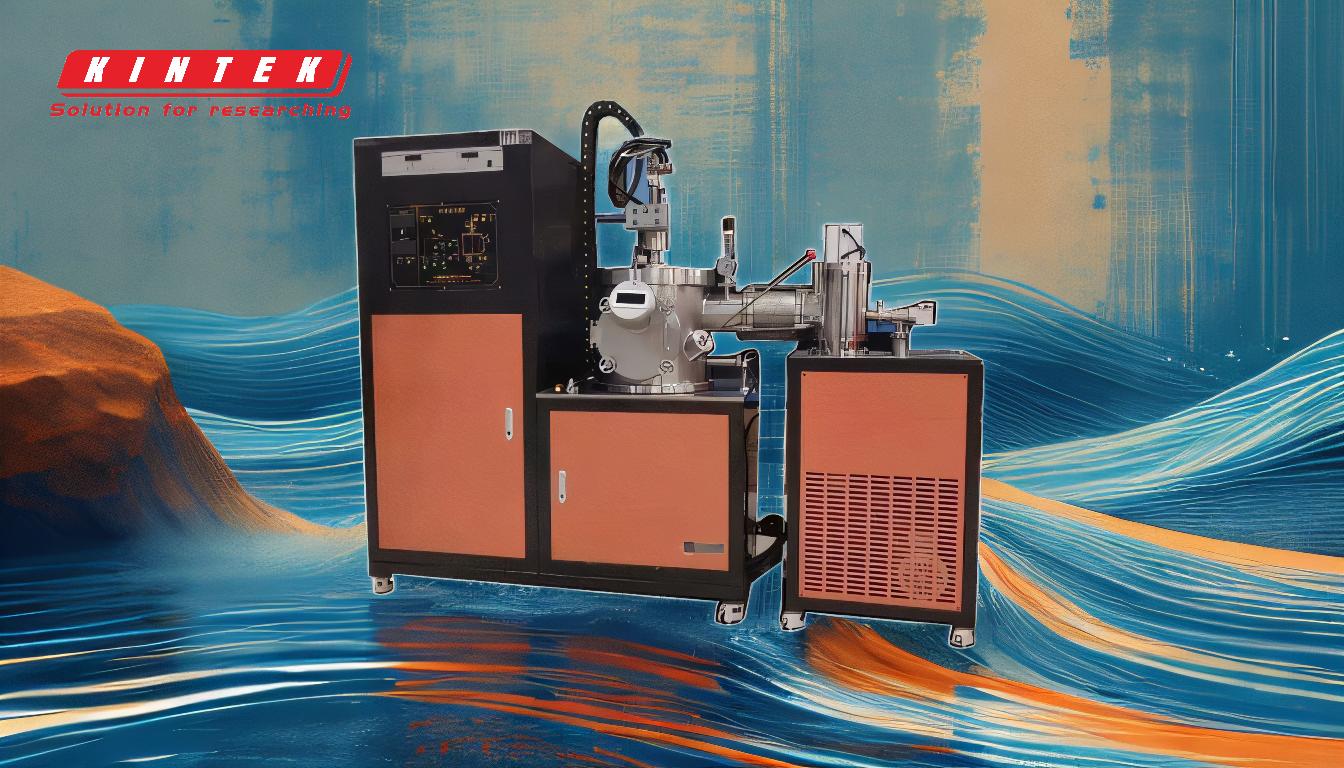
-
Furnace Charging:
- This is the initial stage where raw materials, primarily scrap metal, are loaded into the furnace.
- Scrap metal is often mixed with limestone to aid in slag formation, which helps remove impurities.
- The furnace is designed to handle large volumes of material, including slabs, beams, and shredded scrap.
- Proper charging ensures efficient melting and minimizes energy consumption.
-
Melting:
- Once the furnace is charged, electrodes are introduced into the metal, and an electric arc is generated between the electrodes and the metal.
- The arc produces extremely high temperatures, reaching up to 3275°F (1800°C), which rapidly melts the scrap metal.
- The melting process is energy-intensive, requiring approximately 350 to 370 kWh per ton of scrap.
- Oxygen may be injected during this stage to enhance the melting process and remove impurities.
-
Refining:
- After melting, the molten metal undergoes refining to adjust its chemical composition and remove impurities.
- Alloying elements may be added to achieve the desired steel grade.
- The refining process ensures the final product meets specific quality standards, including carbon content, alloy composition, and mechanical properties.
- Temperature control is critical during refining to avoid defects and ensure uniformity.
-
Deslagging:
- Slag, a byproduct of the melting and refining processes, is removed from the surface of the molten metal.
- Slag contains impurities such as oxides, phosphorous, and sulfur, which are separated from the steel.
- Deslagging is typically done by tilting the furnace or using specialized tools to skim off the slag.
- Proper deslagging ensures the final steel product is clean and free from contaminants.
-
Tapping:
- The final stage involves pouring the refined molten steel out of the furnace into a ladle or casting machine.
- Tapping must be carefully controlled to avoid spillage and ensure the correct temperature and composition of the steel.
- The molten steel is then transported to further processing, such as continuous casting or ingot casting, to produce finished steel products.
- The furnace is then prepared for the next cycle, starting with charging again.
-
Energy and Efficiency Considerations:
- The EAF process is highly energy-efficient compared to traditional blast furnaces, as it primarily uses electrical energy.
- Modern EAFs are equipped with advanced temperature control systems to optimize energy usage and reduce operational costs.
- The ability to recycle scrap metal makes the EAF process environmentally friendly, reducing the need for raw materials and minimizing waste.
-
Variations in EAF Processes:
- While the tap-to-tap cycle is the standard for most EAF operations, some specialized furnaces, such as vacuum non-self-consuming arc furnaces, follow additional stages like vacuum treatment and suction casting.
- These variations are used for specific applications, such as producing high-purity alloys or specialized steel grades.
By understanding these stages, equipment and consumable purchasers can better evaluate the requirements for maintaining and optimizing EAF operations, ensuring efficient and high-quality steel production.
Summary Table:
Stage | Key Details |
---|---|
Furnace Charging | Scrap metal and limestone are loaded into the furnace for efficient melting. |
Melting | Electric arcs heat scrap to 3275°F (1800°C), melting it rapidly. |
Refining | Chemical composition is adjusted, and impurities are removed for quality steel. |
Deslagging | Slag, containing impurities, is removed from the molten metal. |
Tapping | Refined steel is poured into a ladle or casting machine for further processing. |
Energy Efficiency | EAFs are energy-efficient, using ~350-370 kWh per ton of scrap. |
Optimize your steelmaking process with expert insights—contact us today!