Carbon nanotubes (CNTs) are synthesized and purified through a variety of methods, each with its own advantages and limitations. Traditional methods like laser ablation and arc discharge have been foundational, but chemical vapor deposition (CVD) has emerged as the dominant commercial process due to its scalability and efficiency. Emerging methods focus on sustainability, utilizing green or waste feedstocks such as carbon dioxide and methane. Purification techniques are equally critical, ensuring the removal of impurities and by-products to achieve high-quality CNTs. Below, we explore the synthesis and purification methods in detail.
Key Points Explained:
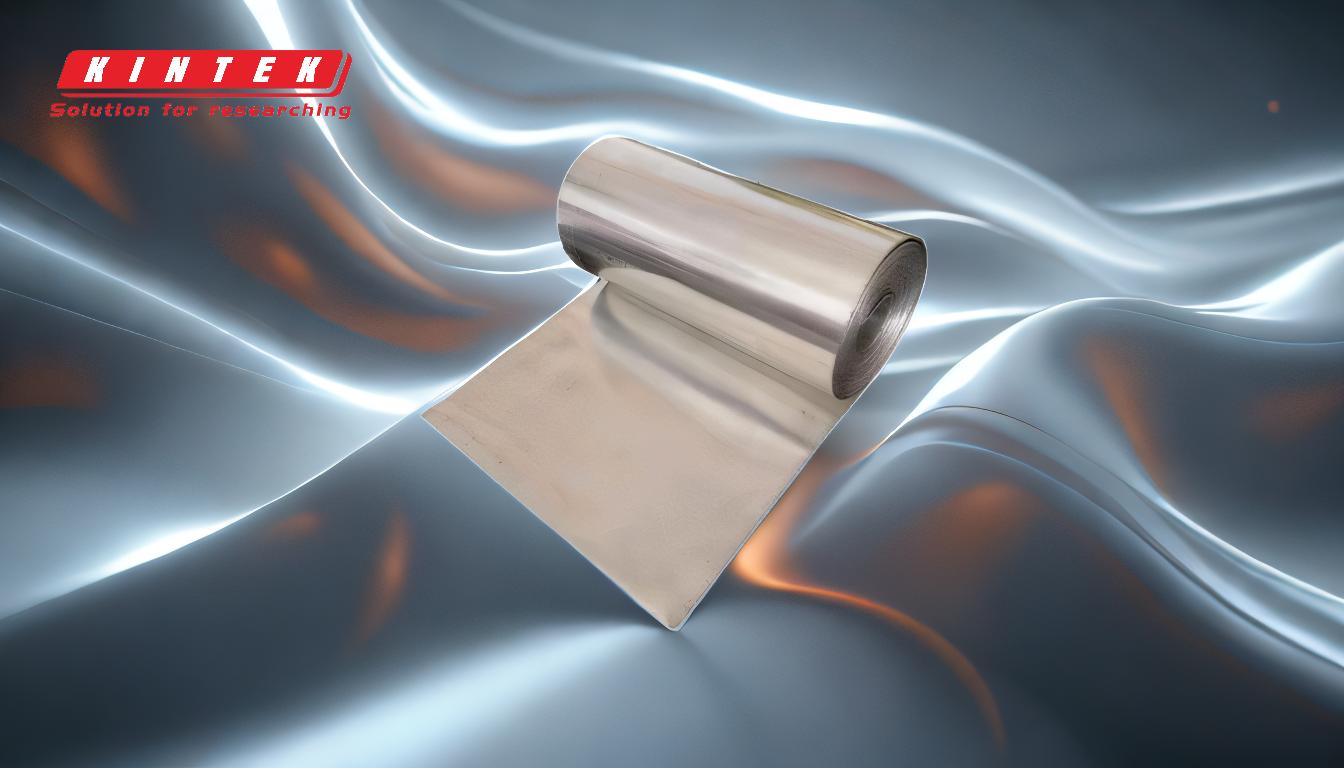
-
Traditional Synthesis Methods
-
Laser Ablation:
This method involves using a high-powered laser to vaporize a carbon target in the presence of a catalyst. The vaporized carbon atoms condense to form carbon nanotubes. While this method produces high-quality CNTs, it is energy-intensive and not suitable for large-scale production. -
Arc Discharge:
In this technique, an electric arc is generated between two graphite electrodes in an inert gas atmosphere. The high temperature causes carbon atoms to vaporize and form CNTs. Arc discharge is effective for producing multi-walled carbon nanotubes (MWCNTs) but often results in impurities that require extensive purification.
-
Laser Ablation:
-
Chemical Vapor Deposition (CVD)
- CVD is the most widely used commercial method for CNT synthesis. It involves decomposing a carbon-containing gas (e.g., methane or ethylene) over a metal catalyst at high temperatures. The carbon atoms deposit on the catalyst particles, forming nanotubes.
- Advantages:
- Scalable and cost-effective for large-scale production.
- Allows precise control over CNT properties, such as diameter and length.
- Limitations:
- Requires high temperatures and a controlled atmosphere.
- Catalyst residues may remain, necessitating purification.
-
Emerging Synthesis Methods
-
Green Feedstocks:
Researchers are exploring sustainable methods, such as using carbon dioxide captured by electrolysis in molten salts or methane pyrolysis. These approaches aim to reduce environmental impact and utilize waste materials. -
Hydrothermal and Sol-Gel Methods:
These chemical synthesis techniques are traditionally used for nanomaterials but are being adapted for CNTs. They involve reactions in aqueous solutions or gels, offering potential for controlled growth and functionalization.
-
Green Feedstocks:
-
Purification Methods
- Purification is essential to remove impurities like amorphous carbon, metal catalysts, and fullerenes. Common techniques include:
- Oxidation: Heating CNTs in air or oxygen to burn off impurities.
- Acid Treatment: Using strong acids (e.g., nitric acid) to dissolve metal catalysts and amorphous carbon.
- Filtration and Centrifugation: Separating CNTs based on size and density.
- Challenges:
- Purification can damage CNTs or alter their properties.
- Balancing purity and yield is critical for commercial applications.
- Purification is essential to remove impurities like amorphous carbon, metal catalysts, and fullerenes. Common techniques include:
-
Innovation in Functionalization and Integration
- Beyond synthesis and purification, CNTs are being functionalized to enhance their properties. This includes creating hybrid products with additives, forming highly conductive yarns, and integrating CNTs into composite materials.
- Functionalization methods include covalent bonding (e.g., attaching chemical groups to the CNT surface) and non-covalent interactions (e.g., wrapping CNTs with polymers).
In summary, the synthesis and purification of carbon nanotubes involve a combination of traditional and emerging methods, each tailored to specific applications and requirements. CVD remains the dominant commercial process, while green feedstocks and innovative functionalization techniques are paving the way for sustainable and advanced CNT applications. Purification remains a critical step to ensure the quality and performance of CNTs in various industries.
Summary Table:
Method | Advantages | Limitations |
---|---|---|
Laser Ablation | Produces high-quality CNTs | Energy-intensive, not scalable for large production |
Arc Discharge | Effective for multi-walled CNTs (MWCNTs) | Impurities require extensive purification |
Chemical Vapor Deposition (CVD) | Scalable, cost-effective, precise control over CNT properties | High temperatures, catalyst residues may remain |
Green Feedstocks | Sustainable, reduces environmental impact | Still in research phase, limited commercial adoption |
Purification Techniques | Removes impurities (e.g., amorphous carbon, metal catalysts) | Can damage CNTs or alter properties, balancing purity and yield is challenging |
Interested in high-quality carbon nanotubes for your applications? Contact our experts today to learn more!