Chemical Vapor Deposition (CVD) is a versatile and widely used technique for depositing thin films on substrates. It involves exposing the substrate to volatile precursors, which decompose or react to form a solid film. The main CVD techniques include thermal CVD, plasma-enhanced CVD (PECVD), and laser CVD (LCVD). These techniques vary in terms of pressure, temperature, and the use of additional energy sources like plasma or lasers. Other methods include Atmospheric Pressure CVD (APCVD), Low Pressure CVD (LPCVD), Ultrahigh Vacuum CVD (UHVCVD), Metal-Organic CVD (MOCVD), and Laser-Induced CVD (LICVD). Each technique has specific applications and advantages, such as conformal thickness, high purity, and higher deposition rates.
Key Points Explained:
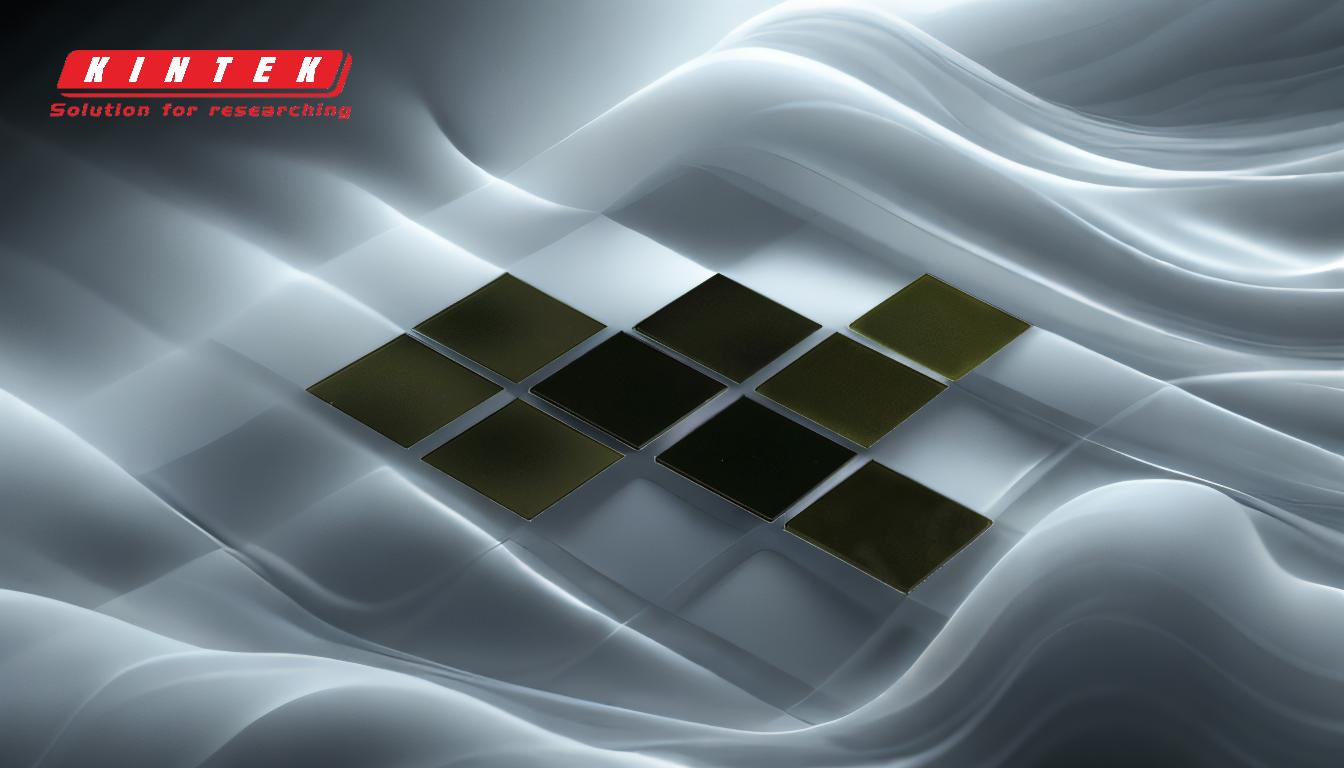
-
Thermal CVD:
- Description: Thermal CVD relies on high temperatures to decompose or react volatile precursors on the substrate surface.
- Process: The substrate is heated in a reaction chamber, and precursor gases are introduced. The heat causes the gases to decompose or react, forming a solid film on the substrate.
- Applications: Commonly used in semiconductor manufacturing, coatings, and thin-film deposition.
- Advantages: High purity, conformal coverage, and high deposition rates.
- Limitations: Requires high temperatures, which may not be suitable for all substrates.
-
Plasma-Enhanced CVD (PECVD):
- Description: PECVD uses plasma to enhance the chemical reaction at lower temperatures compared to thermal CVD.
- Process: A plasma is generated in the reaction chamber, which provides the energy needed for the precursors to decompose or react. This allows the process to occur at lower temperatures.
- Applications: Widely used in the production of thin films for microelectronics, solar cells, and optical coatings.
- Advantages: Lower processing temperatures, better control over film properties, and the ability to deposit films on temperature-sensitive substrates.
- Limitations: More complex equipment and process control compared to thermal CVD.
-
Laser CVD (LCVD):
- Description: LCVD uses a laser to locally heat the substrate, causing the precursors to decompose or react in a highly localized area.
- Process: A focused laser beam is directed at the substrate, providing the necessary energy for the chemical reaction. This allows for precise control over the deposition area.
- Applications: Used in microfabrication, additive manufacturing, and the creation of complex geometries.
- Advantages: High precision, localized deposition, and the ability to create complex patterns.
- Limitations: Limited to small areas, slower deposition rates, and requires precise control of the laser.
-
Atmospheric Pressure CVD (APCVD):
- Description: APCVD occurs at atmospheric pressure and typically requires high temperatures.
- Process: The reaction chamber is maintained at atmospheric pressure, and the substrate is heated to high temperatures to facilitate the reaction.
- Applications: Used in the production of coatings, thin films, and semiconductor devices.
- Advantages: Simpler equipment compared to low-pressure systems, suitable for large-scale production.
- Limitations: High temperatures may limit the types of substrates that can be used.
-
Low Pressure CVD (LPCVD):
- Description: LPCVD operates at reduced pressures, allowing for lower reaction temperatures.
- Process: The reaction chamber is evacuated to reduce pressure, and the substrate is heated to a lower temperature compared to APCVD.
- Applications: Commonly used in the semiconductor industry for depositing silicon dioxide, silicon nitride, and polysilicon films.
- Advantages: Lower temperatures, better film uniformity, and higher purity.
- Limitations: Requires vacuum equipment, which can be more complex and expensive.
-
Ultrahigh Vacuum CVD (UHVCVD):
- Description: UHVCVD operates at extremely low pressures, often in the range of 10^-9 to 10^-6 torr.
- Process: The reaction chamber is evacuated to ultrahigh vacuum levels, and the substrate is heated to facilitate the reaction.
- Applications: Used in the production of high-quality thin films for advanced semiconductor devices and research applications.
- Advantages: Extremely high purity, minimal contamination, and precise control over film properties.
- Limitations: Requires sophisticated vacuum equipment and is more expensive.
-
Metal-Organic CVD (MOCVD):
- Description: MOCVD uses metal-organic compounds as precursors, which are decomposed to deposit metal-containing films.
- Process: Metal-organic precursors are introduced into the reaction chamber, where they decompose at elevated temperatures to form the desired film.
- Applications: Widely used in the production of compound semiconductors, such as GaN, InP, and GaAs.
- Advantages: High precision, ability to deposit complex multi-layer structures, and excellent control over film composition.
- Limitations: Requires careful handling of metal-organic precursors, which can be toxic and flammable.
-
Laser-Induced CVD (LICVD):
- Description: LICVD uses a laser to induce the chemical reaction, allowing for localized and precise deposition.
- Process: A laser beam is focused on the substrate, providing the energy needed for the precursors to react and form a film.
- Applications: Used in microfabrication, additive manufacturing, and the creation of complex patterns.
- Advantages: High precision, localized deposition, and the ability to create complex geometries.
- Limitations: Limited to small areas, slower deposition rates, and requires precise control of the laser.
Each of these CVD techniques has its own set of advantages and limitations, making them suitable for different applications. The choice of technique depends on the specific requirements of the deposition process, including the type of substrate, desired film properties, and production scale.
Summary Table:
CVD Technique | Key Features | Applications | Advantages | Limitations |
---|---|---|---|---|
Thermal CVD | High-temperature decomposition of precursors. | Semiconductor manufacturing, coatings, thin-film deposition. | High purity, conformal coverage, high deposition rates. | Requires high temperatures, may not suit all substrates. |
Plasma-Enhanced CVD | Uses plasma for lower-temperature reactions. | Microelectronics, solar cells, optical coatings. | Lower temperatures, better film control, suitable for sensitive substrates. | Complex equipment and process control. |
Laser CVD | Laser heats substrate for localized deposition. | Microfabrication, additive manufacturing, complex geometries. | High precision, localized deposition, complex patterns. | Limited to small areas, slower deposition rates, precise laser control needed. |
Atmospheric CVD | Operates at atmospheric pressure, high temperatures. | Coatings, thin films, semiconductor devices. | Simpler equipment, suitable for large-scale production. | High temperatures may limit substrate types. |
Low Pressure CVD | Reduced pressure allows lower reaction temperatures. | Silicon dioxide, silicon nitride, polysilicon films in semiconductors. | Lower temperatures, better film uniformity, higher purity. | Requires vacuum equipment, more complex and expensive. |
Ultrahigh Vacuum CVD | Operates at extremely low pressures (10^-9 to 10^-6 torr). | Advanced semiconductor devices, research applications. | Extremely high purity, minimal contamination, precise control. | Sophisticated vacuum equipment, expensive. |
Metal-Organic CVD | Uses metal-organic precursors for metal-containing films. | Compound semiconductors (GaN, InP, GaAs). | High precision, complex multi-layer structures, excellent composition control. | Toxic and flammable precursors, careful handling required. |
Laser-Induced CVD | Laser induces chemical reaction for precise deposition. | Microfabrication, additive manufacturing, complex patterns. | High precision, localized deposition, complex geometries. | Limited to small areas, slower deposition rates, precise laser control needed. |
Need help selecting the right CVD technique for your application? Contact our experts today for personalized guidance!